Hi Jason - thanks for showing so much of your build - this is great! The whole effort is really something to see - keep posting!
Cheers
Nick
Hosted by Darren Baker
A Dragon Wagon odyssey
Posted: Friday, February 28, 2014 - 06:33 PM UTC

JLModels

Joined: February 15, 2014
KitMaker: 117 posts
Armorama: 117 posts
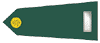
Posted: Saturday, March 01, 2014 - 05:17 AM UTC
At this point I could have started on the cab exterior, or painting the cab interior, but instead opted to work on the heavy-duty dual winches.
To be honest the twin winch setup is actually pretty well molded, but like most things in this kit, it’s simplified. Both the front and rear winch frames suffer from poorly placed injection pin marks, as well as molded in locator tabs which are visible in the end product and are not in the real thing. The braces which go between the frames are also very thick compared to the real ones and needed substantial thinning down, as well as a replacement of the rod that goes between the two braces with some 0.020 plastic rod. The winch cable has been wound onto the winches after the nylon cable was stained black with Mr. surface 1500 black, and then kept in place with Tamiya masking tape.



With all of that dealt with I turned to the two bigger problems with the winches: The tire-changing crane mount and the lever systems. The tire-changing crane was usually stowed on the floor of the transport trailer when not in use, and only left erected when the Dragon Wagon wasn’t towing a trailer (or at least that’s how the Army’s technical manual says it was supposed to be, and also most of the pictures of the real vehicles bear that out.) The problem is first that the support braces for the crane holder are molded much to thick. The upper one is thankfully replaced with a photoetched Royal Models part, but the lower brace I had to fashion from 0.010 thick sheet styrene. The strange part is that the upper part of the mount, above the upper photoetched piece, is molded into the crane. Because I had the old Dragon Wagon kit, I simply cut the base off the crane from that one, hollowed it out as delicately as I could, and glued it on. This allows me to leave the new crane intact, simply sand off the bottom ridge, lengthening and stowing it in the trailer for later.
I also modified the crane itself to represent the folded down position.

The lever mechanisms took the most time and delicacy. The Tamiya winch actually includes all the main levers, and some were replaced by more scale-thickness Royal Models parts, but the connecting rods at their bases that connect to either the gearboxes or the braking systems were completely absent and had to be scratchbuilt from brass strip and styrene rod. If you are going to do this, be sure you have as many references as possible. The two Tankograd books were helpful but even they were missing some angles I needed to see, so the Ampersand publishing Dragon Wagon book and The Military Machine book, as well as various online walkarounds were used to help complete the picture. This is also where it was important to remove all of the molded-on Tamiya locating tabs on the winch frames, as its impossible to put through some of the connecting levers with those still in place (namely the two which go through the frame for the front winch).
Because I wanted to have the winch in operation, in particular pulling in a towed load, I altered the position of the front winch clutch and gearshift lever to the ‘IN’ position, as shown in the Tankograd In Detail book.
Once the front and rear winches were done, it was time to work on the parts I was most dreading since post 4: The winch chain drive assemblies. As with the rear axel unit, I decided to use the Royal Models chain parts, which look a lot better but are a mammoth pain to assemble. On the plus side, this time the sprockets are all photoetched brass rather than poorly-molded resin, so at least there’s that. But it still meant setting up the chopper, cutting 0.020 styrene rod to within 0.75mm +/- 0.03mm, measuring each one with a digital caliper, etc, etc.
One nice thing about the Royal Models set is that it includes the ‘bottom’ chain, which isn’t in the Tamiya kit and is the chain that connects the winches to the power take-off of the secondary transmission.


To be honest the twin winch setup is actually pretty well molded, but like most things in this kit, it’s simplified. Both the front and rear winch frames suffer from poorly placed injection pin marks, as well as molded in locator tabs which are visible in the end product and are not in the real thing. The braces which go between the frames are also very thick compared to the real ones and needed substantial thinning down, as well as a replacement of the rod that goes between the two braces with some 0.020 plastic rod. The winch cable has been wound onto the winches after the nylon cable was stained black with Mr. surface 1500 black, and then kept in place with Tamiya masking tape.



With all of that dealt with I turned to the two bigger problems with the winches: The tire-changing crane mount and the lever systems. The tire-changing crane was usually stowed on the floor of the transport trailer when not in use, and only left erected when the Dragon Wagon wasn’t towing a trailer (or at least that’s how the Army’s technical manual says it was supposed to be, and also most of the pictures of the real vehicles bear that out.) The problem is first that the support braces for the crane holder are molded much to thick. The upper one is thankfully replaced with a photoetched Royal Models part, but the lower brace I had to fashion from 0.010 thick sheet styrene. The strange part is that the upper part of the mount, above the upper photoetched piece, is molded into the crane. Because I had the old Dragon Wagon kit, I simply cut the base off the crane from that one, hollowed it out as delicately as I could, and glued it on. This allows me to leave the new crane intact, simply sand off the bottom ridge, lengthening and stowing it in the trailer for later.
I also modified the crane itself to represent the folded down position.

The lever mechanisms took the most time and delicacy. The Tamiya winch actually includes all the main levers, and some were replaced by more scale-thickness Royal Models parts, but the connecting rods at their bases that connect to either the gearboxes or the braking systems were completely absent and had to be scratchbuilt from brass strip and styrene rod. If you are going to do this, be sure you have as many references as possible. The two Tankograd books were helpful but even they were missing some angles I needed to see, so the Ampersand publishing Dragon Wagon book and The Military Machine book, as well as various online walkarounds were used to help complete the picture. This is also where it was important to remove all of the molded-on Tamiya locating tabs on the winch frames, as its impossible to put through some of the connecting levers with those still in place (namely the two which go through the frame for the front winch).
Because I wanted to have the winch in operation, in particular pulling in a towed load, I altered the position of the front winch clutch and gearshift lever to the ‘IN’ position, as shown in the Tankograd In Detail book.
Once the front and rear winches were done, it was time to work on the parts I was most dreading since post 4: The winch chain drive assemblies. As with the rear axel unit, I decided to use the Royal Models chain parts, which look a lot better but are a mammoth pain to assemble. On the plus side, this time the sprockets are all photoetched brass rather than poorly-molded resin, so at least there’s that. But it still meant setting up the chopper, cutting 0.020 styrene rod to within 0.75mm +/- 0.03mm, measuring each one with a digital caliper, etc, etc.
One nice thing about the Royal Models set is that it includes the ‘bottom’ chain, which isn’t in the Tamiya kit and is the chain that connects the winches to the power take-off of the secondary transmission.



