Hi all.
I'm having a little difficulty with my Badger Renegade brush. It's fine for doing large jobs where detail isn't required. But when I try to do any fine lines I'm afraid it gets unpredictable. Works fine, then suddenly loads of paint, then fine again, then nothing. If it did the same every time I could work with it. I thought it was a cleaning issue so I bought a sonic cleaner -but no still the same.
I cant get proper atomisation below 15 psi. So that's the lowest pressure i work with.
Anyone got any ideas on a fix?
I thought about buying a new brush for detail. An Iwata CM-C Plus. I know its supposed to be the Rolls Royce. Bit is it worth the cash, and will it fix my lack of talent? ;-)
Thanks
AFV Painting & Weathering
Answers to questions about the right paint scheme or tips for the right effect.
Answers to questions about the right paint scheme or tips for the right effect.
Hosted by Darren Baker, Matthew Toms
airbrush

Blackstoat

Joined: October 15, 2012
KitMaker: 568 posts
Armorama: 561 posts

Posted: Saturday, June 01, 2013 - 11:31 AM UTC

sdk10159

Joined: December 08, 2005
KitMaker: 556 posts
Armorama: 433 posts

Posted: Saturday, June 01, 2013 - 11:42 AM UTC
Quoted Text
Hi all.
I'm having a little difficulty with my Badger Renegade brush. It's fine for doing large jobs where detail isn't required. But when I try to do any fine lines I'm afraid it gets unpredictable. Works fine, then suddenly loads of paint, then fine again, then nothing. If it did the same every time I could work with it. I thought it was a cleaning issue so I bought a sonic cleaner -but no still the same.
I cant get proper atomisation below 15 psi. So that's the lowest pressure i work with.
Anyone got any ideas on a fix?
I thought about buying a new brush for detail. An Iwata CM-C Plus. I know its supposed to be the Rolls Royce. Bit is it worth the cash, and will it fix my lack of talent? ;-)
Thanks
Andy,
Try thinning your paint a little more. Then try and lower the PSI.
Steve

Blackstoat

Joined: October 15, 2012
KitMaker: 568 posts
Armorama: 561 posts

Posted: Saturday, June 01, 2013 - 11:49 AM UTC
Forgot to put that in. Thanks Sreve.
I'm usually thinning between 1:1 and 1:4 paint:thinner.
Thanks Steve, I thought that too. But any thinner and I'm spider webbing
I'm usually thinning between 1:1 and 1:4 paint:thinner.
Thanks Steve, I thought that too. But any thinner and I'm spider webbing

sdk10159

Joined: December 08, 2005
KitMaker: 556 posts
Armorama: 433 posts

Posted: Saturday, June 01, 2013 - 11:56 AM UTC
Quoted Text
Forgot to put that in. Thanks Sreve.
I'm usually thinning between 1:1 and 1:4 paint:thinner.
Thanks Steve, I thought that too. But any thinner and I'm spider webbing
Are you using acrylic or enamel paint? and what are you using to thin?

Blackstoat

Joined: October 15, 2012
KitMaker: 568 posts
Armorama: 561 posts

Posted: Saturday, June 01, 2013 - 12:01 PM UTC
Tamiya acrylic. Tamiya acrylic or lacquer thinner.
Thanks bud
Thanks bud

sdk10159

Joined: December 08, 2005
KitMaker: 556 posts
Armorama: 433 posts

Posted: Saturday, June 01, 2013 - 12:14 PM UTC
Quoted Text
Tamiya acrylic. Tamiya acrylic or lacquer thinner.
Thanks bud
1 more thing to try. I use Tamiya acrylic's and I thin them with 91% rubbing alcohol thinned to the consistency of milk roughly 50/50. I've never had any issues with my airbrush.
I don't know if you can buy that over in the UK. If you can, give it a shot - it's much cheaper that Tamiya thinner.
Steve

imatanker

Joined: February 11, 2011
KitMaker: 1,654 posts
Armorama: 1,565 posts
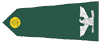
Posted: Saturday, June 01, 2013 - 08:27 PM UTC
Quoted Text
Forgot to put that in. Thanks Sreve.
I'm usually thinning between 1:1 and 1:4 paint:thinner.
Thanks Steve, I thought that too. But any thinner and I'm spider webbing
Andy,spider webbing is usually caused from your paint being too thick.The Renegade is gravity feed,Yes?Let me ask you a question.Are you thinning your paint in the AB cup? If you are then there will be a little bit of paint down in the fluid passages that never gets thinned.Try thinning your paint in a separate container,and then pour it into the AB and try that.Let me know how you make out


