Is there anyone out there who has built these tracks and doesn't wear a straitjacket now? So they're great looking and real sturdy and all, but 17 cuts to get the eight parts per link from their sprues, plus cutting the brass wire track pin - I mean, this is a punishment! Or can somebody give me any hints how to make assembly (especially the pressv fit of the respective second end connector) a little easier?
Help!
Peter
Hosted by Darren Baker
Kaizen T80 indy tracks

PzAufkl

Joined: October 24, 2009
KitMaker: 104 posts
Armorama: 103 posts

Posted: Sunday, August 25, 2019 - 01:33 AM UTC

TopSmith

Joined: August 09, 2002
KitMaker: 1,742 posts
Armorama: 1,658 posts

Posted: Sunday, August 25, 2019 - 04:44 AM UTC
Prozak


jps

Joined: February 06, 2006
KitMaker: 147 posts
Armorama: 140 posts

Posted: Sunday, August 25, 2019 - 05:47 AM UTC
I got some of those and said that there was no ducking way I would build these unless I got a flock of ducks to build them. I would switch to wheeled armored cars first. In the end I used The kit rubber band tracks.
I won the RFM Easy Eight at my club meeting Friday night, and I strated shaking looking at the tracks but I one of the guys said they went together well on his kit.
Don't get me wrong, I love Kaizen for German WWII buttttttt
I won the RFM Easy Eight at my club meeting Friday night, and I strated shaking looking at the tracks but I one of the guys said they went together well on his kit.
Don't get me wrong, I love Kaizen for German WWII buttttttt


RLlockie

Joined: September 06, 2013
KitMaker: 1,112 posts
Armorama: 938 posts
Posted: Sunday, August 25, 2019 - 05:49 AM UTC
My only suggestion is to get the Trumpeter working set. Pretty cheap and go together well. If you build your T-80s on level ground with side skirts and use some of the lengths from the original kit, you can stretch the working set over a couple of builds too.

27-1025

Joined: September 16, 2004
KitMaker: 1,281 posts
Armorama: 1,222 posts
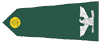
Posted: Sunday, August 25, 2019 - 06:12 AM UTC
Sorry can’t help you. I have a set stuffed away in a drawer someplace. Took one look, and after seeing how much measuring, cutting and filing was needed I put them away. If they had provided the pins precut I might have given this set a try.
Posted: Sunday, August 25, 2019 - 06:54 AM UTC
@David, those RFM tracks are over 1000 pieces! So far I've built one section of seven links...
@Peter, could you use over-long lengths of wire, thread everything on, add glue to where the wire exits the end connectors, and then just cut the excess off each side once the whole track is built? Might be a lot less effort than trying to get the pins the right length to start...

@Peter, could you use over-long lengths of wire, thread everything on, add glue to where the wire exits the end connectors, and then just cut the excess off each side once the whole track is built? Might be a lot less effort than trying to get the pins the right length to start...

PzAufkl

Joined: October 24, 2009
KitMaker: 104 posts
Armorama: 103 posts

Posted: Sunday, August 25, 2019 - 07:46 AM UTC
Tom,
That's a real good idea - in theory. The connectors have a sort of ridge on the side that touches the ground, and that protrudes beyond the track pin ends, thus requiring a cutter that would be able to cut the wire with its very tips, and I still have to see such an instrument.
For the same reason, I find it impossible to file the pin ends once they're mounted, as the instructions recommend; filing them before installation, as I do, on the other hand noticeably reduces the durability of the pins' press-fit in the connectors.
Sigh ...
That's a real good idea - in theory. The connectors have a sort of ridge on the side that touches the ground, and that protrudes beyond the track pin ends, thus requiring a cutter that would be able to cut the wire with its very tips, and I still have to see such an instrument.
For the same reason, I find it impossible to file the pin ends once they're mounted, as the instructions recommend; filing them before installation, as I do, on the other hand noticeably reduces the durability of the pins' press-fit in the connectors.
Sigh ...

