What is your favored method for imparting weld-beads? I like to use Milliput as it can be sculpted into a more or less convincing bead. If one studies German weld beads it is apparent, that, as model-builders we typically make our weld-beads way too tidy as WW II German welds tend to look like hell.
Cody
Hosted by Darren Baker
Welds

Stahlhelm

Joined: April 03, 2004
KitMaker: 414 posts
Armorama: 1 posts
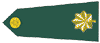
Posted: Sunday, May 23, 2004 - 02:52 PM UTC

MrRoo

Joined: October 07, 2002
KitMaker: 3,856 posts
Armorama: 2,984 posts

Posted: Sunday, May 23, 2004 - 03:44 PM UTC
I sometimes use fine copper wire.


Hollowpoint

Joined: January 24, 2002
KitMaker: 2,748 posts
Armorama: 1,797 posts

Posted: Sunday, May 23, 2004 - 05:05 PM UTC
I like to use fine styrene rod. You can stretch sprue (that's the hard way), or buy rod from Prastistruct or Evergreen. I lay it where I need a weld, glue it on, wait until dry, then soften again with cement and texture with the blade of an old Exacto. It's a bit time consuming, but it's easier than trying to direct Milliputt or some other methods -- plus it looks good and of consistent width.

jw73

Joined: April 08, 2002
KitMaker: 148 posts
Armorama: 0 posts

Posted: Sunday, May 23, 2004 - 11:33 PM UTC
In my opinion, welds on German tanks were very gentle. On Russian tanks this already were different matter.

fiftycaliber

Joined: June 10, 2004
KitMaker: 8 posts
Armorama: 0 posts
Posted: Thursday, June 17, 2004 - 05:08 PM UTC
For welds I use silicone applied with a fine needle. I guess its an added bonus of being the son of an adhesive manufacturer - I get the stuff for free :-) . Thats probably not practical in your case but its just a thought.
The welding on tanks was probably not a high priority for the germans after kursk since the demand at the front would be as great as ever.
The welding on tanks was probably not a high priority for the germans after kursk since the demand at the front would be as great as ever.

druid

Joined: December 28, 2003
KitMaker: 211 posts
Armorama: 0 posts
Posted: Thursday, June 17, 2004 - 09:43 PM UTC
I haven't tried "welding" but I thought I'd share a weathering tip I got when I was shopping for PE and pigments the last time.
The shop owner told me not to make German weld seams rusty. He said that they used some agent in welding that makes the seam shiny rather than rusty. I haven't checked on that elsewhere but I thought it was a good bit of info.
The shop owner told me not to make German weld seams rusty. He said that they used some agent in welding that makes the seam shiny rather than rusty. I haven't checked on that elsewhere but I thought it was a good bit of info.

greatbrit

Joined: May 14, 2003
KitMaker: 2,127 posts
Armorama: 1,217 posts

Posted: Thursday, June 17, 2004 - 09:47 PM UTC
i use either milliput or blu-tac.
for non brits, blu tac is the sticky putty type stuff you use for sticking paper, posters etc. it is reusable, holds any kind of paint, and is very mallable. i find it easier to work with than anything else
cheers
joe
for non brits, blu tac is the sticky putty type stuff you use for sticking paper, posters etc. it is reusable, holds any kind of paint, and is very mallable. i find it easier to work with than anything else
cheers
joe

fitzgibbon505

Joined: May 20, 2002
KitMaker: 99 posts
Armorama: 50 posts

Posted: Thursday, June 17, 2004 - 11:14 PM UTC
I use artist's acrylic paint straight from the tube. Cheap, easy, and you can replicate any type of weld. Here is a link to a little how-to I wrote. http://www.ww2modelmaker.com/articlepub/JHweldtip.htm
Jim
Jim

210cav

Joined: February 05, 2002
KitMaker: 6,149 posts
Armorama: 4,573 posts

Posted: Thursday, June 17, 2004 - 11:33 PM UTC
Fitz-- that's a great idea, I have to try that one. I have never made convincing welds and your technique will probably improve my ability.
thanks
DJ
thanks
DJ

