Hosted by Darren Baker
AFV Club AF35135 Churchill Mk.III
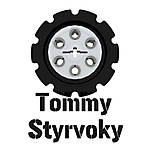
jmsbd07

Joined: April 11, 2014
KitMaker: 96 posts
Armorama: 94 posts

Posted: Thursday, May 22, 2014 - 01:33 AM UTC
Thanks I was wondering about how to make small stuff from scratch, because I'm working on a scratch interrior for my tiger I's turret.
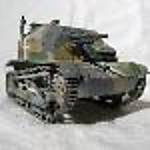
AFVFan

Joined: May 17, 2012
KitMaker: 1,980 posts
Armorama: 1,571 posts

Posted: Thursday, May 22, 2014 - 02:21 AM UTC
Truly amazing work there Mike!
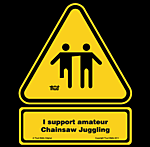
Thudius

Joined: October 22, 2012
KitMaker: 1,194 posts
Armorama: 1,077 posts
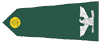
Posted: Thursday, May 22, 2014 - 03:52 AM UTC
Cracking stuff Mike. I love going old school with styrene given half a chance. Hopefully this will help modelers better understand the concept of breaking down stuff into manageable parts. You can get overwhelmed thinking about the sum total, yet adding a piece here and there makes the task fairly straightforward. In essence, the same thing we do when assembling a kit.
Kimmo
Kimmo

SdAufKla

Joined: May 07, 2010
KitMaker: 2,238 posts
Armorama: 2,158 posts

Posted: Thursday, May 22, 2014 - 12:13 PM UTC
@ Tommy: You're very welcome. Don't hesitate to ask any other questions.
@ Bob: Thank you, sir! Looking forward to catching up with you guys in Fayetteville in August for your AMPS show.
@ Kimmo: Very kind of you.
I've been following your Marmon-Herrington armored car build (very nice!) and have noticed that you've offered much the same advice as you've explained and described adding the interior framing.
That's a good analogy - Taking these glued-up sub-assemblies and working them into final shape is very similar to taking a regular kit piece that has a lot of flash, etc, and cleaning away all the bits that don't look like the desired final part. Then putting them together into more complicated components is just the same as gluing smaller parts of a regular kit together.
Thanks for checking in!
Happy modeling!
@ Bob: Thank you, sir! Looking forward to catching up with you guys in Fayetteville in August for your AMPS show.
@ Kimmo: Very kind of you.
Quoted Text
... Hopefully this will help modelers better understand the concept of breaking down stuff into manageable parts. You can get overwhelmed thinking about the sum total, yet adding a piece here and there makes the task fairly straightforward. In essence, the same thing we do when assembling a kit. ...
I've been following your Marmon-Herrington armored car build (very nice!) and have noticed that you've offered much the same advice as you've explained and described adding the interior framing.
That's a good analogy - Taking these glued-up sub-assemblies and working them into final shape is very similar to taking a regular kit piece that has a lot of flash, etc, and cleaning away all the bits that don't look like the desired final part. Then putting them together into more complicated components is just the same as gluing smaller parts of a regular kit together.
Thanks for checking in!
Happy modeling!
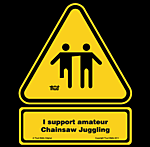
Thudius

Joined: October 22, 2012
KitMaker: 1,194 posts
Armorama: 1,077 posts
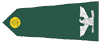
Posted: Friday, May 23, 2014 - 03:22 AM UTC
And thank you for the kind words.
Kimmo
Kimmo
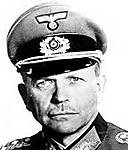
Blackstoat

Joined: October 15, 2012
KitMaker: 568 posts
Armorama: 561 posts

Posted: Friday, May 23, 2014 - 05:18 AM UTC
Nice job bud
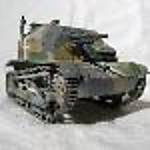
AFVFan

Joined: May 17, 2012
KitMaker: 1,980 posts
Armorama: 1,571 posts

Posted: Friday, May 23, 2014 - 04:01 PM UTC
Quoted Text
@ Bob: Thank you, sir! Looking forward to catching up with you guys in Fayetteville in August for your AMPS show.
That'll be great. Of course, that gives you plenty of time to have this one done by then.


gastec

Joined: February 03, 2014
KitMaker: 1,042 posts
Armorama: 871 posts
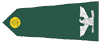
Posted: Friday, May 23, 2014 - 04:26 PM UTC
Mike
I'm a huge fan not only of the Churchill (especially the 'Funnies'), but the AFV kits too and have to say you're doing a splendid job.
Looking forward to the next instalment.
Gary
I'm a huge fan not only of the Churchill (especially the 'Funnies'), but the AFV kits too and have to say you're doing a splendid job.
Looking forward to the next instalment.
Gary