RobinNilsson


Joined: November 29, 2006
KitMaker: 6,693 posts
Armorama: 5,562 posts

Posted: Sunday, August 25, 2019 - 09:51 AM UTC
Peter,
Maybe you could try another method of cutting the wire.
Using a side cutter usually results in a wedge shaped cut which requires filing.
If you place the brass rod on a hard surface, steel or glass, and then use a sharp knife blade (hobby knife, not a scalpel blade since they break when abused like this).
Measure the length of the rod, press the knife edge down on the rod at the correct length. Blade at 90 degrees angle to the hard surface and crossing the rod at 90 degrees angle.
Push the knife forward and back, rolling the brass rod over the surface. This will cut into the brass from all sides until it snaps off. Don't use too much downwards force, just enough to slowly press the hardened steel knife into the brass. If you press too hard you might cut straight through the brass rod and get an angled edge.
The wanted result is a cut that looks like a dome or very shallow cone
The same technique is used in pipe cutters:
except that the knife is a wheel that gets rolled around the pipe while being pushed inwards.
A few gentle strokes with a file should result in a good finish to the end of the rod. The knife cut could result in a very slight ridge around the rod. Fine grit "sandpaper" could cure this. A roughed up surface also works better with superglue if it should be needed to keep the tracks together.
As the next step I would try to assemble two rods and one end connector and make sure they look good. Those would be used on the outside of the track where they are most visible.
The rods could be pushed in from the outside (if there is a slight edge caused by the rolling cut). The end connector on the inside could be glued to the rods since these will be nearly invisible. The ones around the sprockets need to look good on both sides.
/ Robin
Maybe you could try another method of cutting the wire.
Using a side cutter usually results in a wedge shaped cut which requires filing.
If you place the brass rod on a hard surface, steel or glass, and then use a sharp knife blade (hobby knife, not a scalpel blade since they break when abused like this).
Measure the length of the rod, press the knife edge down on the rod at the correct length. Blade at 90 degrees angle to the hard surface and crossing the rod at 90 degrees angle.
Push the knife forward and back, rolling the brass rod over the surface. This will cut into the brass from all sides until it snaps off. Don't use too much downwards force, just enough to slowly press the hardened steel knife into the brass. If you press too hard you might cut straight through the brass rod and get an angled edge.
The wanted result is a cut that looks like a dome or very shallow cone
The same technique is used in pipe cutters:

except that the knife is a wheel that gets rolled around the pipe while being pushed inwards.
A few gentle strokes with a file should result in a good finish to the end of the rod. The knife cut could result in a very slight ridge around the rod. Fine grit "sandpaper" could cure this. A roughed up surface also works better with superglue if it should be needed to keep the tracks together.
As the next step I would try to assemble two rods and one end connector and make sure they look good. Those would be used on the outside of the track where they are most visible.
The rods could be pushed in from the outside (if there is a slight edge caused by the rolling cut). The end connector on the inside could be glued to the rods since these will be nearly invisible. The ones around the sprockets need to look good on both sides.
/ Robin

jps

Joined: February 06, 2006
KitMaker: 147 posts
Armorama: 140 posts

Posted: Sunday, August 25, 2019 - 11:00 AM UTC
I can put up with a thousand parts to do the tracks but I can't put up with them if they are a PITA


PzAufkl

Joined: October 24, 2009
KitMaker: 104 posts
Armorama: 103 posts

Posted: Sunday, August 25, 2019 - 08:14 PM UTC
Robin,
Thanks for your advice, I'll try and make some test cuts with your suggested method.
As for assembly, the main trouble is that the pin diameter is intended for a press fit: you have to insert them with pliers, there's no other way to get them in. And that results in pushing them out through the first connector when you try to mount the opposite one. Because of the "ridge" on the connectors, you can't place anything stabilizing immediately against the pin ends while pressing either.
Meanwhile, I've resorted to my brass calipers to press from both sides simultaneously, but that takes extreme care to avoid obliterating the ridges in this operation.
At least I now fully understand why it says on the box: "Just be patient"...
Thanks for your advice, I'll try and make some test cuts with your suggested method.
As for assembly, the main trouble is that the pin diameter is intended for a press fit: you have to insert them with pliers, there's no other way to get them in. And that results in pushing them out through the first connector when you try to mount the opposite one. Because of the "ridge" on the connectors, you can't place anything stabilizing immediately against the pin ends while pressing either.
Meanwhile, I've resorted to my brass calipers to press from both sides simultaneously, but that takes extreme care to avoid obliterating the ridges in this operation.
At least I now fully understand why it says on the box: "Just be patient"...

RobinNilsson


Joined: November 29, 2006
KitMaker: 6,693 posts
Armorama: 5,562 posts

Posted: Sunday, August 25, 2019 - 08:57 PM UTC
If I were in your situation I would forget about the press fit and use glue instead.
Using glue also means work but maybe it is less trouble than fighting the press fit and maybe destroying parts.
Use fine "sandpaper" to get a rough surface on the brass rod and reduce the diameter slightly.
Drilling out the holes in the connectors could be another option if you have a suitable drill ...
/ Robin
Using glue also means work but maybe it is less trouble than fighting the press fit and maybe destroying parts.
Use fine "sandpaper" to get a rough surface on the brass rod and reduce the diameter slightly.
Drilling out the holes in the connectors could be another option if you have a suitable drill ...
/ Robin

PzAufkl

Joined: October 24, 2009
KitMaker: 104 posts
Armorama: 103 posts

Posted: Tuesday, August 27, 2019 - 09:50 AM UTC
Quoted Text
If I were in your situation I would forget about the press fit and use glue instead.
Using glue also means work but maybe it is less trouble than fighting the press fit and maybe destroying parts.
Use fine "sandpaper" to get a rough surface on the brass rod and reduce the diameter slightly.
Drilling out the holes in the connectors could be another option if you have a suitable drill ...
/ Robin
You mean I should drill 344 holes (86 links per side, each connector w/ 2 holes)? No way!
I'm press fitting 'em all, which means they'll be loose eventually, and then follow your suggestion to glue it all once they're on the model - I'll keep everyone informed in due time.
Peter
![]() |