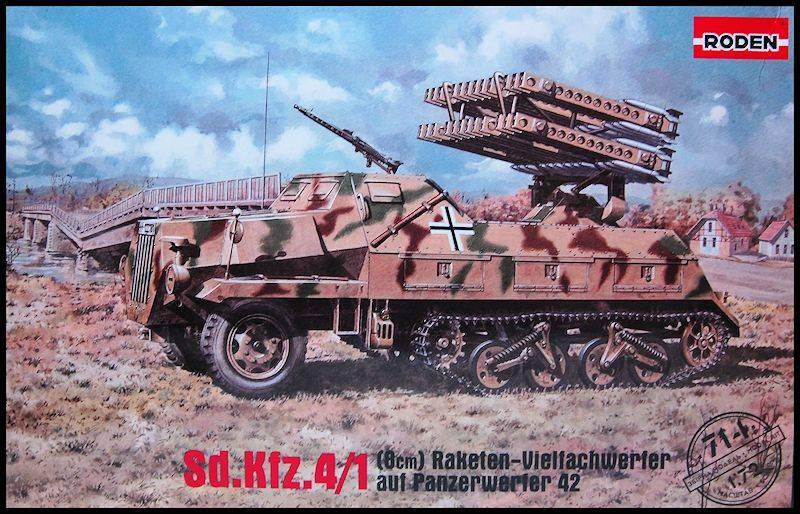
The review can be accessed here.
For the review I built the launcher assembly only and just demonstrated it dry fitted on the body. Now for the rest of the model, from the beginning.
Step 1 starts out with the engine casing in two halves with a wacking great chunk of styrene on each, which I snapped off with pliers:
The separate fan was a bit of an odd shape in that the blades weren't at 90deg to each other, but it ends up inserted into a circular recess in the radiator (15A) anyway. That had a big ejector hole in it which I removed by lots of sanding with the glass nail file (my current favourite tool). End of step 1 is below. That's the distributor cap and the ignition coil lying just in front of the engine.
Step 2 takes us to this:
In the second photo above I don't know if that pipe/hose thing that comes out from behind the radiator is meant to be at that angle, but it's one of those slightly frustrating things where you never get a drawing of the item completed in the instructions, except for from the opposite side. I'm guessing it's meant to exit through the floor somewhere though. So the engine will get a little clean up when it is all set, and possibly a bit more detailing, prior to painting.
For those that like 1/35 scale models, you can pretend those increments are inches. For the rest of us, they're centimetres. I didn't have any Canadian coins handy.

For now I skipped over steps 3 to 6 which is wheels and suspension as I'd had enough of really tiny fiddly pieces for a long Friday evening, and moved straight to the upper bodywork in step 7 with its relatively big pieces.
As mentioned in the review, the various doors are all separate from the body, but joined together in pairs, so to show them open we need to cut them in half, thin them down and eventually add some details to the insides where necessary. So this is the bonnet (hood) doors separated, with the right hand one most of the way to being filed down with the glass file; I suppose some might prefer to simply re-fabricate these doors out of thinner styrene sheet or brass, the shapes are all very simple.
Left hand one shows the ejector pit and the chamfered edge:
Similarly the chamfered edge of the engine compartment opening was removed and the sides thinned down:
And finally for now, the same halving and thinning process is started with the doors in the top of the superstructure; top one is already nice and thin:
The interior detailing that was provided for the 15cm rocket launcher doesn't apply to this version, although the parts are all present, as that was largely racks for the bigger rockets. In this model they have left that part of the interior largely bare, presumably as there is no evidence of what it looked like. I will have to improvise in order to show these roof doors open, but I have some ideas. If anyone else has thoughts on it, please feel free to share...