SdAufKla

Joined: May 07, 2010
KitMaker: 2,238 posts
Armorama: 2,158 posts

Posted: Saturday, May 24, 2014 - 10:17 AM UTC
@ Kimmo: You're welcome; it was well deserved!
@ Andy: Cheers!
@ Bob: Oh yea, Bob, you KNOW that's gonna happen!
I'm shooting for next year's AMPS convention, but even that might be cutting it close...
@ Gary: Thank you! And here is the next installment...
So, not too much today. I've been away for the last week on holiday with my extended family (aunts, uncles, cousins, nieces and nephews...). Needless to say, no model building.
However, I did manage to leave a couple of glued up basic sub-assemblies on the ol' work bench for my return, and today, I worked a bit on those.
The current "project within a project within a project" is the release bearing and its actuating mechanisms.
The release bearing, itself, is just a stack of styrene disks, glued together with a hole drilled through to fit it over the input shaft.
Between the gearbox input shaft collar and saddle and the release bearing is a horizontal yoke-like piece and on the ends of its arms are a shaft with crank arms. Two arms push on the release bearing and the third (not shown today) is pushed by the pneumatic clutch actuator.
Here's a photo of the glued up yoke. It's a bit ugly at this stage. You might notice two, side by side shaft bosses. Why two...
Well, I screwed up and glued the first set on the wrong side of the layout line. When I realized my mistake, I just added more on the correct side of the line knowing that the excess would be cut away later.

Here are two of the actuator arms (the ones that push on the bearing). One is ready for test fit with its shaft hole and end rounded, and the other shows you how the glue up looked before these shaping operations (drilling the hole and rounding the end).

In this photo, the yoke has been shaped and the holes for the shaft drilled into the ends of its arms. A piece of .025" dia styrene rod has been passed through these holes and the holes on the arms.

At this stage, the yoke, shaft and arms are all dry fit together and test fitted on the face of the gearbox input shaft collar and saddle. Note that I've left the actuator arms long and will mark them to be cut for length at this test fit stage.
Everything lined up, and I cut the actuator arms to length, rounded their ends and added the bolt heads.
In this photo, the yoke has been glued to the collar-saddle and the actuator arms have been glued to the release bearing. The shaft and arms are still only press fitted to the yoke, but at this stage, I will let the arms and release bearing dry over night.

The entire collar-saddle / release bearing and yoke assembly will then slip on and off the input shaft. This way, when I do the final assembly, I can slide the collar on, then the spring, and then the release bearing. The spring will be slightly compressed between the collar and release bearing and give a good fit. More on this later, though...
Next job on the "punch list" will be to make the pneumatic clutch actuator which will go on the flat side of the collar-yoke and by way of a piston, is attached to the third actuator arm on the shaft (still not show yet...).
Happy modeling!
@ Andy: Cheers!

@ Bob: Oh yea, Bob, you KNOW that's gonna happen!

@ Gary: Thank you! And here is the next installment...
So, not too much today. I've been away for the last week on holiday with my extended family (aunts, uncles, cousins, nieces and nephews...). Needless to say, no model building.
However, I did manage to leave a couple of glued up basic sub-assemblies on the ol' work bench for my return, and today, I worked a bit on those.
The current "project within a project within a project" is the release bearing and its actuating mechanisms.
The release bearing, itself, is just a stack of styrene disks, glued together with a hole drilled through to fit it over the input shaft.
Between the gearbox input shaft collar and saddle and the release bearing is a horizontal yoke-like piece and on the ends of its arms are a shaft with crank arms. Two arms push on the release bearing and the third (not shown today) is pushed by the pneumatic clutch actuator.
Here's a photo of the glued up yoke. It's a bit ugly at this stage. You might notice two, side by side shaft bosses. Why two...
Well, I screwed up and glued the first set on the wrong side of the layout line. When I realized my mistake, I just added more on the correct side of the line knowing that the excess would be cut away later.

Here are two of the actuator arms (the ones that push on the bearing). One is ready for test fit with its shaft hole and end rounded, and the other shows you how the glue up looked before these shaping operations (drilling the hole and rounding the end).

In this photo, the yoke has been shaped and the holes for the shaft drilled into the ends of its arms. A piece of .025" dia styrene rod has been passed through these holes and the holes on the arms.

At this stage, the yoke, shaft and arms are all dry fit together and test fitted on the face of the gearbox input shaft collar and saddle. Note that I've left the actuator arms long and will mark them to be cut for length at this test fit stage.
Everything lined up, and I cut the actuator arms to length, rounded their ends and added the bolt heads.
In this photo, the yoke has been glued to the collar-saddle and the actuator arms have been glued to the release bearing. The shaft and arms are still only press fitted to the yoke, but at this stage, I will let the arms and release bearing dry over night.