JLModels

Joined: February 15, 2014
KitMaker: 117 posts
Armorama: 117 posts
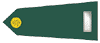
Posted: Tuesday, March 04, 2014 - 11:39 AM UTC
I finally reached the point where I can’t proceed any further without painting the cab interior, but before I get to that I need to work on the driver figure. I plan to have two figures in the cab and the rest of the crew outside of it working the winch, the load, etc. One of the figures will be standing in the roof-mounted machine gun ring and can be added later. The driver figure, however, needs to be cleaned up, painted and added before the rest of the interior is buttoned up since he can’t be inserted later.
With that in mind I began fitting various figures to see which one worked best. I tested two different Verlinden US driver figures I happened to have, a The Bodi driver figure, and finally the Tamiya plastic figure included with the kit. Due to the simplicity of the standard US uniforms there really wasn’t much of a detail difference between all of them, with the exception of the head and hands (resin figures are almost always better in that respect).
The Tamiya figure was found to fit the best, but it includes absolutely terrible hands and head. So those were swapped with Hornet resin hands and one of their ‘heads with ww2-style haircuts’, as I didn’t think the driver would be wearing his helmet all the time while in the cab. I also wanted him looking back out the window so I cut his torso into slices, angled it so he was looking back over his shoulder, made sure one of his arms fit over the back of the seat, and then used Apoxie sculpt to smooth things out and remake the obliterated detail.


I don’t usually modify figures this much, but I wanted him in a specific pose that no manufacturer had made that I could find. It actually was pretty easy to do, so who knows, maybe I’ll start altering figures more often!
Next it was time to prime the interior! This began with a wash of all of the parts with Windex, then water, and then an extended drying time in my paint hood with the fan on to ensure the parts were as clean and dry as they possibly could be.
I recently decided to run a little experiment with primers. I tested half a dozen different paint and primer combinations on plastic, metal gun barrels and photoetch.
The list includes:
Tamiya Grey spray primer
Tamiya superfine white primer
Mr. Surfacer 1000
Vallejo grey primer
no primer with just Tamiya paint
no primer with just Vallejo paint
no primer with just AK-interactive paint.
I tried all of the above at 15psi, 20psi and 25psi, as well as on cleaned and uncleaned surfaces. The test included rubbing the parts hard with my thumb, scraping them with my finger nail, and scraping them with a wood and metal scraper tool.
The Vallejo and AK-interactive paints were thinned with their own thinners, but water was also tested. The Tamiya paint was thinned with their own X20a thinner or their own laquer thinner (both were tried) and the Mr. Surfacer was thinner with Tamiya laquer thinner. The Tamiya spraycan primers were decanted, left to settle to remove air bubbles, and sprayed unthinned.
All were left for 24 hrs to cure before testing them.
For bare plastic, honestly, there’s no much difference. Any of the above work fine, although the Vallejo and Ak-interactive paints did have a bit less adhesion then the others. I actually couldn’t really tell the difference between the Tamiya primers, Mr. Surfacer and the plain, unprimed Tamiya paints on either plastic or photoetch for that matter.
After completing these tests, a few things were noted. If you use Ak-interactive paints, or Vallejo paints, priming is a good idea on almost anything. It does improve adhesion a little on plastic, but the real difference is on photoetch. Mr. Surfacer, Tamiya grey primer and superfine white primer from the spraycan held a clear advantage when sprayed on photoetch and especially on aluminum gun barrels. Any of the unprimed paints flaked off really easily on the gun barrel, and the Vallejo and Ak-interactive paints flaked really easily on both photoetch and the gun barrel. But add either Mr. Surfacer, Tamiya fine or superfine primer and they held well against rubbing, my nail, and to a lesser extent small impacts from a scraper tool. The Vallejo Grey primer was tolerable, but frankly not as good as the other primers. It did help adhesion of the Ak-interactive and Vallejo paints to plastic, and a little bit to the photoetch, but frankly I was not impressed compared to the other primers. It’s also more difficult to sand, often peeling more than the others.
From this I was able to draw a few conclusions. While Vallejo and AK-interactive paints are okay when sprayed on plastic alone, they do benefit from primer. If you plan to put them on resin, photoetch or a metal gun barrel then they DEFINITELY need priming, IMHO. Otherwise they peel or flake off way too easily. Vallejo grey primer did not impress me. It was okay, and better than nothing on metal and photoetch, but every single time I repeated this it faired worse than the Mr. Surfacer and Tamiya primers.
I found my best combination was Mr. Surfacer 1000 diluted 3:1 laquer thinner to paint and sprayed at between 15 and 20psi. The Tamiya primers were okay, but they’re a pain to decant from the can, let degass and then airbrush. You could spray them directly but I much prefer to airbrush my primer over using a spraycan, since you have more control and won’t obscure any detail like a heavier coat of a spraycan primer can. I understand Tamiya makes these primers in jars as well, but they aren’t carried in any of the hobby stores anywhere near me. The Mr. Surfacer 1000, on the other hand is more easily available, sprays beautifully when thinner, doesn’t obscure detail and held best on plastic, photoetch and gun barrels. Since I plan to try color modulation for this model and will be using the AK-interactive allied green set on a model with a lot of small resin and photoetched detail, I decided to prime with Mr. Surfacer.
That being said, if you don’t have much resin or photoetch on your model, you might be able to get away with no primer using either Vallejo or AK-interactive paints, and especially if you plan to use Tamiya paints. I was actually really impressed with its hold. However given that I already had the AK-interactive color modulation set, I decided to go with that and prime.
After priming the interior parts, I began by spraying the large surfaces with the AK-interactive allied green color modulation set. I didn’t need to thin the paints at all, as they flowed well through my Iwata HP-C+ really well at 18psi out of the bottle. They covered beautifully, starting with the ‘Olive drab dark shadow’ in the crevices and corners, followed by their ‘olive drab dark base’ and ‘olive drab light base’ in the large open areas. Any horizontal area that would be illuminated by either the overhead cab light, or the windows/roof opening was airbrushed with the ‘olive drab highlight’ color.
While I understand the purists decrying color modulation as artificial and not realistic, I think I like the effect, especially when it will be toned down with filters, washes and weathering. It adds a lot to the otherwise boring and dull overall olive drab paint scheme. Also, lets face it, olive drab as a color was never produced in a single perfect shade by just one company, and also faded pretty well in the sun over time. So as far as I’m concerned as long as it looks right it should be fine.
The smaller details were painted their appropriate colors, eg: red for the extinguishers, a Hellbau RLM65 for the decontamination cylinders, khaki for the seat covers and straps, chocolate brown for the ubiquitous brown wool blankets the US army used, and dark green for the flashlights. Anywhere to receive a decal was first airbrushed with some future floor wax for a gloss coat, then microset and microsol were used on the decals. The decals themselves either came with the kit, or were Archer Fine transfers waterslide decals. The Archer transfer decals were glorious to use and nicely thin. The Tamiya ones, on the other hand, were rather thick so I had to cut them as close as possible to trim off the excess thick decal film.
The instrument panel was a bit of an unusual issue. I used the more accurate Royal Models one, but Royal models goofed on the photo negative of the instruments themselves. They all look like simplified basic dials, where as the real ones had a tachometer in one of the large dials, a differently shaped oil meter gauge, etc, which all looked different. Shockingly the Eduard negative has all of the correct gauges done perfectly. The only issue was that they don’t fit the Royal Models panel! Every gauge is slightly off vertically or horizontally so they don’t line up with the Royal Models photoetched holes. I debated just using the Eduard panel and being done with it, but instead decided to cut apart the film negative so each gauge was separate, then put in each gauge individually and glue each one down. This was a massive pain in the ass, but now I have a nice, accurate instrument panel where every dial looks like it’s supposed to. A bit of white paint behind the film makes the gauges pop. Some Archer transfers generic placards finished it off.
The cab and roof wiring was a bit of an issue, in that I have pictures of Dragon Wagons showing the wiring olive drab colored or Black. The Black wiring always seems to be in the restored Dragon Wagon images though and not in the original, so I decided to leave it olive drab.



