I'm wondering what are some good silicone and resin products out there that are good to use for casting. I'm looking at some Smooth-on products but unfortunately I can't find the major distributor near me. What are some other good silicone and resin products that are of a good quality but at a lower price?
What I like about Smooth-on is that they say that the resin is "virtually bubble free." But I assume that vibrating or degassing would still be necessary.
Armor/AFV
For discussions on tanks, artillery, jeeps, etc.
For discussions on tanks, artillery, jeeps, etc.
Hosted by Darren Baker, Mario Matijasic
Good rubber silicone/urethane resin to use?

MikeyBugs95

Joined: May 27, 2013
KitMaker: 2,210 posts
Armorama: 1,712 posts
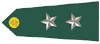
Posted: Saturday, September 10, 2016 - 08:31 PM UTC
TankCarl

Joined: May 10, 2002
KitMaker: 3,581 posts
Armorama: 2,782 posts

Posted: Saturday, September 10, 2016 - 09:21 PM UTC
I have used the Smooth on rubber and resin,to make castings for the rear of my 1/6th scale M4A3's roadwheels.In my experiance, I did not have any major bubbles.Being able to degas,and vibrate would be an added plus,for any resin

heliman

Joined: June 14, 2010
KitMaker: 702 posts
Armorama: 604 posts

Posted: Saturday, September 10, 2016 - 11:11 PM UTC
The product I use the most and is readily available in hobby lobby stores is Alumilite. Their high strenth 3 rubber is great for details and the resin is quick curing. My buddy uses Smooth On products but buys it in large quantities.
HTH
HTH

samkidd

Joined: January 06, 2006
KitMaker: 530 posts
Armorama: 450 posts
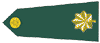
Posted: Sunday, September 11, 2016 - 06:37 AM UTC
This may come as a shock to exactly no one but I have quite a bit of experience with both Alumilite and Smooth-on products. Which one is best for what you're looking to do depends greatly on what you want to cast, how many, the casting itself and of course, availability.
You mentioned not having a Smooth-On dealer nearby. Well, that is one area in which Alumilite edges out Smooth-On. You can order directly from them and I've never had a single issue with their delivery even all the way to Alaska in winter. I still order from them as some of their resins are ideally suited to a few of my castings.
That said, I primarily use Smooth-On products now. They have a tremendous selection to choose from and you can tailor your silicone and resin choices to fit your project. For example you may want a very soft silicone rubber due to some tricky undercuts or edges on the item you are casting. Or perhaps you need something unusual like a resin with a high UV or heat resistance. In this the Smooth-On line is excellent.
If you're only wanting to cast up a few pieces of whatever and aren't in a big hurry I'd recommend leaning towards the resins (of either brand) with the longer "pot life" or curing time. In the short run for small batches Alumilite is usually cheaper for this. Using slower formulas will allow you to paint the inside of the mold with resin to ensure good coverage and more handling time to work out any air bubbles. Just remember that many resins go from easy to use liquid to almost solid plastic in mere seconds so plan accordingly.
*WARNING* If you're planning to cast up some items that have been 3D printed a really good mold release agent is essential. Not just a good idea, it is crucial. The beauty of silicone rubber is that it sticks to almost nothing. Sadly, one of the few things it will absolutely fuse itself to is most of the plastics used in 3D printing. So coat these items generously. Then coat them again. Most release agents dry off leaving only a micro thin layer barrier so don't worry about losing details.
If anyone has questions about specific products or applications for specific projects I'd be happy to help. And please, please follow all manufacturer's warning and safety guidelines. This stuff is fun but they are chemicals that aren't friendly.
Jim
LSA
You mentioned not having a Smooth-On dealer nearby. Well, that is one area in which Alumilite edges out Smooth-On. You can order directly from them and I've never had a single issue with their delivery even all the way to Alaska in winter. I still order from them as some of their resins are ideally suited to a few of my castings.
That said, I primarily use Smooth-On products now. They have a tremendous selection to choose from and you can tailor your silicone and resin choices to fit your project. For example you may want a very soft silicone rubber due to some tricky undercuts or edges on the item you are casting. Or perhaps you need something unusual like a resin with a high UV or heat resistance. In this the Smooth-On line is excellent.
If you're only wanting to cast up a few pieces of whatever and aren't in a big hurry I'd recommend leaning towards the resins (of either brand) with the longer "pot life" or curing time. In the short run for small batches Alumilite is usually cheaper for this. Using slower formulas will allow you to paint the inside of the mold with resin to ensure good coverage and more handling time to work out any air bubbles. Just remember that many resins go from easy to use liquid to almost solid plastic in mere seconds so plan accordingly.
*WARNING* If you're planning to cast up some items that have been 3D printed a really good mold release agent is essential. Not just a good idea, it is crucial. The beauty of silicone rubber is that it sticks to almost nothing. Sadly, one of the few things it will absolutely fuse itself to is most of the plastics used in 3D printing. So coat these items generously. Then coat them again. Most release agents dry off leaving only a micro thin layer barrier so don't worry about losing details.
If anyone has questions about specific products or applications for specific projects I'd be happy to help. And please, please follow all manufacturer's warning and safety guidelines. This stuff is fun but they are chemicals that aren't friendly.
Jim
LSA