The entire collar-saddle / release bearing and yoke assembly will then slip on and off the input shaft. This way, when I do the final assembly, I can slide the collar on, then the spring, and then the release bearing. The spring will be slightly compressed between the collar and release bearing and give a good fit. More on this later, though...
Next job on the "punch list" will be to make the pneumatic clutch actuator which will go on the flat side of the collar-yoke and by way of a piston, is attached to the third actuator arm on the shaft (still not show yet...).
Happy modeling!

Keef1648

Joined: January 23, 2008
KitMaker: 1,240 posts
Armorama: 1,192 posts

Posted: Sunday, May 25, 2014 - 01:24 AM UTC
Glad to hear your vacation didn't cause any model withdrawal symptoms
This build is riveting (pardon the pun) and gets better by each installment. looking forward to seeing more
Keith.

This build is riveting (pardon the pun) and gets better by each installment. looking forward to seeing more
Keith.


SdAufKla

Joined: May 07, 2010
KitMaker: 2,238 posts
Armorama: 2,158 posts

Posted: Tuesday, May 27, 2014 - 10:15 AM UTC
@ Keith: Riveting!? Bad-da bing... ba-da bomm!
So, I'll spare you guys the most ugly details and raggedy glue-ups and just show where I'm at right now.
Here are a couple of shots of the gearbox details coming together in a test fit.



I've made the boxes that run across the top of the gearbox for the "speed change mechanism" (i.e. the gear shifter). The three rods and clevises will get some more work to shorten them some and thin the clevises more so that they will all be parallel to each other.
The "speed change levers" that angle down from the rods in these photos are not the levers that I will actually use. These ones are put together to have a fixture or gage to adjust the rods and get the fulcrum clevis in the correct location and angle. Once the rods and fulcrum clevis have been sorted out, I'll make a new set of levers which will have to be measured to the correct overall length to reach the floor speed change rods from the driver's compartment.
I took a break from the pneumatic clutch actuator while I went to go get some more styrene strip stock. (I ran out of half-round in the size required for the basic glue-up.) Got that today, so I can get back to the actuator when ever I'm ready.
The clutch actuator cranks and levers are still just dry fit onto the input shaft for convenience. The entire unit will simply slip off the shaft right now.
Also, I thought the lift rings that I was using were a bit "anemic" and too small. They were commercial castings from either Grant Line or the Tichy Train Group (I forget which), but just too small. So, using .5 mm diameter brass wire, I soldered up three new lift rings that look more proportional in size to the reference photos I'm working from.
So, lots of little bits and pieces. I know this was a very brief up-date, so if anyone has any questions, don't hesitate to ask.
Happy modeling!

So, I'll spare you guys the most ugly details and raggedy glue-ups and just show where I'm at right now.
Here are a couple of shots of the gearbox details coming together in a test fit.



I've made the boxes that run across the top of the gearbox for the "speed change mechanism" (i.e. the gear shifter). The three rods and clevises will get some more work to shorten them some and thin the clevises more so that they will all be parallel to each other.
The "speed change levers" that angle down from the rods in these photos are not the levers that I will actually use. These ones are put together to have a fixture or gage to adjust the rods and get the fulcrum clevis in the correct location and angle. Once the rods and fulcrum clevis have been sorted out, I'll make a new set of levers which will have to be measured to the correct overall length to reach the floor speed change rods from the driver's compartment.
I took a break from the pneumatic clutch actuator while I went to go get some more styrene strip stock. (I ran out of half-round in the size required for the basic glue-up.) Got that today, so I can get back to the actuator when ever I'm ready.
The clutch actuator cranks and levers are still just dry fit onto the input shaft for convenience. The entire unit will simply slip off the shaft right now.
Also, I thought the lift rings that I was using were a bit "anemic" and too small. They were commercial castings from either Grant Line or the Tichy Train Group (I forget which), but just too small. So, using .5 mm diameter brass wire, I soldered up three new lift rings that look more proportional in size to the reference photos I'm working from.
So, lots of little bits and pieces. I know this was a very brief up-date, so if anyone has any questions, don't hesitate to ask.
Happy modeling!
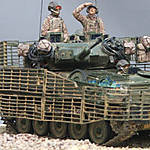
Kallisti

Joined: July 17, 2012
KitMaker: 111 posts
Armorama: 107 posts

Posted: Tuesday, May 27, 2014 - 11:01 AM UTC
Beautiful bit of modelling!
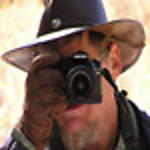
JimF

Joined: July 05, 2002
KitMaker: 717 posts
Armorama: 621 posts
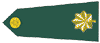
Posted: Tuesday, May 27, 2014 - 04:08 PM UTC
I am a big fan of your build logs and articles, and this is one of the best ones yet. I would have posted earlier, but I just now found and read this one.


