I've been working on a conversion kit that's had me doing a lot of PE soldering. I'm getting the hang of things pretty well, but have one recurring problem:
When I "tin" a part by putting solder onto the part first, then touching the part+solder to the main assembly I'm trying to attach this smaller part to, it won't stick.
I've make sure these main assembly is clean, has flux, and is getting hot enough to melt the tinned solder.... but it just won't stick.
Any ideas what I'm doing wrong?
Thanks!
Armor/AFV
For discussions on tanks, artillery, jeeps, etc.
For discussions on tanks, artillery, jeeps, etc.
Hosted by Darren Baker, Mario Matijasic
Soldering troubles
Posted: Monday, August 08, 2016 - 08:06 PM UTC
Posted: Monday, August 08, 2016 - 09:16 PM UTC
someone told me to make sure to scuff the parts up a bit with very fine grit sandpaper.... might help..... and are you putting enough solder on the original part in the tinning process to have enough to melt the gap between the two parts? Only thing I could come up with.

Belt_Fed

Joined: February 02, 2008
KitMaker: 1,388 posts
Armorama: 1,325 posts

Posted: Monday, August 08, 2016 - 10:06 PM UTC
I have run into this problem before, and simoly use other methods of soldering parts instead. perhaps you should try adding more solder to the tinned part? arr you tinning both the part and where you want the part to go? are you fluxing both the part and where you want it to go?

PRH001

Joined: June 16, 2014
KitMaker: 681 posts
Armorama: 603 posts
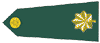
Posted: Monday, August 08, 2016 - 10:13 PM UTC
Did you tin both sides of the joint? If not the solder will try to adhere to the area where solder is already attached. Also, clean both sides of the joint and apply flux to be sure the metal is cleaned while the heat is applied. The solder will flow towards the heat easier than it will away, so place your iron where it touches both sides and pulls the solder to it. A good process is to place a small piece of fresh solder on the opposite side of the joint from the iron to pull the solder into the joint.
Hope this help,
Paul H
Hope this help,
Paul H

Kevlar06


Joined: March 15, 2009
KitMaker: 3,670 posts
Armorama: 2,052 posts

Posted: Tuesday, August 09, 2016 - 01:40 AM UTC
Rules for soldering brass--
1) clean both joining surfaces
2) use just enough solder to tin both surfaces-- less is better
3) add flux to both surfaces-
--if using a silver solder with an acid flux, make sure it's just moist, not damp
4) finally, and perhaps most importantly, make sure your soldering iron tip is clean-- you can use a damp sponge when hot, a clean nail file or metal file when cold. I never use sandpaper or paper/flexible modeling files as they sometimes shed microscopic material onto the tip which then tends to burn on, leaving unwanted carbon on the tip. When done cleaning the tip, wipe it with a damp sponge.
Lastly, as someone above said-- solder will flow towards the heat. Hope this helps.
VR Russ
1) clean both joining surfaces
2) use just enough solder to tin both surfaces-- less is better
3) add flux to both surfaces-
--if using a silver solder with an acid flux, make sure it's just moist, not damp
4) finally, and perhaps most importantly, make sure your soldering iron tip is clean-- you can use a damp sponge when hot, a clean nail file or metal file when cold. I never use sandpaper or paper/flexible modeling files as they sometimes shed microscopic material onto the tip which then tends to burn on, leaving unwanted carbon on the tip. When done cleaning the tip, wipe it with a damp sponge.
Lastly, as someone above said-- solder will flow towards the heat. Hope this helps.
VR Russ

Vicious

Joined: September 04, 2015
KitMaker: 1,517 posts
Armorama: 1,109 posts

Posted: Tuesday, August 09, 2016 - 05:11 AM UTC
i used few time a soldering paste instead of the classic solder and it work soo good and easy to work with
http://www.hobbytools.com.au/solder-paste-smd-syringe-15g/
http://www.hobbytools.com.au/solder-paste-smd-syringe-15g/

Scarred

Joined: March 11, 2016
KitMaker: 1,792 posts
Armorama: 1,186 posts

Posted: Tuesday, August 09, 2016 - 09:36 AM UTC
Is your iron hot enough? Lack of heat is a major issue when joining two parts together.

Pave-Hawk

Joined: May 05, 2006
KitMaker: 900 posts
Armorama: 510 posts

Posted: Tuesday, August 09, 2016 - 02:06 PM UTC
I second the use of solder paste. Combined with a paste flux, it's an invaluable addition to the soldering arsenal.