DocEvan

Joined: August 09, 2014
KitMaker: 180 posts
Armorama: 180 posts
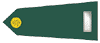
Posted: Sunday, September 11, 2016 - 07:41 AM UTC
I have great success with Micro-Mark's casting materials.
Quoted Text
I'm wondering what are some good silicone and resin products out there that are good to use for casting. I'm looking at some Smooth-on products but unfortunately I can't find the major distributor near me. What are some other good silicone and resin products that are of a good quality but at a lower price?
What I like about Smooth-on is that they say that the resin is "virtually bubble free." But I assume that vibrating or degassing would still be necessary.

MikeyBugs95

Joined: May 27, 2013
KitMaker: 2,210 posts
Armorama: 1,712 posts
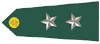
Posted: Sunday, September 11, 2016 - 08:06 AM UTC
Thanks for the reply guys. I'm trying to cast a set of 3D printed parts that I will be ordering (and yes they are of my design so no worry about infringing on anyone). I want to try to make a run of about 10-15.
James: There is a full-line Smooth-On distributor nearby but I just can't find them. I'm looking towards the products that have a pot life of around 10 minutes. I may have a vibrating table but I'm not sure so I would definitely need the time to get the resin bubble-free. Thanks for the tip about the 3D printed products. I'll need to buy some mold release now. Just out of curiosity, would non-stick cooking spray work as a mold release?
James: There is a full-line Smooth-On distributor nearby but I just can't find them. I'm looking towards the products that have a pot life of around 10 minutes. I may have a vibrating table but I'm not sure so I would definitely need the time to get the resin bubble-free. Thanks for the tip about the 3D printed products. I'll need to buy some mold release now. Just out of curiosity, would non-stick cooking spray work as a mold release?