Posted: Wednesday, March 05, 2014 - 10:41 AM UTC
Question: On the real deal is the co-driver/commander's map board wood or metal?

JLModels

Joined: February 15, 2014
KitMaker: 117 posts
Armorama: 117 posts
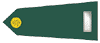
Posted: Wednesday, March 05, 2014 - 12:37 PM UTC

Metal, definitely. It has a hinge at the back that allows the top to open, presumably for map storage, and a little locking ring at the front to keep the maps or other sensitive stuff locked up.


JLModels

Joined: February 15, 2014
KitMaker: 117 posts
Armorama: 117 posts
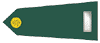
Posted: Thursday, March 06, 2014 - 01:58 PM UTC
At this point it was time for washes and weathering.
I began with a coat of Vallejo satin mixed 50/50 with their airbrush thinner and sprayed at 18psi. After 24hrs of drying time, Mig productions green vehicle filters, concentrating the darker ones along the sides and floor, and the lighter ones on the top of the engine bay. I made about 3 applications of them, and while they didn’t change much in terms of the tone of the paint, they did a little extra color variation to break up the otherwise boring olive drab tone.
I used AK-interactive’s ‘weathering for green vehicles’ set dark brown wash. This is the first time I’ve used an enamel-based wash, as I previously always used oil-based washes. I have to say I’m impressed. With oil washes, no matter what dilution of oil paint and what thinner, I’d always get large paint sedimentation and the wash would never run as smoothly as I’d like. The enamel wash worked pretty much identically to an oil wash, but ran smoother and was consistently diluted, with little sedimentation. The excess cleaned up nicely with white spirits.
The metal parts, namely the spare 50cal barrel and the two Thompson machine guns were worked on next. All of the metal areas received a coat of Vallejo ‘panzer aces tanker black’, which I find is a close match to Tamiya Nato black and a much more realistic color to use then a straight black, being a VERY dark grey. This then got a polishing with Ak-interactive’s Dark steel pigment. This went on nicely and polished up with a cotton bud to look like a nice gunmetal. That being said, while I did like their steel pigment, It works and looks exactly like my old standby, graphite powder lubricant from the hardware store, or graphite from the art supply store, so perhaps you might want to save your money there.