Kevlar06


Joined: March 15, 2009
KitMaker: 3,670 posts
Armorama: 2,052 posts

Posted: Wednesday, August 10, 2016 - 01:51 AM UTC
Quoted Text
I second the use of solder paste. Combined with a paste flux, it's an invaluable addition to the soldering arsenal.
I've been soldering for years, both with a conventional soldering iron, and an American Beauty resistance soldering unit, but I've never been able to get soldering paste to work right--either it contains too much pulverized solder or too much paste flux causing the solder to bounce away from the work. I'd like to know how you fellows get it to work. I find silver solder with acid based flux works the best with a resistance soldering unit.
VR, Russ

PRH001

Joined: June 16, 2014
KitMaker: 681 posts
Armorama: 603 posts
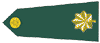
Posted: Wednesday, August 10, 2016 - 02:39 AM UTC
Solder paste is absolutely great when it is fresh, but as it ages it has a tendency to lose the ability to coalesce. That means it breaks up into fine little balls and doesn't flow very well when heated. Shelf life for solder paste to perform as intended is a relatively short time 6 months to 1 year for most brands. That assumes it is refrigerated properly. After that performance from a solder flow perspective becomes much more spotty. It will still melt and hold but it may not go where you intended and it may splatter all over the place leaving little solder splatters to clean up. I solder a good bit, and I can't get through a syringe of solder paste in a year, so I throw a lot of it away, not because it's dried out, but because it doesn't work properly any more. I only use it when the project really benefits from it as $15.00 per tube is pretty expensive when you factor that short shelf life and performance drop. Again, when it's fresh it can be awesome, when it's not, your project may get much longer cleaning up the mess.
Cheers,
Paul H
Cheers,
Paul H

Pave-Hawk

Joined: May 05, 2006
KitMaker: 900 posts
Armorama: 510 posts

Posted: Wednesday, August 10, 2016 - 07:52 AM UTC
Quoted Text
I've been soldering for years, both with a conventional soldering iron, and an American Beauty resistance soldering unit, but I've never been able to get soldering paste to work right--either it contains too much pulverized solder or too much paste flux causing the solder to bounce away from the work.
The solder paste I have contains no flux, so I use a seperate paste flux that I can put on as much or as little as I need. I can't currently justify what it would cost me to get a decent resistance soldering set up, so paste flux is my only real alternative at the moment. Forgot the flux once and got a similar efect from the solder that you describe,
I have been looking in to building a capacitive discharge welder, to see if I can do away with soldering altogether, at least for modelling.
Quoted Text
Solder paste is absolutely great when it is fresh, but as it ages it has a tendency to lose the ability to coalesce. That means it breaks up into fine little balls and doesn't flow very well when heated. Shelf life for solder paste to perform as intended is a relatively short time 6 months to 1 year for most brands. That assumes it is refrigerated properly.
I have some silver solder paste (Sn/Pb paste being unavailable) that I got from the local electronics store over 18 months ago, that still worked just fine on a recent model. I do keep it refrigerated just shy of freezing which may have helped it's shelf life. I do agree on the cost/benefit issues of it, and I bought it purely because I had some parts that were just too small and fiddly to deal with using solid solder, as even the finest solder I had still dumped way too much on the part.
Obvious issue with using silver solder paste is the lack of compatibility with the lead solder wire that I normally use.