samkidd

Joined: January 06, 2006
KitMaker: 530 posts
Armorama: 450 posts
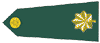
Posted: Sunday, September 11, 2016 - 12:34 PM UTC
I've never tried cooking spray so I cannot say for certain that it wouldn't work but I have my doubts. I DO know that there are various substances that can inhibit (prevents it from happening fully) the cure of silicone. Leaves it a liquidy gooie mess where it contacts the inhibitor. For that reason I'd be wary of experimenting on anything that I wasn't willing to toss completely in the trash should the resin stick to the subject or fail to cure. Pouring silicone molds and making castings are often pretty much either completely successful or are a total write off.
Also for 3D printed items like these you can get away with a spray mold release although a brush on version would be best. I've found that Mann's Ease Release 205 is excellent for this. This simply coats the surface and about 80% of it evaporates away, leaving a uniform, micro thin barrier between the casting object and the mold rubber.
Remember, as has been pointed out on various threads here on the forum, various 3D printing outfits produce items that typically have one "rough" side. This rough side is a magnet for many mold rubbers which often have a very hard time releasing from it. That's why thorough coverage of all surfaces is so important. Spray releases do a decent job in prepping a 3D piece for molding. But my experience is that an evaporating brush on release (like the 205) is best for most of these. Above all avoid things that contain water or attract moisture as this can cause cure inhibition faster than anything. This also applies to the environment around your mold making. Moisture kills mold silicone during the cure process so some areas may never cure.
Trust me, nothing is more disappointing than seeing both a long awaited 3D printed piece and the expensive mold itself turn into a hopelessly stuck and torn piece of fail. That's why I decided to comment, casting is expensive and there are some dreadfully easy mistakes to make when you're first starting out. My advice is to stick with known, recommended products before trying to experiment. Generally speaking it is too expensive (in time and money) to be throwing unknown elements into the mix before you even have your first success.
Not trying to put anyone off of casting here, quite the opposite in fact. Even today I get the biggest kick out of opening a mold to find that really cool piece that didn't even exist anywhere an hour before. But before you get to that cool part I just want folks to be aware of the hidden pitfalls that could rob you of that thrill. Read everything you can find and don't hesitate to ask questions. Questions are WAY cheaper than silicone!
Jim
LSA
Also for 3D printed items like these you can get away with a spray mold release although a brush on version would be best. I've found that Mann's Ease Release 205 is excellent for this. This simply coats the surface and about 80% of it evaporates away, leaving a uniform, micro thin barrier between the casting object and the mold rubber.
Remember, as has been pointed out on various threads here on the forum, various 3D printing outfits produce items that typically have one "rough" side. This rough side is a magnet for many mold rubbers which often have a very hard time releasing from it. That's why thorough coverage of all surfaces is so important. Spray releases do a decent job in prepping a 3D piece for molding. But my experience is that an evaporating brush on release (like the 205) is best for most of these. Above all avoid things that contain water or attract moisture as this can cause cure inhibition faster than anything. This also applies to the environment around your mold making. Moisture kills mold silicone during the cure process so some areas may never cure.
Trust me, nothing is more disappointing than seeing both a long awaited 3D printed piece and the expensive mold itself turn into a hopelessly stuck and torn piece of fail. That's why I decided to comment, casting is expensive and there are some dreadfully easy mistakes to make when you're first starting out. My advice is to stick with known, recommended products before trying to experiment. Generally speaking it is too expensive (in time and money) to be throwing unknown elements into the mix before you even have your first success.
Not trying to put anyone off of casting here, quite the opposite in fact. Even today I get the biggest kick out of opening a mold to find that really cool piece that didn't even exist anywhere an hour before. But before you get to that cool part I just want folks to be aware of the hidden pitfalls that could rob you of that thrill. Read everything you can find and don't hesitate to ask questions. Questions are WAY cheaper than silicone!
Jim
LSA

heliman

Joined: June 14, 2010
KitMaker: 702 posts
Armorama: 604 posts

Posted: Sunday, September 11, 2016 - 06:05 PM UTC
Thanks Jim for the excellent information, several parts I was unaware of and in the future take note of

matt


Joined: February 28, 2002
KitMaker: 5,957 posts
Armorama: 2,956 posts

Posted: Sunday, September 11, 2016 - 09:09 PM UTC
Mike,
I have Smooth-on shipped to me, it beats driving to the nearest dealer 4+ hours away. Shipping is pretty reasonable with the gallon size kits.
I have Smooth-on shipped to me, it beats driving to the nearest dealer 4+ hours away. Shipping is pretty reasonable with the gallon size kits.