SdAufKla

Joined: May 07, 2010
KitMaker: 2,238 posts
Armorama: 2,158 posts

Posted: Thursday, May 29, 2014 - 11:20 AM UTC
@ Andrew: Thank you, sir!
@ Jim: I'm glad you found the blog and have had look.
I have a lot of stuff planned for this build, above and beyond this gearbox stuff. This is just the beginning, really. I have a lot of Voyager PE to add and another pretty significant scratch-building job, not to mention figures and a motorcycle, so keep checking in.
So, on to the build...
Not much time at the work bench over the last few days. However, I have made a bit of progress on the speed change levers and rods.
This might not look like much, but I was surprised at how hard it was to get the levers and rods lined up. In the end, I had to glue down the rods and clevises on the floor to eliminate at least one of the moving parts.
After cutting each lever to length (test fitting as I went), I glued each lever to the speed change rods and then the rods to the gearbox. I had to do these one at a time. Because the space inside the gearbox compartment is so small, I actually had trouble seeing down to the floor past the top of the gearbox, and this made lining up each lever into its floor clevis while matching it with the gearbox rod clevis a lot more difficult than I anticipated.
In the end, though, I got it done. Here are some photos of the speed change levers and rods. Because the space is small and relatively deep, the camera had some depth of field issues, so please forgive the focus issues. I couldn't get a good, in focus picture of both ends of the levers and had to shift back and forth between the floor and the top of the gearbox.




There's still a yoke which serves as a fulcrum for the levers that will go on the front corner of the gearbox. I have it glued up, but I can't mount it until these parts have dried and I can match the yoke to the angle of the levers.
The entire speed change mechanism on the gearbox, to include the rods, levers and boxes will be a single subassembly when it comes to finishing and final assembly.
That's all for now.
Happy modeling!
@ Jim: I'm glad you found the blog and have had look.
I have a lot of stuff planned for this build, above and beyond this gearbox stuff. This is just the beginning, really. I have a lot of Voyager PE to add and another pretty significant scratch-building job, not to mention figures and a motorcycle, so keep checking in.
So, on to the build...
Not much time at the work bench over the last few days. However, I have made a bit of progress on the speed change levers and rods.
This might not look like much, but I was surprised at how hard it was to get the levers and rods lined up. In the end, I had to glue down the rods and clevises on the floor to eliminate at least one of the moving parts.
After cutting each lever to length (test fitting as I went), I glued each lever to the speed change rods and then the rods to the gearbox. I had to do these one at a time. Because the space inside the gearbox compartment is so small, I actually had trouble seeing down to the floor past the top of the gearbox, and this made lining up each lever into its floor clevis while matching it with the gearbox rod clevis a lot more difficult than I anticipated.
In the end, though, I got it done. Here are some photos of the speed change levers and rods. Because the space is small and relatively deep, the camera had some depth of field issues, so please forgive the focus issues. I couldn't get a good, in focus picture of both ends of the levers and had to shift back and forth between the floor and the top of the gearbox.




There's still a yoke which serves as a fulcrum for the levers that will go on the front corner of the gearbox. I have it glued up, but I can't mount it until these parts have dried and I can match the yoke to the angle of the levers.
The entire speed change mechanism on the gearbox, to include the rods, levers and boxes will be a single subassembly when it comes to finishing and final assembly.
That's all for now.
Happy modeling!

Keef1648

Joined: January 23, 2008
KitMaker: 1,240 posts
Armorama: 1,192 posts

Posted: Thursday, May 29, 2014 - 11:59 PM UTC
Well this portion of your build is no 'yoke'
Mike, an amazing amount of detail. One half expects it to start up!
Keep the updates coming!
Keith.

Keep the updates coming!
Keith.


easyco69

Joined: November 03, 2012
KitMaker: 2,275 posts
Armorama: 2,233 posts
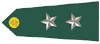
Posted: Friday, May 30, 2014 - 12:11 AM UTC
Nice work!
I built the AFV Club Mk IV , was a great kit.
I built the AFV Club Mk IV , was a great kit.

