.jpg-width=1920-height=1080-fit=bounds)
For this blog I have chosen Panda’s large scale kit #16001 and intend to build it as an Ausf. G. This kit was released in 2013 and I believe is still in production? This will be my first Panda kit and first large scale build. Out of the box the kit can be built as an Ausf. E or F but with little effort it can be built as an Ausf. G. I won’t give a synopsis on the history of this tank here as there is plenty of information on the internet for that. But I will say that it was quite modern for its day and well-armed and armored against its adversary’s in the very early war years. It was fast, dependable and very reliable with good room for a crew of four despite its small size. This light tank served in almost all the theaters of war during WWII that the Germans were involved in with the exception of the African theater of operations. It became obsolete as a front line tank by late 1941 early 1942 but served in various capacities and variants until the end of the war.
.jpg-width=1920-height=1080-fit=bounds)
I tend not to follow the instructions but I do examine them thoroughly so as not to leave out any needed parts and to plan ahead as I build. I always build from the inside out and leave off external parts that could easily be knocked off when handling the model. The posted instructions are showing only the parts with some corrections that were used to get the main parts of the superstructure and hull together. I have chosen to use the hull rear panel for building of the Ausf. E because it is clean of extra holes and a molded on frame section for the smoke canister box; I will be using the Aber #16 048 basic photo etch vol. 1 set for this kit and that set contains parts to render the smoke canister box. I will show the Aber photo etch sets and aftermarket items as I use them during the build. I will not show any of the kit parts sprues here as Jim Starkweather, here on Armorama, has done a wonderful job of that in his out of the box video review for anyone interested in seeing the kit reviewed including an excellent separate clickable photo shoot of the individual kit contents here.
.jpg-width=1920-height=1080-fit=bounds)
My example came molded in a dark gray plastic. With the exception of the belly plates section, which came somewhat warped, the rest of the parts appear to be in good condition. The belly plates section was submerged in 180° of water and a heat gun was also used to relax and soften the plastic, that helped quite a bit but the warpage was slightly still there. I think that is because of its thickness?
.jpg-width=1920-height=1080-fit=bounds)
Checking through my references, notably the scale drawings in Track Link No. 18, I found that the only thing missing on the bottom side of the belly plate was a rivet. I used a round head rivet from one of Meng’s Nuts and Bolts sets. At the time, as an option, I didn’t think to go ahead and just chisel off one of the rivets from the topside of the belly plate. I placed the rivet where shown on the scale drawings forming a rectangle with the other three existing rivets. The rectangular outline surrounding the maintenance access hatch and associated bolts/rivets is unique to the Ausf. G and was not back fitted to any of the early models. Adding this hatch to earlier models of the tank is a common theme with most of the model kits on the market. If modeling either the Ausf. E or F, depending on your motivation and for accuracy, this feature would need to be removed. Nice not having to render this needed feature on the kit if you’re modeling the Ausf. G.

Here I have removed frame sections on the topside of the belly plates to directly install “I” beams to help in eliminating the warpage.
.jpg-width=1920-height=1080-fit=bounds)
One of two “I” beams have been installed in place as shown then cemented using Testors liquid cement and secured with clamps. This was allowed to cure overnight. This process was repeated for the second “I” beam. Note to self: Get more clamps!
.jpg-width=1920-height=1080-fit=bounds)
The three location holes, for the kit fenders, on the outside of each superstructure side were filled in with scrap sheet styrene. I will be using the Aber #16 049 photo etched Fenders vol. 2 set. Where indicated by the arrow I lightly scratched a small line into the plastic at either end just above where I filled in the holes as a guide to help me located where the fenders are going to fit.
.jpg-width=1920-height=1080-fit=bounds)
Here I cut down a pair of turned brass bolts where indicated on the inset picture from Aber’s #16 108 Single Wing Nut and Bolt set to depict the grease fittings on the idler shaft support housings. The fittings were then placed through a hole I had drilled through the center of a set of nuts from one of Meng’s Nuts and Bolts sets. The idler shaft support housings were drilled just enough, where indicated, to hold the nuts just even with the surface of the housings. Each of the grease fittings face toward the rear of the tank. To my surprise I was able to find a line drawing on the internet of where the grease fittings are placed throughout on this tank.
.jpg-width=1920-height=1080-fit=bounds)
Both grease fittings are in place per the line drawing. I found that the idler shafts did not fit all of the way against the idler support housings leaving a small gap so I had to open up the holes just enough to allow for this and to allow the idler shafts to rotate freely for adjusting the position of the idlers when fitting the tracks and wheels to set the track sag. This is important as I will be using a set of metal tracks on this build. The housings were lightly textured by stippling on Mr. Surfacer 500 with an old No. 2 paint brush to represent the casting feature of these parts.
.jpg-width=1920-height=1080-fit=bounds)
Here I placed a pair of bolts with nuts and bolt heads, from the Armory range of hardware, on the idler support housing and scribed in the separation to the housing adjustment block. This was repeated on both housings.