MikeyBugs95

Joined: May 27, 2013
KitMaker: 2,210 posts
Armorama: 1,712 posts
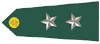
Posted: Monday, September 12, 2016 - 04:19 AM UTC
I've actually found the full-line Smooth-on dealer near me. It was well hidden and I didn't see the sign for them. I'll also head to Michael's or AC Moore to pick up a small set of Alumilite silicone and test it out on some scrap 3D printed pieces I have. Tomorrow I'll get Smooth-on silicone and test them out.
Posted: Monday, September 12, 2016 - 06:10 AM UTC
I have been using Smooth On for some time and have had great success with it I am now branching out into some of their other silicones and resins. 
Cheers Rob.

Cheers Rob.

MikeyBugs95

Joined: May 27, 2013
KitMaker: 2,210 posts
Armorama: 1,712 posts
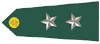
Posted: Tuesday, September 13, 2016 - 03:22 AM UTC
I just purchased some Smooth-on Mold Max 14NV and Smooth-Cast 305. I have a junk 3DP part that's half primed and half bare plastic so I'll test it out and see how the silicon reacts.

motor-t

Joined: September 04, 2005
KitMaker: 10 posts
Armorama: 10 posts
Posted: Tuesday, September 13, 2016 - 06:54 AM UTC
http://hobbysilicone.com/ I've had exellent results using their products

samkidd

Joined: January 06, 2006
KitMaker: 530 posts
Armorama: 450 posts
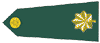
Posted: Wednesday, September 14, 2016 - 01:26 AM UTC
I've used the Smooth on 305 and it is very easy to work with. A couple observations about this particular plastic though. First off, it doesn't reach "really hard" like most of the resin model kit pieces that you might be used to.
It gets hard and is excellent to work with, but the cured plastic is much more like the "green Army Man" plastic like the common children's toy is made from. Slightly elastic and fairly easy to bend. I mention this because it should not be used for anything that will be subjected to a load or stress.
Here's an example. I once used 305 to cast some Jeep axles. My idea at the time was that the slightly softer formula might cut down on potential breakage of parts in shipping. The axles were perfect and went together well. Several weeks later however I noticed that my "test build" models all had the wheels slowly bending up into the wheel wells on the Jeep.
Turns out the softer plastic, over time, was bending under even the lightest load of an unfinished Jeep body. Further testing revealed the same results when this plastic was used to hold up part of a model's ramp. Over a short time it bent and distorted.
Many other types of items cast in this formula are excellent. Ammo crates, packs, pistols and various other pieces benefit from this resin's much less brittle nature and more forgiving properties. This is why I still use this formula for many items while most of my production has been moved over to the TASK line of resins from Smooth On. The Task resins I use are much stronger and have great casting qualities for things requiring shape retention, durability and overall strength.
Just thought I'd toss that out there.
Jim
LSA
It gets hard and is excellent to work with, but the cured plastic is much more like the "green Army Man" plastic like the common children's toy is made from. Slightly elastic and fairly easy to bend. I mention this because it should not be used for anything that will be subjected to a load or stress.
Here's an example. I once used 305 to cast some Jeep axles. My idea at the time was that the slightly softer formula might cut down on potential breakage of parts in shipping. The axles were perfect and went together well. Several weeks later however I noticed that my "test build" models all had the wheels slowly bending up into the wheel wells on the Jeep.
Turns out the softer plastic, over time, was bending under even the lightest load of an unfinished Jeep body. Further testing revealed the same results when this plastic was used to hold up part of a model's ramp. Over a short time it bent and distorted.
Many other types of items cast in this formula are excellent. Ammo crates, packs, pistols and various other pieces benefit from this resin's much less brittle nature and more forgiving properties. This is why I still use this formula for many items while most of my production has been moved over to the TASK line of resins from Smooth On. The Task resins I use are much stronger and have great casting qualities for things requiring shape retention, durability and overall strength.
Just thought I'd toss that out there.
Jim
LSA
Posted: Wednesday, September 14, 2016 - 06:50 AM UTC
I have been using smooth cast 310 with great results.
Cheers Rob.