SdAufKla

Joined: May 07, 2010
KitMaker: 2,238 posts
Armorama: 2,158 posts

Posted: Saturday, May 31, 2014 - 10:58 AM UTC
@ Keith: It's no "yoking matter" at all!
@ David: Thank you! The AFV Club Churchill kits are very nice, indeed.
Details, details, details...
So, I've been switching between several detail assemblies, working on one while another was drying, etc.
I've added the fulcrum yoke to the speed change levers. This is glued to the levers, but not to the front of the gearbox allowing the entire speed change lever, rod and box assembly to remain separate for now.
I've also finished the pneumatic clutch actuator assembly. Again, this part, along with the input shaft collar and saddle remain separate for now.
While waiting on bits and pieces for those two details to dry, I've worked on the speedometer drive wheel. This is sheave or pulley that's driven by a belt that runs around another sheave on the left / port side muff coupling between the two brake drums. The speedometer drive wheel is mounted on an arm that's tensioned by a coil spring and the cable to the speedometer runs from a connection at the hub of the drive wheel.
Here're a couple of pics of the almost completed drive wheel and bracket.


Still to be added is a piece of angle stock extending from the front bottom corner of the triangular bracket that holds the forward end of the tensioning spring. The rear end of this spring is attached to the wheel axle at its hub.
Here's the speedometer drive wheel test fitted on the left / port hull side wall.

And a couple more with the gearbox in place to measure the width of the speedometer drive wheel assembly to fit it between the two brake drums.



The turret traverse motor generator will fit on the hull floor just inboard of the speedometer drive wheel and is itself driven by a belt that runs from the pulley on the input shaft on the front of the gearbox.
I've made the speedometer drive wheel swing arm, wheel hub and axles from brass so that they will resist the force of the drive belt and not twist when I install everything.
So, with the addition of the speed change levers and the clutch actuator mechanism, the gearbox is almost complete.



Still to go are the two muff couplings between the brake drums on either side. Once those are made, I will permanently add the steering brake drums and the couplings and trim the stub axles that are holding the rear of the gearbox in alignment with the main brakes.
If all works as planned, the rear of the gearbox will rest correctly on the rear mounts with the front held in correct alignment by the fan and input shaft. I'll then make the front gearbox mount to fit the space under the input collar-saddle and the floor.
My plan is to make the gearbox totally removable so that I can paint and finish it separately from the inside of the compartment, then install the gearbox during final assembly (in the far distant and murky future...).
Happy modeling!

@ David: Thank you! The AFV Club Churchill kits are very nice, indeed.
Details, details, details...
So, I've been switching between several detail assemblies, working on one while another was drying, etc.
I've added the fulcrum yoke to the speed change levers. This is glued to the levers, but not to the front of the gearbox allowing the entire speed change lever, rod and box assembly to remain separate for now.
I've also finished the pneumatic clutch actuator assembly. Again, this part, along with the input shaft collar and saddle remain separate for now.
While waiting on bits and pieces for those two details to dry, I've worked on the speedometer drive wheel. This is sheave or pulley that's driven by a belt that runs around another sheave on the left / port side muff coupling between the two brake drums. The speedometer drive wheel is mounted on an arm that's tensioned by a coil spring and the cable to the speedometer runs from a connection at the hub of the drive wheel.
Here're a couple of pics of the almost completed drive wheel and bracket.


Still to be added is a piece of angle stock extending from the front bottom corner of the triangular bracket that holds the forward end of the tensioning spring. The rear end of this spring is attached to the wheel axle at its hub.
Here's the speedometer drive wheel test fitted on the left / port hull side wall.

And a couple more with the gearbox in place to measure the width of the speedometer drive wheel assembly to fit it between the two brake drums.



The turret traverse motor generator will fit on the hull floor just inboard of the speedometer drive wheel and is itself driven by a belt that runs from the pulley on the input shaft on the front of the gearbox.
I've made the speedometer drive wheel swing arm, wheel hub and axles from brass so that they will resist the force of the drive belt and not twist when I install everything.
So, with the addition of the speed change levers and the clutch actuator mechanism, the gearbox is almost complete.



Still to go are the two muff couplings between the brake drums on either side. Once those are made, I will permanently add the steering brake drums and the couplings and trim the stub axles that are holding the rear of the gearbox in alignment with the main brakes.
If all works as planned, the rear of the gearbox will rest correctly on the rear mounts with the front held in correct alignment by the fan and input shaft. I'll then make the front gearbox mount to fit the space under the input collar-saddle and the floor.
My plan is to make the gearbox totally removable so that I can paint and finish it separately from the inside of the compartment, then install the gearbox during final assembly (in the far distant and murky future...).
Happy modeling!
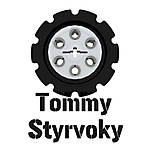
jmsbd07

Joined: April 11, 2014
KitMaker: 96 posts
Armorama: 94 posts

Posted: Saturday, May 31, 2014 - 05:17 PM UTC
So with the transmission, is just layered streme and then was shaped to proper shape ?
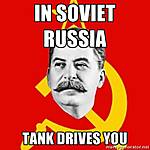
Tiger_213

Joined: August 10, 2012
KitMaker: 1,510 posts
Armorama: 1,443 posts

Posted: Saturday, May 31, 2014 - 07:02 PM UTC
It looks so damn clean! Keep at it, Mike.


