Link to Item
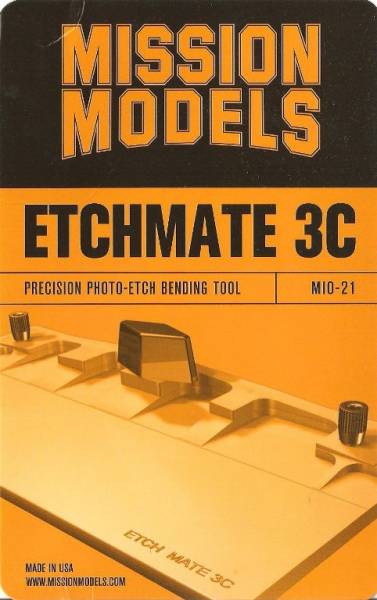
If you have comments or questions please post them here.
Thanks!
A good review! I knew as soon as I saw this thing that it would be crap, and your review just confirms my suspicions. You can't make a PE bending tool out of plastic, even high quality plastic, without sacrificing the precision edge of the clamp. If you do make the edge razor sharp, the plastic will bend and distort in no time.
I know making anything out of metal these days is expensive, but Mission Models should have scrapped the whole thing instead of lowering their standards and going with plastic. Selling this thing is a disservice to their less knowledgeable customers who will end up with a piece of expensive junk. Ausfwerks has done just this and discontinued (unfortunately) their Fender Bender because steel is so expensive these days, and they didn't want to release a lesser product out of inferior materials.
I get what you're saying, but I read somewhere that Missions Models flat-out said they went with plastic because metal was too expensive. Sure, they could go with metal and pass the cost on to us, but I would assume they chose plastic because they would sell more units and make more money overall.
And not to go too off-topic, but Mission Models customer service has been really crappy as of late. Their site can run like sloth at times, they don't seem to update their stock very often, and they take forever to answer emails, if they ever answer them at all.
Yeah you're right that is off-topic! I have been doing business with Mission for several years now and have never had anything but excellent service. No site problems for me, and I haven't found their stock situation to be any different than other online stores, and in many cases better. My e-mails have almost always been answered in a timely fashion, and if not there was a good explanation. If you have an axe to grind with Mission take it up with them somewhere else please!
Mike
Michael,
I'm sorry you were disappointed with my review, but quite frankly I'd rather be disappointed with a review than disappointed in a purchase. At least you only lost a few minutes of your time reading my review and responding in this thread, whereas I lost a bit more than time.
And I suppose that I am not knowledgeable or experienced enough to understand that this tool should only be used with aftermarket PE sets, if Mission Models stated this I would have known. Does this mean the sets I have that are included with my DML and Trumpeter kits need to be dealt with differently? Ah, I'm only being a smart-alec here, Michael, I know what you meant. And, yes, I realize this is not a sheetmetal brake.
Sorry once again, but I do not see what military aircraft has to do with the Etch-mate. They share the same material, but I fail to see how that makes this tool better? I'm pretty sure if I dropped my Etch-Mate off my roof it wouldn't break, though the composite material did not help me achieve sharp bends.
Yes, the price of metals has gone up dramatically, but the amount used in this tool before machining is not that great, do not see that as an excuse.
Michael, I did not purchase this tool and perform the review immediately. I practiced quite a bit with it before running my tests, believe me I wanted it to work well. I was not looking for faults, since I already purchased this tool I wanted it to do what it was advertised to do.
Also, I did state in my review that I used etched bend lines with the same result. What I did not mention was that I also annealed test samples, with like results. I also did not mention that lapping the bottoms of the finger plate and squaring the fronts of the fingers give better results, as this should not need to be done by the consumer and this was strictly an out of box review.
I sincerely hope I did not sound rude here, Michael, that was not my intention. Just wanted to clarify things a bit. It's not my style to put people down, especially people I do not know, to make my point. Cheers.
Michael I am always open to another opinion, may I request your opinion on the ETCHMATE 3C, listing its strong/weak and its good /bad points from your experience having been involved in its design. As for who is right or wrong that can’t be answered as it’s an opinion formed from their personal experience of a product. I myself rarely use PE because I have hands like shovels and old tired eyes (half the time I cant tell the PE from the frame) but if there is a tool out there that will make using PE easy I will invest in one, however I also want to know what it can’t do rather than just what it can.
I would like to say a very big thank you to James for clearly pointing out its weaknesses from his experience with the ETCHMATE 3C and I would also like to say a big thank you to Michael for pointing out its limitations and making very clear that practice makes all the difference. In addition these two reviews have given me a very clear picture (at least to my mind) of what to purchase for what purpose and that the ETCHMATE 3C has its place, a place that was not made clear prior to me reading the reviews here.
![]() |