Cheers Rob.
Posted: Wednesday, September 14, 2016 - 07:35 PM UTC
For 3D printed parts, you can also paint or dip them in Future to add a thin barrier and also fill some of the small print lines (though you really do need to sand those parts before casting in most cases).
Once the Future dries, use the mould release as well and all should be good.
Paul
Once the Future dries, use the mould release as well and all should be good.
Paul

MikeyBugs95

Joined: May 27, 2013
KitMaker: 2,210 posts
Armorama: 1,712 posts
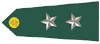
Posted: Thursday, September 15, 2016 - 02:37 AM UTC
Thanks. For some reason, the internet, TV and phone are down at my house so I've had quite a lot of time to practice molding and casting. I've been able to cast one of the holographic weapon sights from the set I made and it turned out pretty good. I'm going to cast the rest of the set using some sprues and see what happens.
What resin would anyone recommend from the Smooth-on line? For the large pieces I eventually want to cast, they will mostly be structural and need to support weight (plus their own weight) so I need a hard resin much like the resin we're used to using in this hobby.
What resin would anyone recommend from the Smooth-on line? For the large pieces I eventually want to cast, they will mostly be structural and need to support weight (plus their own weight) so I need a hard resin much like the resin we're used to using in this hobby.

samkidd

Joined: January 06, 2006
KitMaker: 530 posts
Armorama: 450 posts
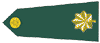
Posted: Thursday, September 15, 2016 - 04:08 AM UTC
I'd get a couple of the trial sizes of TASK 2 and TASK 8, depending on how fast a cure you would prefer.
Jim
LSA
Jim
LSA

MikeyBugs95

Joined: May 27, 2013
KitMaker: 2,210 posts
Armorama: 1,712 posts
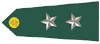
Posted: Thursday, September 15, 2016 - 06:28 AM UTC
Total cure time doesn't matter to me. Pot life/work time is what I need.

samkidd

Joined: January 06, 2006
KitMaker: 530 posts
Armorama: 450 posts
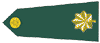
Posted: Thursday, September 15, 2016 - 03:05 PM UTC
Again, it depends a lot on what you're casting, how it's molded, what technique you're using to cast and how much time you need to make the cast itself.
If you're looking for a longer "pot life" then TASK 2 would be the better of the two. It also has a much longer cure time so you'll have to resist messing with it until it has had time to cure itself. Generally speaking, the longer the pot life, the slower the ending cure.
For those who might not know when we are talking about "pot life" we are referring to the length of time you have before the mixed liquid resin starts to "flash" and become hard plastic. With the slower curing resins that have the longer pot life this can take a little longer but is still surprisingly quick. The faster resins can go from thin liquid, to honey like thickness, to hard plastic in a matter of seconds.
If you're just using a simple one piece or two piece mold and casting a piece or two without assistance from either vacuum or pressure then I'd go with the TASK 2. It has a nice pot life of around 7 minutes and you can usually take the pieces out of the mold after an hour or so. The 7 minutes is usually enough time to swab the inside of the mold with resin to ensure good coverage. It is also long enough to pour the resin and then swab the flooded mold again to work out any air bubbles.
TASK 8 has it's uses and is excellent if you want to make something quickly. It's pot life is listed around 2.5 minutes and you can generally take the piece out of the mold around 20 minutes later. I recommended both of these resins over several others as being easy to use and achieving the "hardness" of cure that I believe most modeler's would want.
Jim
LSA
If you're looking for a longer "pot life" then TASK 2 would be the better of the two. It also has a much longer cure time so you'll have to resist messing with it until it has had time to cure itself. Generally speaking, the longer the pot life, the slower the ending cure.
For those who might not know when we are talking about "pot life" we are referring to the length of time you have before the mixed liquid resin starts to "flash" and become hard plastic. With the slower curing resins that have the longer pot life this can take a little longer but is still surprisingly quick. The faster resins can go from thin liquid, to honey like thickness, to hard plastic in a matter of seconds.
If you're just using a simple one piece or two piece mold and casting a piece or two without assistance from either vacuum or pressure then I'd go with the TASK 2. It has a nice pot life of around 7 minutes and you can usually take the pieces out of the mold after an hour or so. The 7 minutes is usually enough time to swab the inside of the mold with resin to ensure good coverage. It is also long enough to pour the resin and then swab the flooded mold again to work out any air bubbles.
TASK 8 has it's uses and is excellent if you want to make something quickly. It's pot life is listed around 2.5 minutes and you can generally take the piece out of the mold around 20 minutes later. I recommended both of these resins over several others as being easy to use and achieving the "hardness" of cure that I believe most modeler's would want.
Jim
LSA