Because this may be of use to some of you I’m showing you here how I remedy warped parts and keep everything squared on the hull. Fortunately this model does not include a full interior and could be addressed in the way I approached this issue on my example. Of course there are other ways too but this is the way I have been doing this and it seems to work for me. I start by creating gussets to help in keepjing things square.

All of the pieces to create the chassis are taped together first. This helps in keeping all of the mating surfaces together when test fitting and to remedy any alinement and fit issues before cementing the parts together.

The gussets are cemented in place only onto the belly plates and allowed to cure overnight. Here I have placed the four gussets on the belly plates using the frames to keep them perpendicular to the superstructure sides. I’ve also drilled a series of holes onto the front hull section of the belly plates, more about this latter.
.jpg-width=1920-height=1080-fit=bounds)
The superstructure sides were then cemented to the gussets. I used tape to keep the top and bottom ends of the superstructure sides against the gussets and the belly plate during the cementing and curing.

The riveted plates that are intergraded with the towing hooks (not attached yet) on the rear plate and the plates fastened with screws on the bottom of the belly are actually a one piece affair. I used super glue as filler thus the transparency in the picture, when painted this will not show any separation. However, the separation line between the hull rear plate and belly is correct as these are separate pieces on the real tank.

I scribed a line between the side plate and angle plate against the rear area of the belly as these are separate parts. This was repeated for the other side.
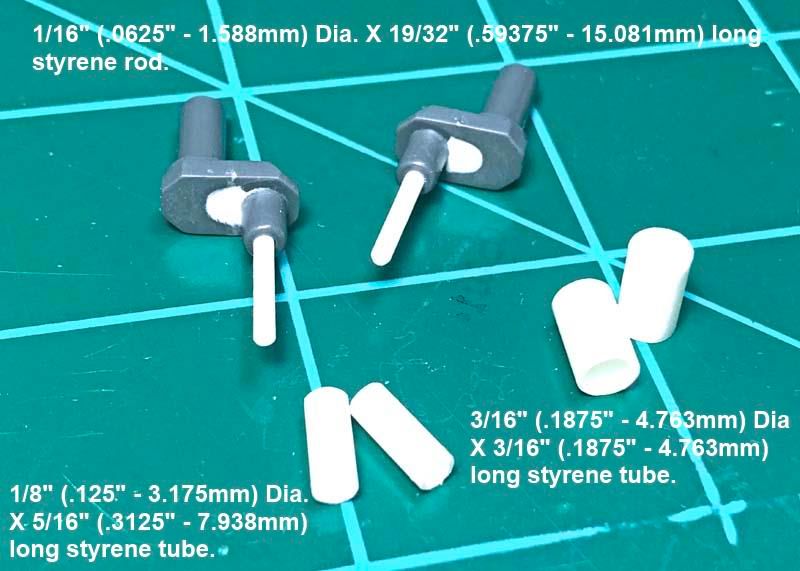
Pieces of styrene rod and tubes were cut for keeping the idler shaft in place and to allow for rotation on the model. The idler shafts were drilled to accept the styrene rods on the housing side of the idler shafts.
.jpg-width=1920-height=1080-fit=bounds)
The smaller styrene tubs were cemented centered over the styrene rods and against the idler shafts. A pair of styrene disks (2) were fabricated to secure the idler shafts against the larger styrene tubes (1) and to keep them free to rotate.