SdAufKla

Joined: May 07, 2010
KitMaker: 2,238 posts
Armorama: 2,158 posts

Posted: Sunday, June 01, 2014 - 07:13 AM UTC
@ Christopher: Thanks! The challenge and satisfaction is when you're done, hopefully there's a seamless transition between the scratch-built work and the kit. If no one notices the difference between my work and the kit maker's, then I'll be a happy camper!
@ Tommy:
That's pretty much it in a nut shell. I used layered styrene sheet glued together and after the glue dried, shaped by carving, sanding and filing. It helps to break seemingly complicated components down into a conglomeration of basic shapes. Build each shape, bring the shapes together, and then add the details.
Here are a couple of collages of photos of the various general steps in the process to make the gearbox.


I studied my reference photos and materials and took some dimensions from the kit and drew up some working sketches of the basic gearbox shape. I left off the details and concentrated on the basic dimensions (to fit the space in the kit) and the overall shape.
These working drawings don't have to be works of mechanical art.
I used the end view dimensions divided by the thickness of my styrene sheet to determine the number of layers I had to cut out. The shapes were pretty much all the same and very similar to the shape of the "flange" part in the second picture.
You'll note the comment in the third picture where I had to go back and add a filler strip in the notch along the front of the very top styrene layer. I used filler putty as necessary to get these top and bottom shapes smooth.
I also did a lot of test fitting to make sure that my estimated dimensions would fit the space and continuously compared my basic shape to my reference photos.
Once I was satisfied, I began to add the details. First up were the ribs and flanges. To get the flanges to fit nicely and to be spaced evenly, I inserted them into slots cut into the basic shape using a miter box and saw. These flanges, just wide styrene strips, were glued in place and shaped. I again use filler putty to blend them into the over all gearbox shape.
After that, I added the details, starting with enhancing the cast texture with thinned filler putty brushed on, then the nuts and bolts (punched out of styrene sheet using punch and die sets), and finally adding the larger details (input shaft collar-saddle, air compressor, and speed change mechanism) which were made as subassemblies.
The work is slow, but when taken as individual bits and pieces, not particularly hard. If you can accurately layout the cut lines and then cut a single styrene part to shape, then this is really just repetitiously doing that same task many times. Once you reduce assemblies down to their basic shapes, you'll find the reproducing those shapes is usually pretty straightforward work.
The only special tools that are necessary are good measuring and layout tools. I use a dial caliper to take measurements and some good metal rulers and squares and triangles for layout. I generally use an X-acto knife to scribe most layout lines rather than a pencil since the lines are much more precise. A parallel cutter (like a compass with small blades on either leg - one blade replaced with a compass point) is very useful for cutting circles and large holes. I do all my measuring and layout work using metric dimensions as the math is easier and I'm less prone to make mistakes (just a personal preference).
I use the "score and snap" method to cut out most parts. Once styrene parts are cut out, they should be cleaned up by sanding to get the snapped edges straight and eliminate the ridges left on either side of the cut lines.
HTH and happy modeling!
@ Tommy:
Quoted Text
So with the transmission, is just layered streme and then was shaped to proper shape ?
That's pretty much it in a nut shell. I used layered styrene sheet glued together and after the glue dried, shaped by carving, sanding and filing. It helps to break seemingly complicated components down into a conglomeration of basic shapes. Build each shape, bring the shapes together, and then add the details.
Here are a couple of collages of photos of the various general steps in the process to make the gearbox.