Kevlar06


Joined: March 15, 2009
KitMaker: 3,670 posts
Armorama: 2,052 posts

Posted: Wednesday, August 10, 2016 - 09:43 AM UTC
Quoted Text
Quoted TextI've been soldering for years, both with a conventional soldering iron, and an American Beauty resistance soldering unit, but I've never been able to get soldering paste to work right--either it contains too much pulverized solder or too much paste flux causing the solder to bounce away from the work.
The solder paste I have contains no flux, so I use a seperate paste flux that I can put on as much or as little as I need. I can't currently justify what it would cost me to get a decent resistance soldering set up, so paste flux is my only real alternative at the moment. Forgot the flux once and got a similar efect from the solder that you describe,
I have been looking in to building a capacitive discharge welder, to see if I can do away with soldering altogether, at least for modelling.Quoted TextSolder paste is absolutely great when it is fresh, but as it ages it has a tendency to lose the ability to coalesce.
I have some silver solder paste (Sn/Pb paste being unavailable) that I got from the local electronics store over 18 months ago, that still worked just fine on a recent model. I do keep it refrigerated just shy of freezing which may have helped it's shelf life. I do agree on the cost/benefit issues of it, and I bought it purely because I had some parts that were just too small and fiddly to deal with using solid solder, as even the finest solder I had still dumped way too much on the part.
Obvious issue with using silver solder paste is the lack of compatibility with the lead solder wire that I normally use.
Well, I'd never heard of refrigerating the solder paste I've purchased, but it seems a mute point as I've purchased it from both Model Expo and Micro Mark, in the injector tube pictured above, and used it as soon as it arrived-- with the same results-- it tends to ball up and splatter-- maybe the distributors aren't refrigerating it. As for silver and lead solder-- I cut it into very fine pieces, smaller than the head of a pin--specks really, to apply it, and I stick it to the surface using either past flux or acid flux-- I find less is better when working with brass or photo etch. However, I can attest that a resistance soldering unit is the best way to solder (I do use a torch for large projects though). There is no substitute though for proper heat at the right place. My latest soldering project is the full waist gun position of a B-17 in 1/16 scale-- for the Verlinden waist gunner. The aircraft ribs, sheet metal skin, gun supports and sliding window are all soldered brass. I had to bend the ribs and skin over a 5lb coffee can! But to get that much heat over that large a surface required a torch for warming the brass before using the soldering unit.
VR Russ

flippen_waffles

Joined: June 01, 2010
KitMaker: 143 posts
Armorama: 116 posts

Posted: Wednesday, August 10, 2016 - 11:37 AM UTC

Kevlar06


Joined: March 15, 2009
KitMaker: 3,670 posts
Armorama: 2,052 posts

Posted: Thursday, August 11, 2016 - 06:22 AM UTC
Its an excellent article, and he's right, model railroaders have been using soldering techniques like this for years-- that's how I learned to solder. Unfortunately, he uses soldering paste in the last bit of the article but doesn't address any problems others have mentioned above with it splattering, nor list the brand he uses. I checked my tubes, and didn't find any "keep refrigerated" instructions on them, perhaps it was on the bubble packages they came in? I'm wondering if I should drop the $15 and buy one last tube to give it a shot.
VR, Russ

Pave-Hawk

Joined: May 05, 2006
KitMaker: 900 posts
Armorama: 510 posts

Posted: Thursday, August 11, 2016 - 06:53 AM UTC
Had a look at the various solder pastes available to me locally, and it looks like the lead-free silver solder paste I have has no warnings about needing to be refrigerated that I can find, whereas the tin/lead stuff does state it needs refrigerating to maintain its shelf life.
I don't know if that means that silver solder paste does not require refrigerating, or that the manufacturer simply left off the warning.
I don't know if that means that silver solder paste does not require refrigerating, or that the manufacturer simply left off the warning.

PRH001

Joined: June 16, 2014
KitMaker: 681 posts
Armorama: 603 posts
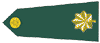
Posted: Thursday, August 11, 2016 - 07:41 AM UTC
I wrote the soldering article that Jon linked above and the solder paste used was made by GC Electronics for those who are interested.
As to the refrigeration or solder paste, theminiature and microminiature soldering training I had while on active duty in the Air Force stressed the requirement. The electronics industry commonly refrigerates solder paste to slow the degradation of the product's performance. Solder paste is actually expected to be removed from refrigeration 12-18 hrs before use to return it to room temperature.
My perspective is far from the only one when it come to soldering and It's kind of hard to anticipate all of the questions that might come up when you write an article, but if there are any that come to mind, feel free to ask or PM me if you would prefer.
As to the refrigeration or solder paste, theminiature and microminiature soldering training I had while on active duty in the Air Force stressed the requirement. The electronics industry commonly refrigerates solder paste to slow the degradation of the product's performance. Solder paste is actually expected to be removed from refrigeration 12-18 hrs before use to return it to room temperature.
My perspective is far from the only one when it come to soldering and It's kind of hard to anticipate all of the questions that might come up when you write an article, but if there are any that come to mind, feel free to ask or PM me if you would prefer.
Posted: Thursday, August 11, 2016 - 08:34 AM UTC
Great conversation, thanks!!
I've had the same problems with solder paste, but it's old and non-refrigerated. So I've order a new tube and will make sure it stays cool..... Although shipping in the Texas 100+ degree heat may kill that tube anyway.
I've had the same problems with solder paste, but it's old and non-refrigerated. So I've order a new tube and will make sure it stays cool..... Although shipping in the Texas 100+ degree heat may kill that tube anyway.
![]() |