Link to Item
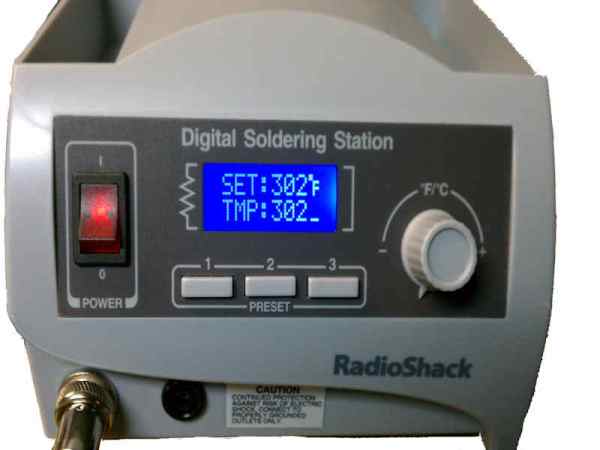
If you have comments or questions please post them here.
Thanks!
Could not get it to solder anything. It would melt the solder easy enough, but when I touch it to the pieces to be joined, the melted solder would solidify again
I also picked up some tinning stuff at Radio Shack which might of helped with heat transfer.
Quoted TextCould not get it to solder anything. It would melt the solder easy enough, but when I touch it to the pieces to be joined, the melted solder would solidify againQuoted TextHow were you doing it? No amount of heat and flux will help if you don't have the right technique. Trick is to heat the parts from one side and add your soldier to the other. In other words don't use the soldiering iron to melt the soldier, but use the heat from the iron to heat up whatever you are trying to join, and use that heat to melt the soldier. In the end, if done right, you will use very little soldier and flux.
Scott good catch on the issue Matthew was talking about with the solder solidifying. I totally missed that!
Yes you heat the metal to allows the solder to flow. I use several techniques when working with PE. One technique to applying solder is to add just a Tiny Bit to your soldering tip and then the tip is applied to the work piece and when the metal heats up the solder will flow into the joints to secure the pieces together. That is why flux is so important to allowing a good solder flow as well as bond. Another way I apply solder is to flux the parts while they in secured in place and add just a tiny piece of solder to the area to be joined and then apply the soldering tip on the opposite side from where the Tiny Bit of solder was placed. When the metal heats up and the solder melts it flows through the joint and towards the soldering tip.
With the second method where I place a tiny piece of solder I take a x-acto knife and cut a Very Small piece off the soldering spool.
I use a liquid rosin free flux and a very fine diameter solid core solder for working with photo etch.
Quoted TextI also picked up some tinning stuff at Radio Shack which might of helped with heat transfer.
Not sure what you mean by "tinning stuff" when I was taking Electronics Engineering you tinned your soldiering iron by melting some soldier on the tip as it was heating up, and also just before you turn your iron off...melt some soldier on the tip and leave it there while it cools down. This will protect your tips and your iron will be ready for your next session. Don't waste your money on the idiots at Radio Shack or The Source here in Canada.
Gas irons are more expensive over all...but convenient, as you aren't tethered to a wall socket. Temps are a little hard to control and be precise with as compared to an electric one, especially a digital one.
![]() |