I studied my reference photos and materials and took some dimensions from the kit and drew up some working sketches of the basic gearbox shape. I left off the details and concentrated on the basic dimensions (to fit the space in the kit) and the overall shape.
These working drawings don't have to be works of mechanical art.
I used the end view dimensions divided by the thickness of my styrene sheet to determine the number of layers I had to cut out. The shapes were pretty much all the same and very similar to the shape of the "flange" part in the second picture.
You'll note the comment in the third picture where I had to go back and add a filler strip in the notch along the front of the very top styrene layer. I used filler putty as necessary to get these top and bottom shapes smooth.
I also did a lot of test fitting to make sure that my estimated dimensions would fit the space and continuously compared my basic shape to my reference photos.
Once I was satisfied, I began to add the details. First up were the ribs and flanges. To get the flanges to fit nicely and to be spaced evenly, I inserted them into slots cut into the basic shape using a miter box and saw. These flanges, just wide styrene strips, were glued in place and shaped. I again use filler putty to blend them into the over all gearbox shape.
After that, I added the details, starting with enhancing the cast texture with thinned filler putty brushed on, then the nuts and bolts (punched out of styrene sheet using punch and die sets), and finally adding the larger details (input shaft collar-saddle, air compressor, and speed change mechanism) which were made as subassemblies.
The work is slow, but when taken as individual bits and pieces, not particularly hard. If you can accurately layout the cut lines and then cut a single styrene part to shape, then this is really just repetitiously doing that same task many times. Once you reduce assemblies down to their basic shapes, you'll find the reproducing those shapes is usually pretty straightforward work.
The only special tools that are necessary are good measuring and layout tools. I use a dial caliper to take measurements and some good metal rulers and squares and triangles for layout. I generally use an X-acto knife to scribe most layout lines rather than a pencil since the lines are much more precise. A parallel cutter (like a compass with small blades on either leg - one blade replaced with a compass point) is very useful for cutting circles and large holes. I do all my measuring and layout work using metric dimensions as the math is easier and I'm less prone to make mistakes (just a personal preference).
I use the "score and snap" method to cut out most parts. Once styrene parts are cut out, they should be cleaned up by sanding to get the snapped edges straight and eliminate the ridges left on either side of the cut lines.
HTH and happy modeling!
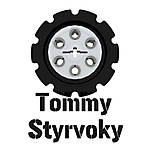
jmsbd07

Joined: April 11, 2014
KitMaker: 96 posts
Armorama: 94 posts

Posted: Monday, June 02, 2014 - 02:27 PM UTC
Thanks again, I have a dividers that I use to cut circles,the points are sharpened. Also with the shaping of the transmission, did you just make a solid block of streme then cut it to desired shape or made indivisual layers and cemented them ?

SdAufKla

Joined: May 07, 2010
KitMaker: 2,238 posts
Armorama: 2,158 posts

Posted: Tuesday, June 03, 2014 - 02:00 AM UTC
@ Tommy:
You can actually do it either way or combine the two approaches.
If you glue a bunch of styrene layers together to make a solid block, you'll need to transfer your top, side and end profiles to the block as references.
Alternatively, you can cut each layer to the approximate size, glue them together and then shape them. Using this method, you would transfer your end profile (or at least one of the other profiles) to the glue-up to have those reference lines for shaping.
(You'll note in many of the photos of my gearbox the scribed centerline of the output shafts is still visible. When I started shaping it, I also had a perpendicular line to mark the location of the input shaft. At one time, I also had the end profiles laid out, too.)
Or, you can glue up a basic block shape and then add some more refined layers to that. This is actually the approach I used with my gearbox because the final shape has some complex bumps and dips as well as a more regular cylindrical portion.
I cut the middle layers more or less the same dimensions, but the layers where there were bumps and bulges got a more "custom" treatment to help establish the final detail shapes. The center layers that formed the equatorial flanges were cut very close to their final shapes and added between the top and bottom basic halves later.
Here's a quick diagram of the basic technique showing the top half of a cylinder with a flange around its bottom.

This could be done as a solid rectangular block or, as shown here, as a series of graduated layers.
Note that you need to cut the layers slightly oversized so that their edges stand proud of the final, desired profile in order to have enough material to shape to an accurate dimension. If you don't do this, you'll wind up with a part that's undersized.
You take your two basic dimensions from the two different views - The top view will give you the true length, and the end view will give you the true widths.
The number of layers that you need to glue together to make a basic block large enough can be calculated by dividing the thickness of the profile by the thickness of the sheet plastic.
Finally, as you glue up the layers, give them plenty of time to dry hard. I usually leave these glue-ups to dry at least over night. This will help with both strength and shrinkage. The hard dry glue-up will be strong enough to handle and shape and the spaces between the layers will not shrink as the glue continues to dry.
HTH and happy modeling!
Quoted Text
... Also with the shaping of the transmission, did you just make a solid block of streme then cut it to desired shape or made indivisual layers and cemented them ?
You can actually do it either way or combine the two approaches.
If you glue a bunch of styrene layers together to make a solid block, you'll need to transfer your top, side and end profiles to the block as references.
Alternatively, you can cut each layer to the approximate size, glue them together and then shape them. Using this method, you would transfer your end profile (or at least one of the other profiles) to the glue-up to have those reference lines for shaping.
(You'll note in many of the photos of my gearbox the scribed centerline of the output shafts is still visible. When I started shaping it, I also had a perpendicular line to mark the location of the input shaft. At one time, I also had the end profiles laid out, too.)
Or, you can glue up a basic block shape and then add some more refined layers to that. This is actually the approach I used with my gearbox because the final shape has some complex bumps and dips as well as a more regular cylindrical portion.
I cut the middle layers more or less the same dimensions, but the layers where there were bumps and bulges got a more "custom" treatment to help establish the final detail shapes. The center layers that formed the equatorial flanges were cut very close to their final shapes and added between the top and bottom basic halves later.
Here's a quick diagram of the basic technique showing the top half of a cylinder with a flange around its bottom.