matt


Joined: February 28, 2002
KitMaker: 5,957 posts
Armorama: 2,956 posts

Posted: Thursday, September 15, 2016 - 03:50 PM UTC
Smooth Cast 310 and Mold Max 20 are my usual go to's.

samkidd

Joined: January 06, 2006
KitMaker: 530 posts
Armorama: 450 posts
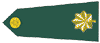
Posted: Thursday, September 15, 2016 - 11:28 PM UTC
Matt is correct. Both the 310 and Mold Max 20 are excellent all around choices as well. The Mold Max 20 Silicone rubber is a very forgiving and long lasting silicone that can survive casting pieces with deep undercuts. It is also firm enough on it's own to minimize any distortion while being soft enough to be easy to work with. Great suggestions Matt!
Jim
LSA
Jim
LSA

MikeyBugs95

Joined: May 27, 2013
KitMaker: 2,210 posts
Armorama: 1,712 posts
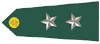
Posted: Thursday, September 15, 2016 - 11:42 PM UTC
So I will be picking up a different resin. Which would you recommend. 310 or TASK 2. With TASK 2, do I need to use a vacuum chamber? Will I still get bubbles if I don't? Also, James, what do you mean by swabbing the inside with resin?

samkidd

Joined: January 06, 2006
KitMaker: 530 posts
Armorama: 450 posts
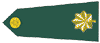
Posted: Friday, September 16, 2016 - 12:51 PM UTC
Neither of these resins requires a vacuum chamber. They are always nice to use if you have one but they are not necessary for hobbyist use. You stand the chance of having air bubbles in ANY resin as there is a thorough mixing of two chemicals involved but the chance of having air bubbles ruin your casting can be reduced.
First, when mixing, don't "whip" the two chemicals together. When mixing small amounts I typically used disposable 1oz. cups and a disposable hobby paint brush. The cups are inexpensive and available through most casting dealers while I have found the small hobby brushes in a 30 piece package at Walmart for a couple dollars. Look in the kid's crafting area.
As for "swabbing" aka "painting" the inside of the mold it is just a simple technique to cut down on air bubbles ruining the surface of your cast. I take the small brush and mix the two chemicals together thoroughly. Then using that same brush and a generous amount of the mixed resin I simply paint or swab the inside of the mold with resin to make sure it coats the entire surface.
Bubbles often form in pockets of detail or corners of a mold cavity when you pour in the resin. By painting the interior mold surface with resin you allow air bubbles and air pockets that might otherwise be trapped in the mold to move away from the mold surface more freely. Basically these bubbles like to cling to bare silicone surfaces but if the surface is already fully coated there's nothing to cling to so they tend to float away from the interior mold surfaces.
By casting without aid of either vacuum or pressure you will likely still get a few bubbles. But by painting or swabbing the inside mold surfaces with the mixed resin before you pour the resin in you are moving the bubbles away from what will be the surface of you cast piece. They then tend to migrate more towards the interior where you'll never see them or to the casting stub area.
As for 310 vs. TASK 2 take a look at both on the Smooth-On website and weight their pros and cons for what you want. Both are great. Each has wildly different casting performance. Either CAN give you great casts if you take your time and use the painting technique. I would guess that the 310 would probably work well for most beginners as it usually mixes with very few bubbles. It cures to a strong, slightly flexible plastic. If you decide to go with the 310 then make sure you can leave the casting and mold alone for about 4 or more hours to allow it to cure. Never move, handle, poke at or pry open any mold until it has COMPLETELY cured.