Blackstoat

Joined: October 15, 2012
KitMaker: 568 posts
Armorama: 561 posts

Posted: Saturday, June 01, 2013 - 11:39 PM UTC
Thanks Jeff, thought of that. I do mix in the AB cup (gravity fed), but I put the thinner in first. Then I toot it through until I get a consistent colour/viscosity.
I'm thinking perhaps I'm getting a little drying at the tip. Just enough to restrict the flow? Perhaps if I try mixing in a retarder for detailed stuff?
Thanks for your help
I'm thinking perhaps I'm getting a little drying at the tip. Just enough to restrict the flow? Perhaps if I try mixing in a retarder for detailed stuff?
Thanks for your help

M4A1Sherman

Joined: May 02, 2013
KitMaker: 4,403 posts
Armorama: 4,078 posts

Posted: Sunday, June 02, 2013 - 01:46 AM UTC
Hi, All! I definitely agree with imatanker- Mix your paint and thinner in a SEPARATE CONTAINER before you put it into your color cup. It'll save you a lot of headaches that steal time away from your work. ALWAYS make sure that you've properly stirred your paint in it's original bottle. My own personal preference in paints are TESTORS MODEL MASTER II ENAMELS. I agree with the 50-50 paint-to-thinner ratio; the mix should be the same consistency as milk for your main colors... In my own experience, I find that the petroleum-based products flow easier and paint-clogs are virtually non-existent for me. For airbrushing enamels, I like to use the TESTORS AIRBRUSH THINNERS FOR ENAMELS. I always add a drop or two of WINSOR-NEWTON FLAT VARNISH to the ENAMEL paint/thinner-mix that I've already transferred into my color cup. It helps to flow my paint, and also adds better durability once the paint has dried. I NEVER add the W/N FLAT VARNISH to acrylic paints...

imatanker

Joined: February 11, 2011
KitMaker: 1,654 posts
Armorama: 1,565 posts
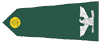
Posted: Sunday, June 02, 2013 - 02:44 AM UTC
Quoted Text
Thanks Jeff, thought of that. I do mix in the AB cup (gravity fed), but I put the thinner in first. Then I toot it through until I get a consistent colour/viscosity.
I'm thinking perhaps I'm getting a little drying at the tip. Just enough to restrict the flow? Perhaps if I try mixing in a retarder for detailed stuff?
Thanks for your help
If you are using X-20A for thinner,then yes,I would use a retarder.For what it's worth,I use Liquitex Slow-Dri Fluid Retarder.It works well with all the acrylics I use,Tamiya,Vallejo,and ModelMaster.Jeff T.
Oh,what size is your fluid tip?It has been my experence that the smaller the tip,the more prone to tip clogging it is


Blackstoat

Joined: October 15, 2012
KitMaker: 568 posts
Armorama: 561 posts

Posted: Sunday, June 02, 2013 - 04:10 AM UTC
Thanks Jeff, thought of that. I do mix in the AB cup (gravity fed), but I put the thinner in first. Then I toot it through until I get a consistent colour/viscosity.
I'm thinking perhaps I'm getting a little drying at the tip. Just enough to restrict the flow? Perhaps if I try mixing in a retarder for detailed stuff?
Thanks for your help
I'm thinking perhaps I'm getting a little drying at the tip. Just enough to restrict the flow? Perhaps if I try mixing in a retarder for detailed stuff?
Thanks for your help

DavidJG

Joined: June 16, 2013
KitMaker: 7 posts
Armorama: 7 posts

Posted: Monday, June 17, 2013 - 07:30 AM UTC
Hi,
I was tempted with a Iwata CMC plus but was advised against it for two reasons.
* Because it is so well engineered the paint / thinner mix has to be a perfect consistency, if it is out the brush will clog.
* It is not easy to use and can be tricky to control .. and as such no good for a very casual user like me.
I ended up buying a Iwata High Line HP - CH - it's great to use and have had no problems so far.
D
I was tempted with a Iwata CMC plus but was advised against it for two reasons.
* Because it is so well engineered the paint / thinner mix has to be a perfect consistency, if it is out the brush will clog.
* It is not easy to use and can be tricky to control .. and as such no good for a very casual user like me.
I ended up buying a Iwata High Line HP - CH - it's great to use and have had no problems so far.
D