This could be done as a solid rectangular block or, as shown here, as a series of graduated layers.
Note that you need to cut the layers slightly oversized so that their edges stand proud of the final, desired profile in order to have enough material to shape to an accurate dimension. If you don't do this, you'll wind up with a part that's undersized.
You take your two basic dimensions from the two different views - The top view will give you the true length, and the end view will give you the true widths.
The number of layers that you need to glue together to make a basic block large enough can be calculated by dividing the thickness of the profile by the thickness of the sheet plastic.
Finally, as you glue up the layers, give them plenty of time to dry hard. I usually leave these glue-ups to dry at least over night. This will help with both strength and shrinkage. The hard dry glue-up will be strong enough to handle and shape and the spaces between the layers will not shrink as the glue continues to dry.
HTH and happy modeling!

SdAufKla

Joined: May 07, 2010
KitMaker: 2,238 posts
Armorama: 2,158 posts

Posted: Thursday, June 05, 2014 - 12:43 PM UTC
The latest up-date:
I've finished the speedometer drive wheel assembly.

This was also the time to add the framing and rivets to the hull interior.

I still have to do some more work on the framing in the rear corners, so there are some filler pieces and putty that are drying in those areas.
The round headed rivets are Grant Line #153.
The inverted V-shaped front gearbox mount is not finished on its top since that part of it will not be visible once the compartment is finished.
I've also added the muff couplings to the steering brake drums, trimmed the stub axles to length, and glued the couplings and drums to the gearbox. There are two pneumatic lines to add to the insides of the steering brake drums.


The gearbox assembly as seen in these photos will slip into and out of the compartment for later finishing.
With the speedo drive wheel assembly and left / port side muff coupling completed, I can do some detailed test fitting to check the alignment of the drive wheel and the center pulley on the coupling. In this photo, I've used a piece of straightened brass wire to test the alignment of these parts. When finished, there will be a drive belt running around the coupling and speedo drive wheel.

The speedo drive wheel is only temporarily attached in this photo with a small dab of contact cement.
Lastly, another test fit of all the components to check the alignment of the shifter levers and other parts now that the rear of the gearbox sits on its rear hull mounts, held in the center of the compartment by the couplings between the steering and main brake drums.

Next up will probably be the turret motor generator and its mount followed by the compressed air reservoir cylinder.
Happy modeling!
I've finished the speedometer drive wheel assembly.

This was also the time to add the framing and rivets to the hull interior.

I still have to do some more work on the framing in the rear corners, so there are some filler pieces and putty that are drying in those areas.
The round headed rivets are Grant Line #153.
The inverted V-shaped front gearbox mount is not finished on its top since that part of it will not be visible once the compartment is finished.
I've also added the muff couplings to the steering brake drums, trimmed the stub axles to length, and glued the couplings and drums to the gearbox. There are two pneumatic lines to add to the insides of the steering brake drums.


The gearbox assembly as seen in these photos will slip into and out of the compartment for later finishing.
With the speedo drive wheel assembly and left / port side muff coupling completed, I can do some detailed test fitting to check the alignment of the drive wheel and the center pulley on the coupling. In this photo, I've used a piece of straightened brass wire to test the alignment of these parts. When finished, there will be a drive belt running around the coupling and speedo drive wheel.

The speedo drive wheel is only temporarily attached in this photo with a small dab of contact cement.
Lastly, another test fit of all the components to check the alignment of the shifter levers and other parts now that the rear of the gearbox sits on its rear hull mounts, held in the center of the compartment by the couplings between the steering and main brake drums.

Next up will probably be the turret motor generator and its mount followed by the compressed air reservoir cylinder.
Happy modeling!
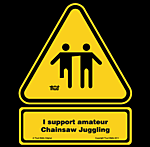
Thudius

Joined: October 22, 2012
KitMaker: 1,194 posts
Armorama: 1,077 posts
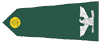
Posted: Thursday, June 05, 2014 - 10:27 PM UTC
Sweet.
Kimmo
Kimmo

Keef1648

Joined: January 23, 2008
KitMaker: 1,240 posts
Armorama: 1,192 posts

Posted: Friday, June 06, 2014 - 12:01 AM UTC
Quoted Text
The latest up-date:
Next up will probably be the turret motor generator and its mount followed by the compressed air reservoir cylinder.
Happy modeling!
What do you mean by 'probably' of course it will be, how can it not be? seems logical to me

The detail is amazing and I am loving this build, another winner for sure

Keith.

![]() |