To further the interior weathering, I began by adding small dots of various oil colors, including a yellow, a white, and a brown to all of the flat surfaces and then blending them with some white spirits. Very much like filters, this adds tonal variation and breaks up the boring olive drab tone. That being said, I’m in no way convinced that both this and filters are necessary. In fact they seem a little redundant, unless you have a single large panel on your AFV that you want to vary the tone of in different areas of that same single panel, where the oil dot method would be superior to a filter. Beyond that though, I truly don’t think both are needed. But I came to this conclusion only after I’d done them already. Oops! At least no harm done.
I followed this up with some drybrushing using lightened Vallejo Brown Violet, which contrary to its color name nicely resembled a light olive drab. I then finished off the basic weathering using some mig productions powders, including their track brown a European dust, all applied sparingly and then wetted down with mineral spirits to ‘fix’ it in place. I concentrated mostly on the floor and wheel arches; effectively anywhere a GI would like walk around the cab. Lastly I added a bit of spilled oil from Ak-interactive’s ‘Fresh engine oil’ on the floor near the hatches which lead to the fuel tanks.
A massive word of warning here. When I applied this stuff I tried to work it a little with a paint brush and was shocked when it ate all the way through the paint layers to the primer coat! I though this would be just another enamel product and wouldn’t harm the acrylic, and maybe something just went wrong with mine, but all of a suddenly I was looking at the Mr. surface primer gray layer and freaking out a little. Thankfully I managed to recover by adding and blending the color modulation base colors and then topping with some more pigment, then adding the engine oil and NOT TOUCHING IT. It did dry to look like a nice little bit of spilled oil, but all I can say right now is be careful when using this stuff.


I began with a coat of Vallejo satin mixed 50/50 with their airbrush thinner and sprayed at 18psi. After 24hrs of drying time, Mig productions green vehicle filters, concentrating the darker ones along the sides and floor, and the lighter ones on the top of the engine bay. I made about 3 applications of them, and while they didn’t change much in terms of the tone of the paint, they did a little extra color variation to break up the otherwise boring olive drab tone.
I used AK-interactive’s ‘weathering for green vehicles’ set dark brown wash. This is the first time I’ve used an enamel-based wash, as I previously always used oil-based washes. I have to say I’m impressed. With oil washes, no matter what dilution of oil paint and what thinner, I’d always get large paint sedimentation and the wash would never run as smoothly as I’d like. The enamel wash worked pretty much identically to an oil wash, but ran smoother and was consistently diluted, with little sedimentation. The excess cleaned up nicely with white spirits.
The metal parts, namely the spare 50cal barrel and the two Thompson machine guns were worked on next. All of the metal areas received a coat of Vallejo ‘panzer aces tanker black’, which I find is a close match to Tamiya Nato black and a much more realistic color to use then a straight black, being a VERY dark grey. This then got a polishing with Ak-interactive’s Dark steel pigment. This went on nicely and polished up with a cotton bud to look like a nice gunmetal. That being said, while I did like their steel pigment, It works and looks exactly like my old standby, graphite powder lubricant from the hardware store, or graphite from the art supply store, so perhaps you might want to save your money there.


To further the interior weathering, I began by adding small dots of various oil colors, including a yellow, a white, and a brown to all of the flat surfaces and then blending them with some white spirits. Very much like filters, this adds tonal variation and breaks up the boring olive drab tone. That being said, I’m in no way convinced that both this and filters are necessary. In fact they seem a little redundant, unless you have a single large panel on your AFV that you want to vary the tone of in different areas of that same single panel, where the oil dot method would be superior to a filter. Beyond that though, I truly don’t think both are needed. But I came to this conclusion only after I’d done them already. Oops! At least no harm done.
I followed this up with some drybrushing using lightened Vallejo Brown Violet, which contrary to its color name nicely resembled a light olive drab. I then finished off the basic weathering using some mig productions powders, including their track brown a European dust, all applied sparingly and then wetted down with mineral spirits to ‘fix’ it in place. I concentrated mostly on the floor and wheel arches; effectively anywhere a GI would like walk around the cab. Lastly I added a bit of spilled oil from Ak-interactive’s ‘Fresh engine oil’ on the floor near the hatches which lead to the fuel tanks.
A massive word of warning here. When I applied this stuff I tried to work it a little with a paint brush and was shocked when it ate all the way through the paint layers to the primer coat! I though this would be just another enamel product and wouldn’t harm the acrylic, and maybe something just went wrong with mine, but all of a suddenly I was looking at the Mr. surface primer gray layer and freaking out a little. Thankfully I managed to recover by adding and blending the color modulation base colors and then topping with some more pigment, then adding the engine oil and NOT TOUCHING IT. It did dry to look like a nice little bit of spilled oil, but all I can say right now is be careful when using this stuff.


Posted: Thursday, March 06, 2014 - 05:49 PM UTC
Hi Jason - wish I could add something smart about the content of your build - but I can't - instead, I can just restate that I think this is a great build - now the winch and the interior. Wow! Please keep posting - the modeling info along the way is helpful too
Cheers
Nick
Cheers
Nick
Posted: Saturday, March 08, 2014 - 03:58 AM UTC
Jason - truly beautiful work.
I hope no one minds but I would like to interject a detailing possibility on the Dragon Wagon trailer that is often over looked.
While the small jib crane is most often posed on the tractor for removing the spare tire when needed. There are also four points located on the trailer that were designed to accept the jib crane for changing the tires there.
On the Tamiya kit these mounting points are marked by the four screw holes used to secure the metal rebar into the body of the trailer. However if one were to substitute a strong glue like two-part epoxy for the metal screws this frees up the holes for their original intended purpose which was to mount this light weight crane.
My work on this is in no way on a par with yours but I thought the general information might be of interest. Cheers

That's an M-199 two-axle post-war towing dolly under the trailer in this photo. This allowed ballast tractors such as the Diamond T to tow the M-26 trailer.

Here is the post-war A1 trailer with the jib crane installed in the rear most position but these fittings were available on the earlier trailer as well.
(In this case the trailer is being pulled by the post-war T-26 Sterling Tractor.) (Photo provided by Tony Gibbs.)
I hope no one minds but I would like to interject a detailing possibility on the Dragon Wagon trailer that is often over looked.
While the small jib crane is most often posed on the tractor for removing the spare tire when needed. There are also four points located on the trailer that were designed to accept the jib crane for changing the tires there.
On the Tamiya kit these mounting points are marked by the four screw holes used to secure the metal rebar into the body of the trailer. However if one were to substitute a strong glue like two-part epoxy for the metal screws this frees up the holes for their original intended purpose which was to mount this light weight crane.
My work on this is in no way on a par with yours but I thought the general information might be of interest. Cheers

That's an M-199 two-axle post-war towing dolly under the trailer in this photo. This allowed ballast tractors such as the Diamond T to tow the M-26 trailer.


