The kit I chose was the AFVclub pak40, which had good reviews on PMMS, as well as ammo and crews available to really take it over the top. The thing that really pushed it over the top for me was that Verlinden just came out with a resin diorama base for it, which would let me concentrate on building the gun and crew, and not worry as much about the base.
So I purchased the kit, and then… kinda went nuts.
One of the glorious and terrifying things about modeling these days is the glut of information available on almost any subject. After just a couple of days of searching I found six walk arounds and 4 books on the Pak40, as well as videos, hundreds of historical photos, etc.
And then I found just how much aftermarket this gun has! Every photoetch manufacturer and their uncle seems to have a pak40 etch set or two. I’ve lost count of how many replacement barrels are available. That’s not including the K59 resin update set which effectively replaces the entire kit gun above the trailing arms!
Historically I’ve had the most success with Aber photoetch, so I chose their ‘Basic’ set and their ‘gun shield’ set. For crew I went for Warrior’s SS pak 40 crew #1 and 2, and as mentioned before, the verlinden base.
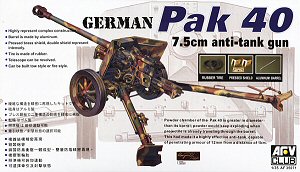
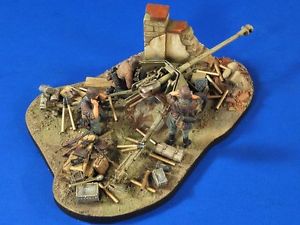
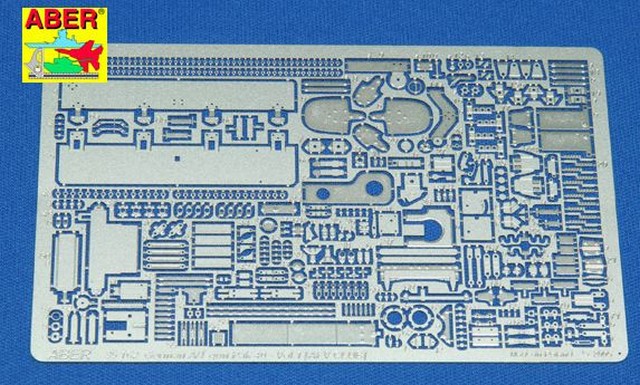
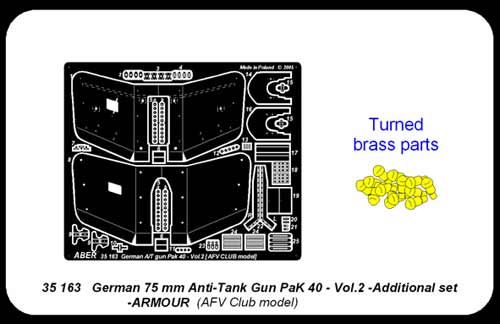
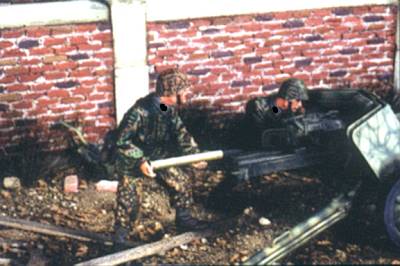
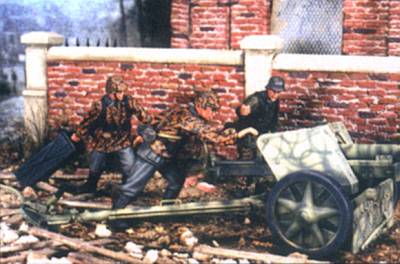
Finally, mostly because I’d read really good things about K59’s resin stuff, I also picked up their Pak40 update set.
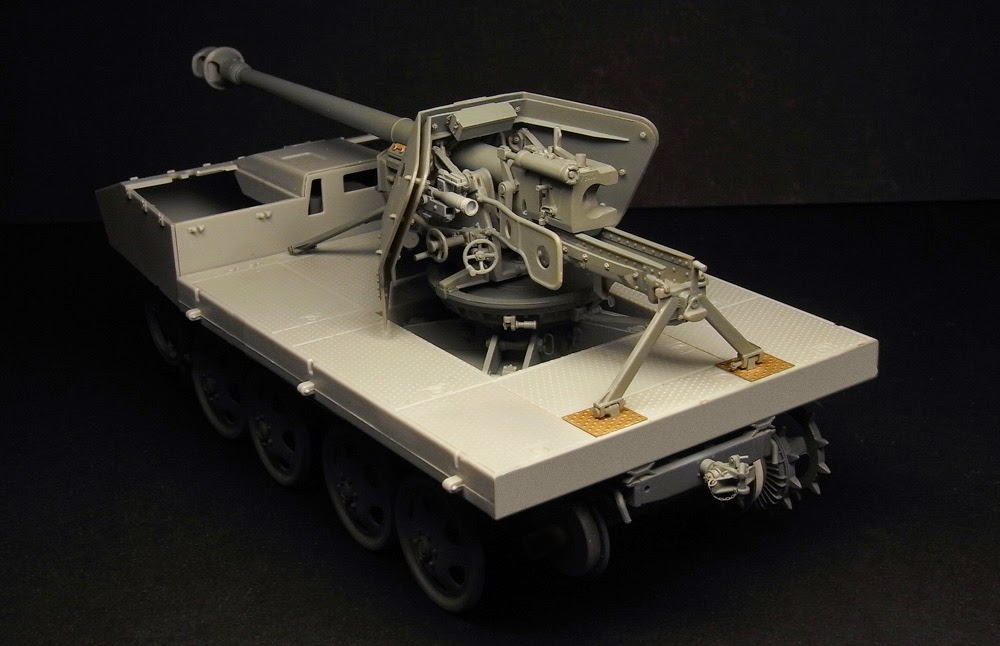
Yes, all of this for one small artillery piece. In the end I think I’m actually only using about 25% of the AFVclub kit. As I said, I’m nuts.