The TASK 2 is a little trickier to work with but yields harder casts and has a greatly reduced curing time. It is a slightly higher performance resin but also one that requires a bit more attention to avoiding the dreaded air bubbles during mixing and pouring. It can get bubbles a bit easier than the 310.
So really it is a matter of choosing whichever one you feel most comfortable about working with and what end results you want. Try hitting up the Smooth On website and take a look at all their resins. Chances are that you'll find something that is perfect for what you're wanting to accomplish. They also have loads of videos to show you how to get started casting.
Jim
LSA
First, when mixing, don't "whip" the two chemicals together. When mixing small amounts I typically used disposable 1oz. cups and a disposable hobby paint brush. The cups are inexpensive and available through most casting dealers while I have found the small hobby brushes in a 30 piece package at Walmart for a couple dollars. Look in the kid's crafting area.
As for "swabbing" aka "painting" the inside of the mold it is just a simple technique to cut down on air bubbles ruining the surface of your cast. I take the small brush and mix the two chemicals together thoroughly. Then using that same brush and a generous amount of the mixed resin I simply paint or swab the inside of the mold with resin to make sure it coats the entire surface.
Bubbles often form in pockets of detail or corners of a mold cavity when you pour in the resin. By painting the interior mold surface with resin you allow air bubbles and air pockets that might otherwise be trapped in the mold to move away from the mold surface more freely. Basically these bubbles like to cling to bare silicone surfaces but if the surface is already fully coated there's nothing to cling to so they tend to float away from the interior mold surfaces.
By casting without aid of either vacuum or pressure you will likely still get a few bubbles. But by painting or swabbing the inside mold surfaces with the mixed resin before you pour the resin in you are moving the bubbles away from what will be the surface of you cast piece. They then tend to migrate more towards the interior where you'll never see them or to the casting stub area.
As for 310 vs. TASK 2 take a look at both on the Smooth-On website and weight their pros and cons for what you want. Both are great. Each has wildly different casting performance. Either CAN give you great casts if you take your time and use the painting technique. I would guess that the 310 would probably work well for most beginners as it usually mixes with very few bubbles. It cures to a strong, slightly flexible plastic. If you decide to go with the 310 then make sure you can leave the casting and mold alone for about 4 or more hours to allow it to cure. Never move, handle, poke at or pry open any mold until it has COMPLETELY cured.
The TASK 2 is a little trickier to work with but yields harder casts and has a greatly reduced curing time. It is a slightly higher performance resin but also one that requires a bit more attention to avoiding the dreaded air bubbles during mixing and pouring. It can get bubbles a bit easier than the 310.
So really it is a matter of choosing whichever one you feel most comfortable about working with and what end results you want. Try hitting up the Smooth On website and take a look at all their resins. Chances are that you'll find something that is perfect for what you're wanting to accomplish. They also have loads of videos to show you how to get started casting.
Jim
LSA

matt


Joined: February 28, 2002
KitMaker: 5,957 posts
Armorama: 2,956 posts

Posted: Friday, September 16, 2016 - 02:30 PM UTC
I use a pressure pot (a hell of a lot cheaper than a vac. chamber) to do my casting, the result is better castings, as it makes any bubble really tiny!
![]() |