Mech-Maniac

Joined: April 16, 2004
KitMaker: 2,240 posts
Armorama: 1,319 posts

Posted: Friday, June 18, 2004 - 02:38 AM UTC
i just use modelling cement, the stuff in the tubes, and i made a fine point for it...so i guess it all works out
Posted: Friday, June 18, 2004 - 07:23 AM UTC
Didn't Lee Loyd do an article about welding, which should be here on armorama IIRC...
Posted: Saturday, June 19, 2004 - 06:50 PM UTC
I use several methods, depending upon what type of welds I'm trying to reproduce:
1 - Fine or very well done welds
Steve Zaloga turned me on to this in one of his articles. You lay out some masking tape on each side of the weld location leaving only as much open space as the weld you are trying to reproduce. Trowel on a thin layer of spot & glaze/Squadron type putty. As thick as the tape will do nicely. While it's still fresh, peel away the tape leaving the thin parallel strip of putty. While still wet, work the weld "waves" into the putty and ley dry. Keep the putty wet with small applications of liquid cement.
2 - medium welds or fillet welds between two sizeable pieces
I use some epoxy putty, one that isn't too tacky when fresh (I like A+B Brand). I mix the putty and then roll it out into a thin, even rope or snake. I lay the snake where the weld should be and then work the surface to make the bead. If I want to make a weld that doesn't extend too far above the mating surfaces, I'll bevel the edges (just like a real butt weld) and then lay in the filler material until I'm happy with the protrusion before making the bead.
3 - Heavy welds and large casting seams
I lay out the path of the weld with a piece of fine wire that is slightly thinner than the max thickness of the weld or seam I am trying to reproduce. I'll lay a snake of epoxy putty down over the wire and then work it into a humped shape for a weld or a slightly cusped shape for a seam and then work in the bead texture. The wire ensures that I don't overdo the shaping and make it too thin as well as keeping the basic "weld" on the right path.
4 - Heavy, broad welds (multiple passes)
For the sort of multiple pass weld that joins two thick pieces of plate together, I'll lay down a ribbon of epoxy putty, shape it just right and then make multiple lines of weld bead by pushing the cylindrical end of a small rod into the fresh putty. You easily get the little "wave" shapes in the putty and if you are careful you can really see the lines of weld that a good welder will lay down. Make no mistake, even in hasty production, these lines can be easily seen.
I like to use epoxy putty because it stays workable for a long time and because it doesn't shrink and crak over time. Solvent based putties have a tendency to do that if they are over .030 thick. Be careful, though because although they are stronger than solvent putties, the epoxies don't bond to plastic terribly well and can chip off if cut after they cure. Just a case of being a little careful.
HTH
Paul
1 - Fine or very well done welds
Steve Zaloga turned me on to this in one of his articles. You lay out some masking tape on each side of the weld location leaving only as much open space as the weld you are trying to reproduce. Trowel on a thin layer of spot & glaze/Squadron type putty. As thick as the tape will do nicely. While it's still fresh, peel away the tape leaving the thin parallel strip of putty. While still wet, work the weld "waves" into the putty and ley dry. Keep the putty wet with small applications of liquid cement.
2 - medium welds or fillet welds between two sizeable pieces
I use some epoxy putty, one that isn't too tacky when fresh (I like A+B Brand). I mix the putty and then roll it out into a thin, even rope or snake. I lay the snake where the weld should be and then work the surface to make the bead. If I want to make a weld that doesn't extend too far above the mating surfaces, I'll bevel the edges (just like a real butt weld) and then lay in the filler material until I'm happy with the protrusion before making the bead.
3 - Heavy welds and large casting seams
I lay out the path of the weld with a piece of fine wire that is slightly thinner than the max thickness of the weld or seam I am trying to reproduce. I'll lay a snake of epoxy putty down over the wire and then work it into a humped shape for a weld or a slightly cusped shape for a seam and then work in the bead texture. The wire ensures that I don't overdo the shaping and make it too thin as well as keeping the basic "weld" on the right path.
4 - Heavy, broad welds (multiple passes)
For the sort of multiple pass weld that joins two thick pieces of plate together, I'll lay down a ribbon of epoxy putty, shape it just right and then make multiple lines of weld bead by pushing the cylindrical end of a small rod into the fresh putty. You easily get the little "wave" shapes in the putty and if you are careful you can really see the lines of weld that a good welder will lay down. Make no mistake, even in hasty production, these lines can be easily seen.
I like to use epoxy putty because it stays workable for a long time and because it doesn't shrink and crak over time. Solvent based putties have a tendency to do that if they are over .030 thick. Be careful, though because although they are stronger than solvent putties, the epoxies don't bond to plastic terribly well and can chip off if cut after they cure. Just a case of being a little careful.
HTH
Paul

Stahlhelm

Joined: April 03, 2004
KitMaker: 414 posts
Armorama: 1 posts
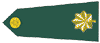
Posted: Sunday, June 20, 2004 - 07:28 AM UTC
Paul,
Interesting idea with the wire...
Two-part epoxies are terrific for welds, in particular Milliput for the 'working-time' reasons you put forth. I like to use 'shaped' toothpicks to impart faux-flows and apparent texture. This faux-weld is one example of weld samples seen on this particular feature of various Tiger 1 starter attachments. The welds on this feature range from smooth and 'dressed' to down-right scary-lookin' jagged affairs. The research continues...
Cody
Interesting idea with the wire...
Two-part epoxies are terrific for welds, in particular Milliput for the 'working-time' reasons you put forth. I like to use 'shaped' toothpicks to impart faux-flows and apparent texture. This faux-weld is one example of weld samples seen on this particular feature of various Tiger 1 starter attachments. The welds on this feature range from smooth and 'dressed' to down-right scary-lookin' jagged affairs. The research continues...
Cody

USArmy2534

Joined: January 28, 2004
KitMaker: 2,716 posts
Armorama: 1,864 posts
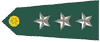
Posted: Saturday, June 26, 2004 - 01:57 PM UTC
my idea is kind of a wierd one. This only works on plastic to plactic connections, but I use Tenex plastic welder to connect my pieces (most of the time) using a touch-n-flow needle (with a small piece of rubber hose to suck in the liquid) as little is needed to create a weld. What it does is it literally melts and bonds the two plastics together so your connection is as strong as the plastic itself and not the adhesive. Anyway, when it melts and you squish those pieces together, a very small amount of melted plastic bubbles up; this is a good thing in multiple ways, not the least of which is you can sand it with virtually no seamline.
I've found you can control the "bubbling" by how hard you press and keep pressed together. The harder you press, the bigger the bubbling. After a little practice, I get a slight weld bead effect. If you are really good and the melted plastic hasn't "dried" yet you can even scribe slightly to add more texture.
I've found you can control the "bubbling" by how hard you press and keep pressed together. The harder you press, the bigger the bubbling. After a little practice, I get a slight weld bead effect. If you are really good and the melted plastic hasn't "dried" yet you can even scribe slightly to add more texture.
![]() |