The idler shafts are fitted through the idler shaft housings to keep things aligned before cementing things in place. The larger styrene tubes (1) are then separately cemented against the inside belly plate and secured with super glue for added strength. The styrene disks (2) are then slipped over the idler shafts styrene rods and pressed against the larger styrene tubes and cemented only to the styrene rods. This will allow the shafts to freely rotate and keep them from wobbling and slipping from side to side. The idler shafts are now against the idler housings without any visible gaps.
.jpg-width=1920-height=1080-fit=bounds)
There are two pieces that make up the hull front armor in the kit and when cemented together there is a small radius along the mating edges. This groove between the two parts represents the 25mm armor base plate and the 25mm face hardened thick armor front hull plates that were riveted together and fitted to the Ausf. E and F tanks. However, on the Ausf. G a single 50mm homogeneous thick armor plate was used in place of the two plates. Super glue was used as filler between the two parts to create the single 50mm piece. On the Ausf. G two thin plates were introduced and welded against the face of this front armor plate to help support a rack assembly for holding up to 8 spare track links. This feature was also back fitted on earlier models. Fortunately there is a slight angle along the edges of the two thin plates on the kit and I used that to create a weld bead using a #15 Xacto blade. Then used Testors liquid cement to soften the scoring as this is a slower setting cement. I filled the openings on the thin plates for the track support rack assembly with styrene strip and rod; as I will be using parts from the Aber basic photo etch set.
Note: Because there were several manufactures producing this tank during the war photographs show round faced bolts or round head rivets being used for securing the single homogeneous 50mm armor plates onto the hull front, superstructure front and turret. In my research I did not find a mix of this hardware being used on any of the tanks to affix these plates. Panda has chosen to render their kit fasteners on these plates as round head rivets. I left mine that way.
.jpg-width=1920-height=1080-fit=bounds)
Here are the series of holes I drilled through the front hull section of the belly plate. I used these holes to apply liquid cement to the rear piece of the two piece front armor plate. I also used a clamp to secure the side plates against the front armor plate while the cement cured overnight.
The upper edges on the front end on the superstructure sides and backside of where the front hull armor plate resides is a rebate for placing the glacis plate. The glacis plate should sit down against this rebate so that the glacis plate face sits level and not below or proud of the front armor plate or superstructure sides. On my example the glacis plate sat proud of the superstructure sides and front armor plate. With a round edge #10 X-acto blade I carefully scrapped material off the face of the rebate until the glacis plate face sat level. Now I was ready to work over the glacis plate.
.jpg-width=1920-height=1080-fit=bounds)
The hinges for the transmission access plate have been removed on the glacis plate to accommodate the photo etch hinges in the Aber basic set. Four of the bolts have been reduced in height for attaching ring loops and a pair of holes have been filled with styrene rod for photo etch parts that will be fitted in place of the plastic parts.
.jpg-width=1920-height=1080-fit=bounds)
The glacis plate is now fastened against the sides and front armor plate with tape while the cement cures overnight. Also a clamp has been applied to keep the sides and glacis plate together. I always make it a priority to apply cement away from the appearance side of parts and this also helps to prevent the fusing of plastic between the panels where the separation of panels is appropriate.
.jpg-width=1920-height=1080-fit=bounds)
Again as on the hull rear plate and belly plate the front hull bracket pieces on the front armor plate and belly plate are a one piece affair. All of the rivets on the belly plates where removed to aid in sanding and blending of the putty. When finished with this process the rivets were than reinstalled back to their original locations.
.jpg-width=1920-height=1080-fit=bounds)
The edges on the support brackets were scribed where indicated to help define the separate parts.
.jpg-width=1920-height=1080-fit=bounds)
These are the pieces used to make the single piece homogeneous 50mm thick front superstructure armor plate. Like the two piece lower front armor plates representing 50mm of armor here again these kit parts are fashioned together in the same way. However, on the Ausf. G, the single piece 50mm armor plate is slightly wider than on the Ausf. E/F and fewer bolts/rivets were used. Seven of the twelve rivets were removed where indicated and one of the rivets was moved to a position aligned with one of the lower rivets where indicated with the dashed green lines.
.jpg-width=1920-height=1080-fit=bounds)
The machine gun ball mount was to narrow when fitted between the two plates and floated around. I fastened an electrical buss wire with super glue to the inside of the rear plate and scraped, filed and sanded the wire so that the ball mount could be easily rotated and yet fit snuggly against the front plate opening.
.jpg-width=1920-height=1080-fit=bounds)
On the Ausf. G’s there are only six bolts/rivets used on the face of the front superstructure 50mm thick armor plate as shown. Styrene strips were added to the sides as shown to widen the armor plate. This feature is unique to this model and not easily seen on WWII pictures on this tank because boxes were usually fitted on the fenders and against the sides of the front armor plate. Also the lower edge corners where cut at an angle to prevent contact with the tracks. Only a few initial production Ausf. G’s had the narrower front armor plate as on the Ausf. E/F’s. I thought the smaller hole on the flat front section of the machine gun ball mount was somewhat shallow so I deepened it up a bit.
.jpg-width=1920-height=1080-fit=bounds)
Here the front armor plate is cemented in place and secured with tape to allow the cement to cure overnight. What can’t be seen is a piece of tape on the backside holding the center of the glacis plate against the front armor plate because the glacis plate was slightly bowed and this was leaving a gap between the parts.
.jpg-width=1920-height=1080-fit=bounds)
After all I had done to square the floor plate the chassis was still slightly unleveled and one of the ends floated off the surface.
.jpg-width=1920-height=1080-fit=bounds)
I cut a slightly uneven square panel to be fitted to the inside of the chassis to force the chassis to sit flush against the surface.
.jpg-width=1920-height=1080-fit=bounds)
The panel cemented in place near the front of the engine compartment and against the frames of the superstructure sides. It worked! More building is on the way.