Last week while on vacation I started Ravell's Tiger I E in 1/72 scale. Well late Tigers need zimm. My thoughts on it are to try to use some form of heat to burn in and melt the zimm right into the completed model. I haven't actually tried it yet, but I was thinking of two ideas 1. Pin vice a needle and heat it then use the hot needle to melt in the zimm. 2. Use the back edge of a #11 blade or a dental scribe to etch the zimm in.
How have you added zimm to braille scale kits?
Hosted by Darren Baker
Zimm in 1/72nd - How do you do it?

slodder

Joined: February 22, 2002
KitMaker: 11,718 posts
Armorama: 7,138 posts

Posted: Wednesday, June 28, 2006 - 10:32 PM UTC

Vadster

Joined: June 28, 2004
KitMaker: 987 posts
Armorama: 444 posts

Posted: Wednesday, June 28, 2006 - 10:46 PM UTC
I am just thinking out loud here. Your 2nd idea sounds better - maybe use some Tenax-7 or ProWeld to soften the plastic up 1st? I was thinking using a dime or a quarter maybe in addition to the #11 blade?



slodder

Joined: February 22, 2002
KitMaker: 11,718 posts
Armorama: 7,138 posts

Posted: Wednesday, June 28, 2006 - 10:52 PM UTC
Good call - I hadn't thought of a softener.


blaster76

Joined: September 15, 2002
KitMaker: 8,985 posts
Armorama: 3,034 posts

Posted: Wednesday, June 28, 2006 - 11:42 PM UTC
keep in mind that real zimmerit wasn't real thick. Using the burn method will probably result in it being way to deep making the zim scale out to 3 inches thick or so. Contact JIMF. He showed me a 72nd scale KT he had recently done. The zim was real delicate and you had to look hard to see it, but it was the best "in-scale" I had ever seen

slodder

Joined: February 22, 2002
KitMaker: 11,718 posts
Armorama: 7,138 posts

Posted: Thursday, June 29, 2006 - 12:26 AM UTC
Yea - scale is a big issue that's why I was going with a needle. But you're dead on with the tip. Thanks

CPL-Overby

Joined: September 12, 2005
KitMaker: 190 posts
Armorama: 192 posts

Posted: Thursday, June 29, 2006 - 06:47 AM UTC
Keep in mind that while Zimmerit isn't very thick, it does have thickness.
Burning or scribing it in taks away from that.
To be athentic you should apply putty and use a jeweller's screw driver to apply the pattern.
Burning or scribing it in taks away from that.
To be athentic you should apply putty and use a jeweller's screw driver to apply the pattern.

Sabot
Joined: December 18, 2001
KitMaker: 12,596 posts
Armorama: 9,071 posts
KitMaker: 12,596 posts
Armorama: 9,071 posts

Posted: Thursday, June 29, 2006 - 08:33 AM UTC
Quoted Text
I've used both Eduard and Part PE zimmerit. It is kind of tricky to get into place before the glue grabs. I've also bought the Atak resin zimmerit set for the Dragon Sturmtiger, Elefant and Revell King Tiger (Porsche). I have not tried them yet, but after doing PE zimmerit, they look like a much easier solution to me.How have you added zimm to braille scale kits?

RAF-Mad

Joined: March 13, 2004
KitMaker: 153 posts
Armorama: 0 posts
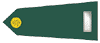
Posted: Friday, July 07, 2006 - 12:33 PM UTC
dont know if this help this was one of my 1/72 with a PART photoetch zimm kit on it

for my tiger e i have some resin parts (cant remember who the manufacturer is) with zimm for revell kit not got rooud to buying the actual revell kit yet to try it out


for my tiger e i have some resin parts (cant remember who the manufacturer is) with zimm for revell kit not got rooud to buying the actual revell kit yet to try it out


sparten

Joined: August 11, 2005
KitMaker: 28 posts
Armorama: 27 posts

Posted: Friday, September 29, 2006 - 08:34 PM UTC
Hi
I'm just adding zimm to my tiger 1, i am using humbrol putty spread on really thin and then using a very small screwdriver used for those tiny screws in peoples glasses to inprint the pattern. So far it looks pretty good to my eyes anyway.
Sparten
I'm just adding zimm to my tiger 1, i am using humbrol putty spread on really thin and then using a very small screwdriver used for those tiny screws in peoples glasses to inprint the pattern. So far it looks pretty good to my eyes anyway.
Sparten