retiredyank

Joined: June 29, 2009
KitMaker: 11,610 posts
Armorama: 7,843 posts

Posted: Monday, June 17, 2013 - 08:27 AM UTC
Do not thin it with IPA. IPA is the cause of pebbling. I have ruined many finishes, that way. Get the Tamiya acryl thinner or use glass cleaner. I thin it 1:1 and, occasionally, 4:5(paint:thinner). You won't believe the difference. Perfect finish, every time.
Posted: Monday, June 17, 2013 - 08:46 AM UTC
Hi Andy
I live in the UK. I don't use Tamiya thinners it's too expensive. I use window cleaner (not the vinegar type)for thinning my tamiya paint, and I mix in the cup same as you, and I put in my thinner 1st. I use a paint brush to mix it all when its in there, as some of the thick stuff will sink to the bottom. Once I have mixed with a brush I use the blowback to give it a final mix. For fine lines etc. try taking off the spray difuser on the tip of the gun, but be careful as the needle sticks out of the end. This allows for fine detail, BUT you need to thin your paint 4 or 5 to 1, that 4 thinners and 1 paint, and a slightly higher pressure too. I clean my brush with the same window cleaner with ammonia added (stinks but cleans the gun well). Check out you tube there are some really good videos of pros showing you the tricks.
Cheers Pete
I live in the UK. I don't use Tamiya thinners it's too expensive. I use window cleaner (not the vinegar type)for thinning my tamiya paint, and I mix in the cup same as you, and I put in my thinner 1st. I use a paint brush to mix it all when its in there, as some of the thick stuff will sink to the bottom. Once I have mixed with a brush I use the blowback to give it a final mix. For fine lines etc. try taking off the spray difuser on the tip of the gun, but be careful as the needle sticks out of the end. This allows for fine detail, BUT you need to thin your paint 4 or 5 to 1, that 4 thinners and 1 paint, and a slightly higher pressure too. I clean my brush with the same window cleaner with ammonia added (stinks but cleans the gun well). Check out you tube there are some really good videos of pros showing you the tricks.
Cheers Pete