Here is the post-war A1 trailer with the jib crane installed in the rear most position but these fittings were available on the earlier trailer as well.
(In this case the trailer is being pulled by the post-war T-26 Sterling Tractor.) (Photo provided by Tony Gibbs.)
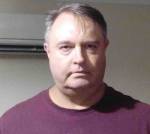
airborne1

Joined: April 15, 2006
KitMaker: 915 posts
Armorama: 797 posts

Posted: Sunday, March 09, 2014 - 06:50 PM UTC
There is some excellent work going on with this build Michael.
Keep posting the images.
Super work so far
Thanks .
Keep posting the images.
Super work so far
Thanks .

JLModels

Joined: February 15, 2014
KitMaker: 117 posts
Armorama: 117 posts
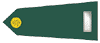
Posted: Monday, March 10, 2014 - 08:03 AM UTC
Time to bring the cab to life, as it were.
The driver figure was primed using Mr. surface again, and his clothing was base-painted with Tamiya Dark Yellow and Flat earth. Now the fun began: painting his head.
I truly believe a figure or two, well-painted and well-fitted, makes or breaks a model. I actually refuse to build a model without at least one figure now, since I think it truly brings a model to life and provides a viewer with a true sense of scale.
That being said, I despise painting heads with a passion like unto the gods. I have tried both oils and acrylics, currently settling on Vallejo Acrylics. It always takes me hours to get a single head looking okay, and I often have to repaint several times. All I can say is that I managed to paint this figure’s head decently, to the maximum of my capabilities. I am by no means a figure painting master though, and there are probably hundreds of people on this site who can do it better than I, but it’s an area I am currently working hard on improving.
For those who have been avoiding figures or are just curious, I base painted the head with Vallejo Brown Sand, then added progressive highlights using a combination of Brown Sand and Basic Skintone, and added shadows using Brown Sand combined with Burnt Cadmium Red. I used the tutorials in the Osprey book ‘Modelling Fallschirmjager figures’. This book is often highly recommended on figure modeling websites for its head painting tutorial, and after watching and reading dozens of them, I have to agree. It is one of the clearest tutorials on how to paint a decent head, and I highly recommend it.
The patches on his jacket are archer transfers, added using the usual method mentioned in my previous posts.



I wanted this Dragon Wagon to look lived in, so I had to include some soldiers gear and stuff I thought would ‘liven the place up’. I added a map, a letter and pair of binoculars to the commander’s table, a pack of cigarettes opened with the cigarettes visible on the engine deck as wel as a tied-down wine bottle, a ‘pin up’ on one of the left hand side engine panels, and a couple of tools from the spares bin, as well as a dirty rag made of thinly-rolled epoxy putty. I didn’t want to overwhelm the space by any means, or randomly toss in packs and bedrolls to the point where no one could sit comfortably in the cab. I think I achieved a nice balance.
I also noticed that my Verlinden M8 greyhound armored car detail set included a more accurate map holder that matched with my references better than the Tamiya one so I swapped that one onto the roof.



The driver figure was primed using Mr. surface again, and his clothing was base-painted with Tamiya Dark Yellow and Flat earth. Now the fun began: painting his head.
I truly believe a figure or two, well-painted and well-fitted, makes or breaks a model. I actually refuse to build a model without at least one figure now, since I think it truly brings a model to life and provides a viewer with a true sense of scale.
That being said, I despise painting heads with a passion like unto the gods. I have tried both oils and acrylics, currently settling on Vallejo Acrylics. It always takes me hours to get a single head looking okay, and I often have to repaint several times. All I can say is that I managed to paint this figure’s head decently, to the maximum of my capabilities. I am by no means a figure painting master though, and there are probably hundreds of people on this site who can do it better than I, but it’s an area I am currently working hard on improving.
For those who have been avoiding figures or are just curious, I base painted the head with Vallejo Brown Sand, then added progressive highlights using a combination of Brown Sand and Basic Skintone, and added shadows using Brown Sand combined with Burnt Cadmium Red. I used the tutorials in the Osprey book ‘Modelling Fallschirmjager figures’. This book is often highly recommended on figure modeling websites for its head painting tutorial, and after watching and reading dozens of them, I have to agree. It is one of the clearest tutorials on how to paint a decent head, and I highly recommend it.
The patches on his jacket are archer transfers, added using the usual method mentioned in my previous posts.



I wanted this Dragon Wagon to look lived in, so I had to include some soldiers gear and stuff I thought would ‘liven the place up’. I added a map, a letter and pair of binoculars to the commander’s table, a pack of cigarettes opened with the cigarettes visible on the engine deck as wel as a tied-down wine bottle, a ‘pin up’ on one of the left hand side engine panels, and a couple of tools from the spares bin, as well as a dirty rag made of thinly-rolled epoxy putty. I didn’t want to overwhelm the space by any means, or randomly toss in packs and bedrolls to the point where no one could sit comfortably in the cab. I think I achieved a nice balance.
I also noticed that my Verlinden M8 greyhound armored car detail set included a more accurate map holder that matched with my references better than the Tamiya one so I swapped that one onto the roof.



panamadan

Joined: July 20, 2004
KitMaker: 1,513 posts
Armorama: 1,449 posts

Posted: Monday, March 10, 2014 - 02:21 PM UTC
Nice job Jason. That's actually a flag holder and is still in use today.
Dan
Dan