nfafan

Joined: August 01, 2003
KitMaker: 335 posts
Armorama: 315 posts
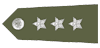
Posted: Saturday, September 30, 2006 - 05:39 AM UTC
Quoted Text
keep in mind that real zimmerit wasn't real thick. Using the burn method will probably result in it being way to deep making the zim scale out to 3 inches thick or so. Contact JIMF. He showed me a 72nd scale KT he had recently done. The zim was real delicate and you had to look hard to see it, but it was the best "in-scale" I had ever seen
Agree, especially on a 1/72nd AFV. Look closely at pix of Zimm'd armor where the distance to the vehicle makes it approx 1/72nd in size - in the pic the zimm is barely visible. Even true on many pix where the vehicle is "closer" to the camera than 1/72nd.
To that end, I used the "liquid cement to soften the surface" trick and scribed the pattern into the surface. Time consuming but way cheaper than aftermarket zimm and less work than trying to spread and scribe a thin layer of putty.

LarryStrong
Joined: January 16, 2007
KitMaker: 3 posts
Armorama: 2 posts
KitMaker: 3 posts
Armorama: 2 posts

Posted: Monday, January 15, 2007 - 06:54 PM UTC
I use the edge of paper napkin I jsut seperate the napkin from itself , then soften the model with liquid glue and then lay it on. I will post a photo later today.



JimF

Joined: July 05, 2002
KitMaker: 717 posts
Armorama: 621 posts
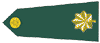
Posted: Monday, January 15, 2007 - 07:38 PM UTC
The method I used to do the zim on a 1/48 scale Tiger II was to use Mr Surfacer 500 liberally on the surfaces that needed zimmeret, and then scribe it. If I didn't like the pattern, a bit of light sanding, a tad more Mr Surfacer 500, and then a careful application of a pointy thing did the trick.


Wolf-Leader

Joined: June 06, 2002
KitMaker: 1,225 posts
Armorama: 520 posts

Posted: Monday, January 15, 2007 - 08:04 PM UTC
Quoted Text
Last week while on vacation I started Ravell's Tiger I E in 1/72 scale. Well late Tigers need zimm. My thoughts on it are to try to use some form of heat to burn in and melt the zimm right into the completed model. I haven't actually tried it yet, but I was thinking of two ideas 1. Pin vice a needle and heat it then use the hot needle to melt in the zimm. 2. Use the back edge of a #11 blade or a dental scribe to etch the zimm in.
How have you added zimm to braille scale kits?
Hi good question.
As most of you guys know, I did a very intensive scratch build project of a 1/72nd scale Panzer IV with zimmerite. What I did was I got very detailed photos of the pattern I wanted and then found the thinnest sheet of brass I could find. I then took it to an engraver that can laser engrave on brass and them to copy the detailed photo onto the brass sheet. It came out perfectly!!!

DavidOBarr

Joined: September 27, 2006
KitMaker: 26 posts
Armorama: 25 posts

Posted: Tuesday, January 23, 2007 - 12:41 AM UTC
I have used three methods for zim in 1/72. The first is the hardest but looks the best - It is a two part epoxy product called Zim-it-rite. You just mix the epoxy together, spread it on the surface and I then use a small jeweler's screwdriver to create the pattern. This is time consuming and some surfaces are small or awkward. The result looks like the real thing. The second method is using liquid cement to soften the plastic and then using the same small screwdriver to make the pattern. This is more difficult because the indentation varies in depth and the starting surface is smooth. It looks OK but not as nice as the Zim-it-rite. The third method in the PE sets. These go on easy and they take very little time. The only drawback is the pattern is too regular. Also usually there are some small surffaces left that you must cover with zim using either method one or method two. These areas will not look as fine and as neat as the PE portions. Have fun (Oh yeah a fourth method is to buy one of the several Dragon kits that come covered in very nice "Molded On" zim.)
![]() |