SdAufKla

Joined: May 07, 2010
KitMaker: 2,238 posts
Armorama: 2,158 posts

Posted: Monday, June 17, 2013 - 12:38 PM UTC
Hi Andy,
Here's a rather "longish" reply, but hopefully, it's complete enough to help.
There are only a set number of variables that can be adjusted with any airbrush while using any paint. If we assume that mechanical problems have been ruled out and the paint and reducer are compatible, then these are the variables that you are working with:
1) Air pressure – controlled at the compressor and or airbrush trigger.
(If you're using a single-action AB and a diaphragm-type compressor, then air pressure is set and does not change. All other variables must be changed to accommodate this set pressure.)
2) Paint flow – controlled by the airbrush needle and tip by way of the adjusting nut or trigger and tip and needle size.
3) Paint viscosity – controlled by the operator when he reduces (i.e. thins) the paint for spraying.
4) Distance from the airbrush tip to the painted surface – controlled by the operator.
5) Speed that the airbrush is moved across the painted surface – controlled by the operator.
6) Drying time of the paint – controlled by paint viscosity, the reducer (thinner), paint volume, humidity and temperature. When the drying time is too short, all kinds of problems can result.
All of these variables can be combined in differing degrees to successfully accomplish most of the same general effects. This means that no single variable is the most important. (Even a single-action AB and diaphragm-type compressor combination allows most of these variables to be adjusted.)
For example, if the paint viscosity is too great (i.e. the paint is too "thick") and the AB will not spray, the operator can 1) increase the air pressure, or 2) he can open the tip up, or 3) he can reduce the paint, or 4) he can do some combination of all three.
However, there are some "rules of thumb" that can be turned to when sorting out problems or trying to achieve some particular effect. These rules tell us how the AB system works:
1) Fine lines are painted close to the surface.
2) Wider patterns are painted farther away from the surface.
3) The closer the tip is to the surface, the less paint flow and air pressure is needed.
4) The farther away the tip is from the surface, the more paint flow and pressure are needed.
5) Higher air pressure can spray heavier viscosity ("thicker") paint.
6) Lower air pressure can spray lighter or lower viscosity ("thinner") paint.
7) Heavier viscosity paint requires a larger tip opening.
8) Lighter viscosity paint requires a smaller tip opening.
9) Greater paint flow requires a faster surface speed and or greater distance.
10) Smaller paint flow allows a slower surface speed and or closer distance.
Using these rules of thumb, we can see that to paint fine lines: the paint viscosity is low, the air pressure low, the paint flow low, the tip is close to the surface and the speed across the surface should be moderate. Because the paint viscosity is low, it is sometimes necessary to follow the same line several times to get good coverage (a lot depends on the back ground and line colors).
Overspray is usually caused by air pressure that's too high coupled with high paint flow and too much distance from the surface. Tighter spray patterns are achieved by moving the tip closer which may require less paint volume, lower air pressure, lighter viscosity, and faster surface speed.
(Note: High pressure "tight" patterns require very fast surface speeds and close distances. The faster surface speed demands a practiced eye and a steady hand to "free hand" the desired pattern. However, the "high pressure" technique will allow for heavier viscosity paint producing better single coat coverage.)
Spattering around the edges of the paint spray pattern is usually caused by too much paint flow, too low air pressure, too low paint viscosity or a combination of all three. Reduce the paint flow, increase the air pressure and or increase the paint viscosity or, again, make a slight change in all three.
Spattering from paint build up on the AB tip is caused by 1) opening the paint flow on a double-action AB before starting the air flow, or 2) too low paint viscosity with the needle open from the tip, or 3) too low air pressure for the paint flow. Sometimes acrylic paints that are drying too fast will build up on the paint tip and create conditions for drops on the tip to also form. Adjusting the paint viscosity and using a drying retarder can sometimes help. Usually you can't do much to lower the temperature or increase the humidity, but if you can, that can also help here.
Paint runs are caused by too much paint (too high volume, too much flow, and too little distance) applied in too small an area (too slow surface speed). Gravity then pulls the paint downward creating the run. Lower the volume, decrease the flow, increase the distance or do all three to cure runs.
"Spidering" is a special case of paint runs radiating out from a single point rather than down in the direction of gravity. The cause is the same – too much paint volume on the surface at the point of the runs, in this case, by holding the AB stationary in one place, too close to the surface while starting the spraying. This loads the surface with a puddle of paint which the air pressure pushes into runs radiating from the point where the AB is directed.
The cure for "spidering" can be any one or a combination of the following: Keep the AB moving across the surface, lower the air pressure, increase the distance, and or lower the paint flow.
"Orange Peel" or "white, powdery flat coats" is caused by the atomized paint partially drying between the AB and the surface. The reason is too high air pressure, too much distance from the surface, paint drying time is too fast. The cures are: reduce air pressure and or close the distance. This combination of cures often requires speeding up the surface speed since the volume of paint onto the surface is increased. Usually, the paint-reducer (i.e. the "thinner" used) combination cannot be changed. However, the reducing ratio can sometimes be changed to increase the viscosity causing the paint to dry slightly slower (air pressure might have to be increased as a result of the higher viscosity).