JLModels

Joined: February 15, 2014
KitMaker: 117 posts
Armorama: 117 posts
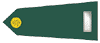
Posted: Monday, March 10, 2014 - 03:00 PM UTC
Dan,
whoops! You're right, I meant flag holder but typed the wrong thing. Thanks for catching that.
whoops! You're right, I meant flag holder but typed the wrong thing. Thanks for catching that.

panamadan

Joined: July 20, 2004
KitMaker: 1,513 posts
Armorama: 1,449 posts

Posted: Tuesday, March 11, 2014 - 12:04 AM UTC


JLModels

Joined: February 15, 2014
KitMaker: 117 posts
Armorama: 117 posts
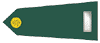
Posted: Tuesday, March 11, 2014 - 03:18 AM UTC
The Dragon Wagon accessories came next, starting with the oxygen and acetylene bottles. Like most, these are molded in two halves, which leaves a large seam. This is also an area where the Eduard exterior set came in handy, as the Royal Models one only has a small part to improve the bottle latches, whereas the Eduard one has new straps and latches for all three bottles. So I removed the straps, latches, seam and ended with a nice, smooth bottles I could fill and sand.
The mounting plate for these bottles is pretty crappy in the kit, being way too thick with the holders molded as part of the bottles. I replaced this with the parts included in the Royal Models set #2, soldered together.


The machine gun mount and ring was next. The ring went together nicely with only a few bolts missing from it. A note on those bolts though: for some reason they appear on some Dragon Wagons but on others the ring was just welded down. As far as I can tell either is correct and it may just be a production difference.
Surprisingly, the Tamiya mount is actually a pretty reasonable replica of the real thing, needing only the handle on the right side, as well as a couple of blocks and bolts on either side of the pintle mount. The handle that hangs down under the mount is part of the Royal Models set.

The fifth wheel was a joy to build, minus the injection pin marks of course. It’s actually pretty much perfectly accurate, missing only 4 holes in the main brace on the front and rear, and two on the sides. I don’t know what these holes are for, if they’re just lightening holes or if they’re for some adjustment mechanism, but they’re there in every image so I drilled them out with a pin vise and a #62 bit.
The handle at the front of the fifth wheel was thinned significantly and the notch it slides into cut into it, but that’s all it took to complete that subassembly.


The Vertical Lift Device, or A-frame, that mounts to the back of the Dragon Wagon came next, and the way Tamiya designed it, it’s a bit of a mess. The actual A-frame has the hinge points in the center of the angle piece, but if you assemble the Tamiya part as per instructions they end up on the edges. This isn’t as big a deal as the side plates, which Tamiya molded to secure to the A-frame with a second plate that doubles the thickness of the A-frame in those regions. Not only does this double plate not exist in the real thing, but removing it also means the crossbars with their circular mounting holes are suddenly too short and don’t connect properly to the A-frame sides.
Also in error, the reverse side of the A-frame as two small pads along the top bar which are supposed to represent the rubber padding used to keep the A-frame from damaging the frame when in the down position. In the Tamiya kit these are vertical, going from ‘top’ to ‘bottom’ of the A-frame, when in reality they should go from left to right, or side-to-side. These then needed to be removed and the mounts made from folded sheet brass topped with some styrene strip to represent the rubber.
The end result of all of this is that I had to cut off the angled cross braces, assemble the main A-frame, fill all of the locating slots/holes for the hinge points, then cut the hinge points off their mounts, glue them into the locations they’re supposed to be in, scratchbuild new side plates, new angled cross pieces, and new circular mounting points at the ends of the cross pieces. I also added all of the weld seams using the Archer Transfers resin micro weld seam set, as they looked good and were much easier to apply on a flat surface than gluing down sprue, melting it with more glue and then texturing it with tweezers.
Thankfully at the end of all of this I wound up with an A-frame that perfectly matches all of the reference images.


The mounting plate for these bottles is pretty crappy in the kit, being way too thick with the holders molded as part of the bottles. I replaced this with the parts included in the Royal Models set #2, soldered together.


The machine gun mount and ring was next. The ring went together nicely with only a few bolts missing from it. A note on those bolts though: for some reason they appear on some Dragon Wagons but on others the ring was just welded down. As far as I can tell either is correct and it may just be a production difference.
Surprisingly, the Tamiya mount is actually a pretty reasonable replica of the real thing, needing only the handle on the right side, as well as a couple of blocks and bolts on either side of the pintle mount. The handle that hangs down under the mount is part of the Royal Models set.

The fifth wheel was a joy to build, minus the injection pin marks of course. It’s actually pretty much perfectly accurate, missing only 4 holes in the main brace on the front and rear, and two on the sides. I don’t know what these holes are for, if they’re just lightening holes or if they’re for some adjustment mechanism, but they’re there in every image so I drilled them out with a pin vise and a #62 bit.
The handle at the front of the fifth wheel was thinned significantly and the notch it slides into cut into it, but that’s all it took to complete that subassembly.


The Vertical Lift Device, or A-frame, that mounts to the back of the Dragon Wagon came next, and the way Tamiya designed it, it’s a bit of a mess. The actual A-frame has the hinge points in the center of the angle piece, but if you assemble the Tamiya part as per instructions they end up on the edges. This isn’t as big a deal as the side plates, which Tamiya molded to secure to the A-frame with a second plate that doubles the thickness of the A-frame in those regions. Not only does this double plate not exist in the real thing, but removing it also means the crossbars with their circular mounting holes are suddenly too short and don’t connect properly to the A-frame sides.
Also in error, the reverse side of the A-frame as two small pads along the top bar which are supposed to represent the rubber padding used to keep the A-frame from damaging the frame when in the down position. In the Tamiya kit these are vertical, going from ‘top’ to ‘bottom’ of the A-frame, when in reality they should go from left to right, or side-to-side. These then needed to be removed and the mounts made from folded sheet brass topped with some styrene strip to represent the rubber.
The end result of all of this is that I had to cut off the angled cross braces, assemble the main A-frame, fill all of the locating slots/holes for the hinge points, then cut the hinge points off their mounts, glue them into the locations they’re supposed to be in, scratchbuild new side plates, new angled cross pieces, and new circular mounting points at the ends of the cross pieces. I also added all of the weld seams using the Archer Transfers resin micro weld seam set, as they looked good and were much easier to apply on a flat surface than gluing down sprue, melting it with more glue and then texturing it with tweezers.
Thankfully at the end of all of this I wound up with an A-frame that perfectly matches all of the reference images.



JLModels

Joined: February 15, 2014
KitMaker: 117 posts
Armorama: 117 posts
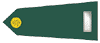
Posted: Wednesday, March 12, 2014 - 02:18 PM UTC
Next up was more exterior details.
I finished up the exhausted, using the Royal Models mesh heated over an open flame, although the Tamiya or Eduard ones look pretty much as good.

As you can see I’ve replaced the exhaust straps with 0.010 x 0.040 strip styrene, as well as added a few small brackets around the exhaust. This is an area with a lot of variability in the real thing. Some Dragon Wagons have a securing strip at the top of the exhaust, some at the bottom, some have both and some have neither. The exhaust screen was also easily damaged in the field, so many images show it cut in half, or cut down. I chose this version but there’s a lot of options here.
The brass A-frame arms are supplied by Tamiya as just plain brass tube, but the real thing had two sets of holes used to slide pins through when the A-frame was raised. I drilled these first with a sharp X-acto knife, and then widened the hole with a #70 drill bit. Trying with just the drill bit alone, without starting first with an x-acto knife cause the drill bit to just slide around the tube and prevent proper alignment. This chewed up x-acto #11 blades, but worked well.

Finally I began working on the lights around the cab exterior, or at least as much of them as I could without attaching them to the model. The light protectors were a bit of a pain because I made the mistake of trying to solder the entire thing together. While the outer loop soldered fine, the brass rod on the inside of the loop was impossible to solder. I’d get one perfect, only to try another and have the first one’s joint melt over and over. I finally got one of them done after 3 hrs, only to drop it on the floor and break off one of the rods!
So I cleaned off all of the excess solder and resorted to superglue… which worked beautifully and took 5min. Lesson learned!

One last note after the rear spotlights (those are the two at the front of the above image): It appears there were two versions of these. One had a handle on the back of each spotlight and a smooth, semi-circular mount (like the ones in the image> while the other had no handle and an angular mount. The Royal models kit comes with the latter, while the Tamiya stock kit comes with the former. I chose the former as they appear in most of the images I’ve found, but I have found pictures of both variants. The Eduard kit, in accordance with Eduard’s poor research, actually includes instructions for some bizarre mashup of the two with an angular mount AND handle, but I’ve never seen an actual image of this anywhere.
I finished up the exhausted, using the Royal Models mesh heated over an open flame, although the Tamiya or Eduard ones look pretty much as good.

As you can see I’ve replaced the exhaust straps with 0.010 x 0.040 strip styrene, as well as added a few small brackets around the exhaust. This is an area with a lot of variability in the real thing. Some Dragon Wagons have a securing strip at the top of the exhaust, some at the bottom, some have both and some have neither. The exhaust screen was also easily damaged in the field, so many images show it cut in half, or cut down. I chose this version but there’s a lot of options here.
The brass A-frame arms are supplied by Tamiya as just plain brass tube, but the real thing had two sets of holes used to slide pins through when the A-frame was raised. I drilled these first with a sharp X-acto knife, and then widened the hole with a #70 drill bit. Trying with just the drill bit alone, without starting first with an x-acto knife cause the drill bit to just slide around the tube and prevent proper alignment. This chewed up x-acto #11 blades, but worked well.

Finally I began working on the lights around the cab exterior, or at least as much of them as I could without attaching them to the model. The light protectors were a bit of a pain because I made the mistake of trying to solder the entire thing together. While the outer loop soldered fine, the brass rod on the inside of the loop was impossible to solder. I’d get one perfect, only to try another and have the first one’s joint melt over and over. I finally got one of them done after 3 hrs, only to drop it on the floor and break off one of the rods!
So I cleaned off all of the excess solder and resorted to superglue… which worked beautifully and took 5min. Lesson learned!

One last note after the rear spotlights (those are the two at the front of the above image): It appears there were two versions of these. One had a handle on the back of each spotlight and a smooth, semi-circular mount (like the ones in the image> while the other had no handle and an angular mount. The Royal models kit comes with the latter, while the Tamiya stock kit comes with the former. I chose the former as they appear in most of the images I’ve found, but I have found pictures of both variants. The Eduard kit, in accordance with Eduard’s poor research, actually includes instructions for some bizarre mashup of the two with an angular mount AND handle, but I’ve never seen an actual image of this anywhere.

JLModels

Joined: February 15, 2014
KitMaker: 117 posts
Armorama: 117 posts
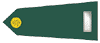
Posted: Friday, March 14, 2014 - 09:07 AM UTC
Assembling the exterior details is next. This, of course, started off by gluing the cab onto the frame. I was actually pretty amazed at how well it fits, without needing a single bit of filler around the wheel wells. The fuel tank covers, which are located just behind the cab steps, were another matter. Tamiya molded these pretty basic, just as L-shaped pieces of plastic, which while doing the job, are missing a lot of bolt and weld seam detail. This was added after a lot of filling and sanding.

The rest of the detail additions went pretty smoothly. Since I didn’t want to risk getting sanding dust into my newly finished interior, I added the armored covers to the openings and taped them down with Tamiya tape, as well as covering the roof opening.
Most of the detailing here came from the royal Models photoetch set, with only the oxygen and acetelyene straps and the sledge hammer holders coming from the Eduard exterior detail set.
The oxygen and acetelyene straps are one area where Eduard really got it right. They are perfectly sized, easy to fold, and even partially operational (operational but very delicate). Royal models just added a little handle to the molded on Tamiya straps.
All of the little tie-downs on the roof and for the tools are tiny pieces of 0.030 brass rod, cut to the proper size, bent with a pliers and then the ends crushed to flatten them. They are a pain to make, but look pretty much exactly like the real thing.
The tool holders themselves are from the royal models kit, and are FAR superior to the eduard ones. For one, they are the right thickness and have the right peripheral holes, as well as the right axe holder. That being said, this is another area where soldering skills come in VERY handy, and a photoetch bender is essential.