When trouble shooting AB problems, the key is to understand how the system works and how changing any one variable will effect the rest. Usually, changing only one of the first three variables will produce some positive results, but possibly not achieve the desired effect. Although you can make slight changes in several variables that will combine to fix a problem, often you will not get the final effect that you want going that route and sometimes you will create a new and different problem.
So, for example, if the AB will not spray (and mechanical issues have been ruled out) then either: Reduce the paint more to make it "thinner," OR increase the air pressure, OR open up the tip more. At the same surface distance and speed (on a test piece) you should get some acceptable result. If you don't get enough improvement to get some positive result, stick with the same change just more of it until you do.
(If you max out the possible change in that variable with no positive improvement at all, you've likely misidentified the kind of problem. Best to go back to square one and start all over.)
Once the AB is spraying, then you can then judge the effects and adjust either or both of the other two variables (pressure or flow) to get an improvement towards the desired effect. Then judge how speed and distance are affecting the desired pattern and make an adjustment there. If the desired effect is still not achieved, then judge what needs to be changed in the first three variables and proceed through these steps again working towards the final desired effect. Once you have the effect "dialed in," make some notes on pressure, paint viscosity, flow rate, spray distance and spray speed so that you will have a starting place to replicate the same effect later. Add these notes to you color mixes, etc.
If you try to change too many variables at one time, you wind up "chasing your own tail." Proceed methodically and logically and you will be able to resolve your problems to the maximum capability of your AB and individual skills.
Often when guys get some experience, they tend to use the same air pressure and flow rates and only ever vary their paint viscosity and application distance and speeds for different effects. Alternatively, some guys keep viscosity nearly constant and play around with air pressure and flow rates to get different effects, and still others only ever vary speed and distance. This is why when guys ask questions about air pressure or paint viscosity they get as many different answers as guys answering. Why? Because each of those answers works for the guy who submitted it at what ever other variables he usually keeps constant.
This is why it's important to understand what's actually going on and to learn to trouble-shoot for your self. You, your AB, your compressor, the paints and thinners you use along with the environment you work in all form a unique, to you, system that you have to understand to get the best results from.
Sorry for the length of the reply here, but AB problems are only simple once you find the solution - the one variable that fixes the problem. Until then, it's a matter of understanding.
Happy Modeling!
Here's a rather "longish" reply, but hopefully, it's complete enough to help.
There are only a set number of variables that can be adjusted with any airbrush while using any paint. If we assume that mechanical problems have been ruled out and the paint and reducer are compatible, then these are the variables that you are working with:
1) Air pressure – controlled at the compressor and or airbrush trigger.
(If you're using a single-action AB and a diaphragm-type compressor, then air pressure is set and does not change. All other variables must be changed to accommodate this set pressure.)
2) Paint flow – controlled by the airbrush needle and tip by way of the adjusting nut or trigger and tip and needle size.
3) Paint viscosity – controlled by the operator when he reduces (i.e. thins) the paint for spraying.
4) Distance from the airbrush tip to the painted surface – controlled by the operator.
5) Speed that the airbrush is moved across the painted surface – controlled by the operator.
6) Drying time of the paint – controlled by paint viscosity, the reducer (thinner), paint volume, humidity and temperature. When the drying time is too short, all kinds of problems can result.
All of these variables can be combined in differing degrees to successfully accomplish most of the same general effects. This means that no single variable is the most important. (Even a single-action AB and diaphragm-type compressor combination allows most of these variables to be adjusted.)
For example, if the paint viscosity is too great (i.e. the paint is too "thick") and the AB will not spray, the operator can 1) increase the air pressure, or 2) he can open the tip up, or 3) he can reduce the paint, or 4) he can do some combination of all three.
However, there are some "rules of thumb" that can be turned to when sorting out problems or trying to achieve some particular effect. These rules tell us how the AB system works:
1) Fine lines are painted close to the surface.
2) Wider patterns are painted farther away from the surface.
3) The closer the tip is to the surface, the less paint flow and air pressure is needed.
4) The farther away the tip is from the surface, the more paint flow and pressure are needed.
5) Higher air pressure can spray heavier viscosity ("thicker") paint.
6) Lower air pressure can spray lighter or lower viscosity ("thinner") paint.
7) Heavier viscosity paint requires a larger tip opening.
8) Lighter viscosity paint requires a smaller tip opening.
9) Greater paint flow requires a faster surface speed and or greater distance.
10) Smaller paint flow allows a slower surface speed and or closer distance.
Using these rules of thumb, we can see that to paint fine lines: the paint viscosity is low, the air pressure low, the paint flow low, the tip is close to the surface and the speed across the surface should be moderate. Because the paint viscosity is low, it is sometimes necessary to follow the same line several times to get good coverage (a lot depends on the back ground and line colors).
Overspray is usually caused by air pressure that's too high coupled with high paint flow and too much distance from the surface. Tighter spray patterns are achieved by moving the tip closer which may require less paint volume, lower air pressure, lighter viscosity, and faster surface speed.