Moving back to the rear of the cab, I corrected something that I’ve never seen anyone else bother with.

On the back of the cab of some dragon wagons are two toolboxes. If these are added as per the Tamiya instructions, one is flat against the back of the cab is one is angled down are per the angle of the back of the cab. This is entirely incorrect. These toolboxes were mounted in holders welded to a backing plate, which in turn was welded to the back of the cab so the toolboxes are both vertical. I scratchbuilt this out of scrap brass.
Another point of note is the tow bar you can see mounted on the rear of the cab. This is molded by Tamiya with the rotating bottom part with the gap sideways, which is the way it should be while towing. But when mounted to the back of the cab there is a bottom bracket, completely missing in the Tamiya kit, which lines up with this slot and means the tow bar can only be hung with that bottom part with the slit facing directly out from the rear of the cab.
I’m not sure if this sounds confusing or not, so here’s an image from a walkaround showing the bracket.


I also added the tons of tiny chains that hold on the shackles, as well as some scratchbuilt dummy airline ends hanging from chains. These were made out of strip styrene, cut and drilled to shape.


The rest of the detail additions went pretty smoothly. Since I didn’t want to risk getting sanding dust into my newly finished interior, I added the armored covers to the openings and taped them down with Tamiya tape, as well as covering the roof opening.
Most of the detailing here came from the royal Models photoetch set, with only the oxygen and acetelyene straps and the sledge hammer holders coming from the Eduard exterior detail set.
The oxygen and acetelyene straps are one area where Eduard really got it right. They are perfectly sized, easy to fold, and even partially operational (operational but very delicate). Royal models just added a little handle to the molded on Tamiya straps.
All of the little tie-downs on the roof and for the tools are tiny pieces of 0.030 brass rod, cut to the proper size, bent with a pliers and then the ends crushed to flatten them. They are a pain to make, but look pretty much exactly like the real thing.
The tool holders themselves are from the royal models kit, and are FAR superior to the eduard ones. For one, they are the right thickness and have the right peripheral holes, as well as the right axe holder. That being said, this is another area where soldering skills come in VERY handy, and a photoetch bender is essential.


Moving back to the rear of the cab, I corrected something that I’ve never seen anyone else bother with.

On the back of the cab of some dragon wagons are two toolboxes. If these are added as per the Tamiya instructions, one is flat against the back of the cab is one is angled down are per the angle of the back of the cab. This is entirely incorrect. These toolboxes were mounted in holders welded to a backing plate, which in turn was welded to the back of the cab so the toolboxes are both vertical. I scratchbuilt this out of scrap brass.
Another point of note is the tow bar you can see mounted on the rear of the cab. This is molded by Tamiya with the rotating bottom part with the gap sideways, which is the way it should be while towing. But when mounted to the back of the cab there is a bottom bracket, completely missing in the Tamiya kit, which lines up with this slot and means the tow bar can only be hung with that bottom part with the slit facing directly out from the rear of the cab.
I’m not sure if this sounds confusing or not, so here’s an image from a walkaround showing the bracket.


I also added the tons of tiny chains that hold on the shackles, as well as some scratchbuilt dummy airline ends hanging from chains. These were made out of strip styrene, cut and drilled to shape.


didgeboy

Joined: September 21, 2010
KitMaker: 1,846 posts
Armorama: 1,509 posts

Posted: Friday, March 14, 2014 - 09:24 AM UTC
Continues to impress. Wow. just wow.

JLModels

Joined: February 15, 2014
KitMaker: 117 posts
Armorama: 117 posts
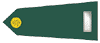
Posted: Friday, March 14, 2014 - 09:27 AM UTC
Damon,
Thanks. I freely admit I may have gone a little overboard on this... just a bit
Thanks. I freely admit I may have gone a little overboard on this... just a bit

Posted: Friday, March 14, 2014 - 01:38 PM UTC
F.Y.I. The tow bar you are talking about is called a "whiffle tree". They have been around in one form or another since the horse and buggy days. Cheers

JLModels

Joined: February 15, 2014
KitMaker: 117 posts
Armorama: 117 posts
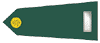
Posted: Friday, March 14, 2014 - 02:21 PM UTC
Michael,
Cool! I guess ya learn something new every day, right?
Cool! I guess ya learn something new every day, right?

Posted: Friday, March 14, 2014 - 03:15 PM UTC
Whiffletrees on a four horse hitch:

(Photo Richard New Forest - Wikepedia)

(Photo Richard New Forest - Wikepedia)
Posted: Friday, March 14, 2014 - 03:18 PM UTC
I would love to see more about how you made those dummy airline couplings. I need them for my Mack! Very impressive!

JLModels

Joined: February 15, 2014
KitMaker: 117 posts
Armorama: 117 posts
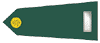
Posted: Friday, March 14, 2014 - 03:53 PM UTC
Michael,
Ask and you shall receive!
I scratch built mine out of some 0.10 x 0.30 evergreen strip based off of this image from the Dragon Wagon technical manual.

I hope this helps!
Ask and you shall receive!
I scratch built mine out of some 0.10 x 0.30 evergreen strip based off of this image from the Dragon Wagon technical manual.

I hope this helps!

Posted: Saturday, March 15, 2014 - 04:10 PM UTC
Would still like to see some close ups of the dummy couplings you made if possible.
Posted: Saturday, March 15, 2014 - 04:11 PM UTC
![]() |