(Note: High pressure "tight" patterns require very fast surface speeds and close distances. The faster surface speed demands a practiced eye and a steady hand to "free hand" the desired pattern. However, the "high pressure" technique will allow for heavier viscosity paint producing better single coat coverage.)
Spattering around the edges of the paint spray pattern is usually caused by too much paint flow, too low air pressure, too low paint viscosity or a combination of all three. Reduce the paint flow, increase the air pressure and or increase the paint viscosity or, again, make a slight change in all three.
Spattering from paint build up on the AB tip is caused by 1) opening the paint flow on a double-action AB before starting the air flow, or 2) too low paint viscosity with the needle open from the tip, or 3) too low air pressure for the paint flow. Sometimes acrylic paints that are drying too fast will build up on the paint tip and create conditions for drops on the tip to also form. Adjusting the paint viscosity and using a drying retarder can sometimes help. Usually you can't do much to lower the temperature or increase the humidity, but if you can, that can also help here.
Paint runs are caused by too much paint (too high volume, too much flow, and too little distance) applied in too small an area (too slow surface speed). Gravity then pulls the paint downward creating the run. Lower the volume, decrease the flow, increase the distance or do all three to cure runs.
"Spidering" is a special case of paint runs radiating out from a single point rather than down in the direction of gravity. The cause is the same – too much paint volume on the surface at the point of the runs, in this case, by holding the AB stationary in one place, too close to the surface while starting the spraying. This loads the surface with a puddle of paint which the air pressure pushes into runs radiating from the point where the AB is directed.
The cure for "spidering" can be any one or a combination of the following: Keep the AB moving across the surface, lower the air pressure, increase the distance, and or lower the paint flow.
"Orange Peel" or "white, powdery flat coats" is caused by the atomized paint partially drying between the AB and the surface. The reason is too high air pressure, too much distance from the surface, paint drying time is too fast. The cures are: reduce air pressure and or close the distance. This combination of cures often requires speeding up the surface speed since the volume of paint onto the surface is increased. Usually, the paint-reducer (i.e. the "thinner" used) combination cannot be changed. However, the reducing ratio can sometimes be changed to increase the viscosity causing the paint to dry slightly slower (air pressure might have to be increased as a result of the higher viscosity).
When trouble shooting AB problems, the key is to understand how the system works and how changing any one variable will effect the rest. Usually, changing only one of the first three variables will produce some positive results, but possibly not achieve the desired effect. Although you can make slight changes in several variables that will combine to fix a problem, often you will not get the final effect that you want going that route and sometimes you will create a new and different problem.
So, for example, if the AB will not spray (and mechanical issues have been ruled out) then either: Reduce the paint more to make it "thinner," OR increase the air pressure, OR open up the tip more. At the same surface distance and speed (on a test piece) you should get some acceptable result. If you don't get enough improvement to get some positive result, stick with the same change just more of it until you do.
(If you max out the possible change in that variable with no positive improvement at all, you've likely misidentified the kind of problem. Best to go back to square one and start all over.)
Once the AB is spraying, then you can then judge the effects and adjust either or both of the other two variables (pressure or flow) to get an improvement towards the desired effect. Then judge how speed and distance are affecting the desired pattern and make an adjustment there. If the desired effect is still not achieved, then judge what needs to be changed in the first three variables and proceed through these steps again working towards the final desired effect. Once you have the effect "dialed in," make some notes on pressure, paint viscosity, flow rate, spray distance and spray speed so that you will have a starting place to replicate the same effect later. Add these notes to you color mixes, etc.
If you try to change too many variables at one time, you wind up "chasing your own tail." Proceed methodically and logically and you will be able to resolve your problems to the maximum capability of your AB and individual skills.
Often when guys get some experience, they tend to use the same air pressure and flow rates and only ever vary their paint viscosity and application distance and speeds for different effects. Alternatively, some guys keep viscosity nearly constant and play around with air pressure and flow rates to get different effects, and still others only ever vary speed and distance. This is why when guys ask questions about air pressure or paint viscosity they get as many different answers as guys answering. Why? Because each of those answers works for the guy who submitted it at what ever other variables he usually keeps constant.
This is why it's important to understand what's actually going on and to learn to trouble-shoot for your self. You, your AB, your compressor, the paints and thinners you use along with the environment you work in all form a unique, to you, system that you have to understand to get the best results from.
Sorry for the length of the reply here, but AB problems are only simple once you find the solution - the one variable that fixes the problem. Until then, it's a matter of understanding.
Happy Modeling!

JimF

Joined: July 05, 2002
KitMaker: 717 posts
Armorama: 621 posts
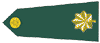
Posted: Monday, June 17, 2013 - 01:22 PM UTC
Mike, that is one of the explanations/how-tos about air brushing I have ever come across, and I've looked at lots. Even though I thought I knew most of the individual facts, seeing them all in one place, laid out logically and succinctly, is the best refresher course I could of hoped for. Thank you, thank you, thank you for your post. Throw in a few illustrations, and you have the makings of a damn article/tutorials.

![]() |