So, with that out of the way, lets get to building!
I began with the trailing arms, which went together fairly nicely. The pak 40 had a lot of production variations, especially in terms of wheels, muzzle breaks, and electrical and pneumatic braking. The AFVclub kit including the pneumatic brakes, air tank, and the connectors on the right trailing arm, which I installed. If you want to simplify construction so you don’t need to do all of the air line plumbing you can leave these parts off and fill their locator holes.
As usual for me, rather than bother removing the mold seams and ensuring roundness of the grab handles, I simply replaced them with brass rod. The gun barrel cleaning rods were also replaced with evergreen plastic rod in the aber mounts.
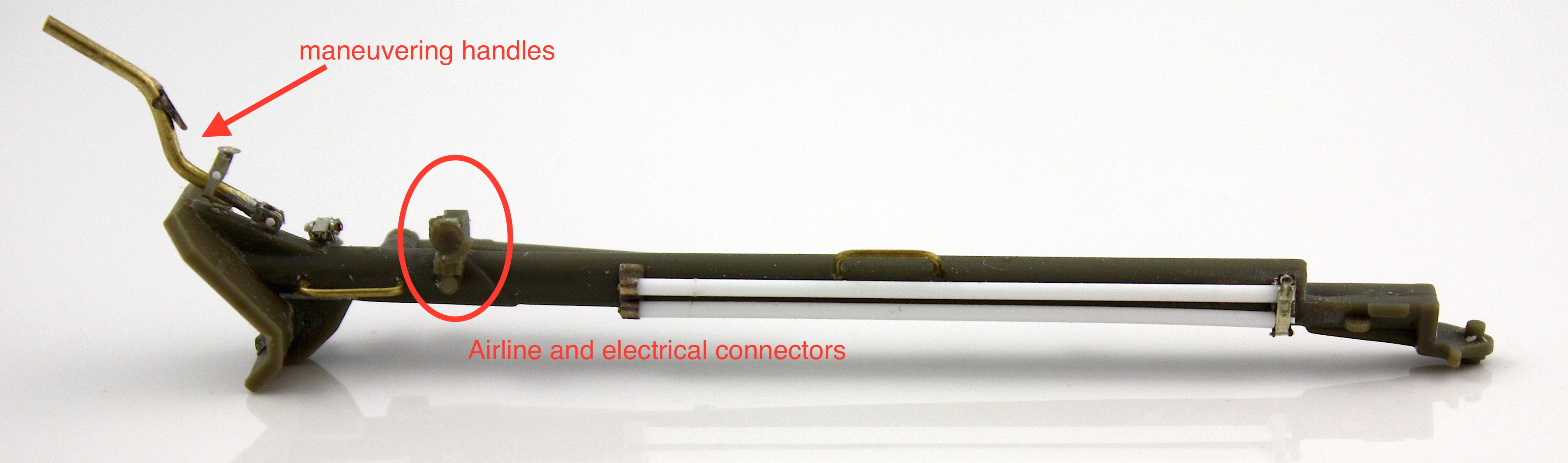
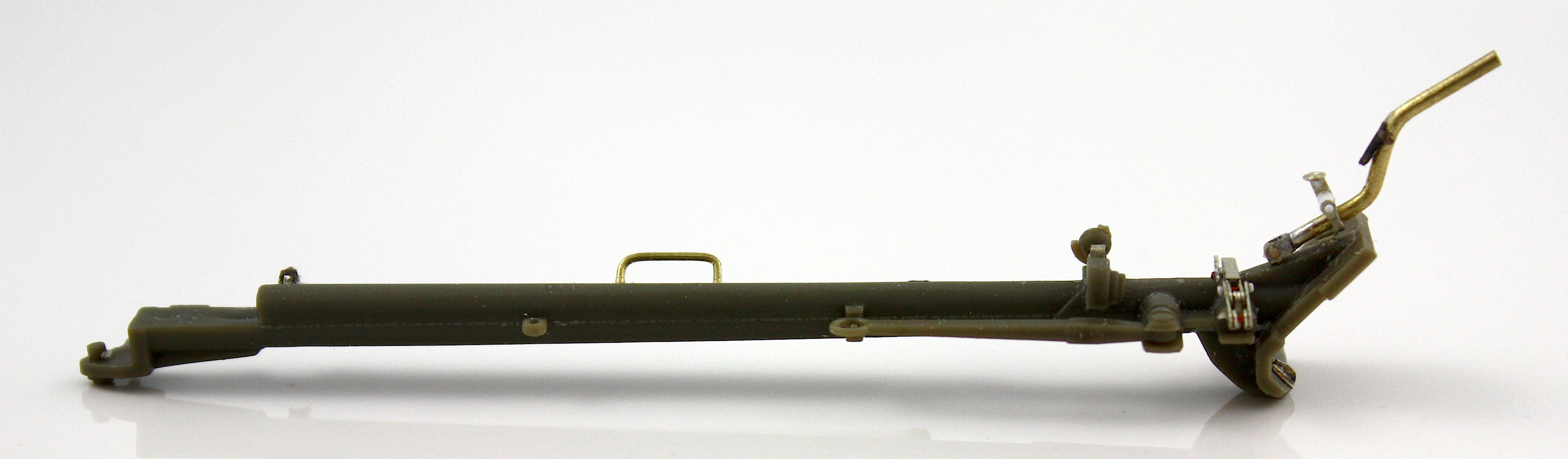
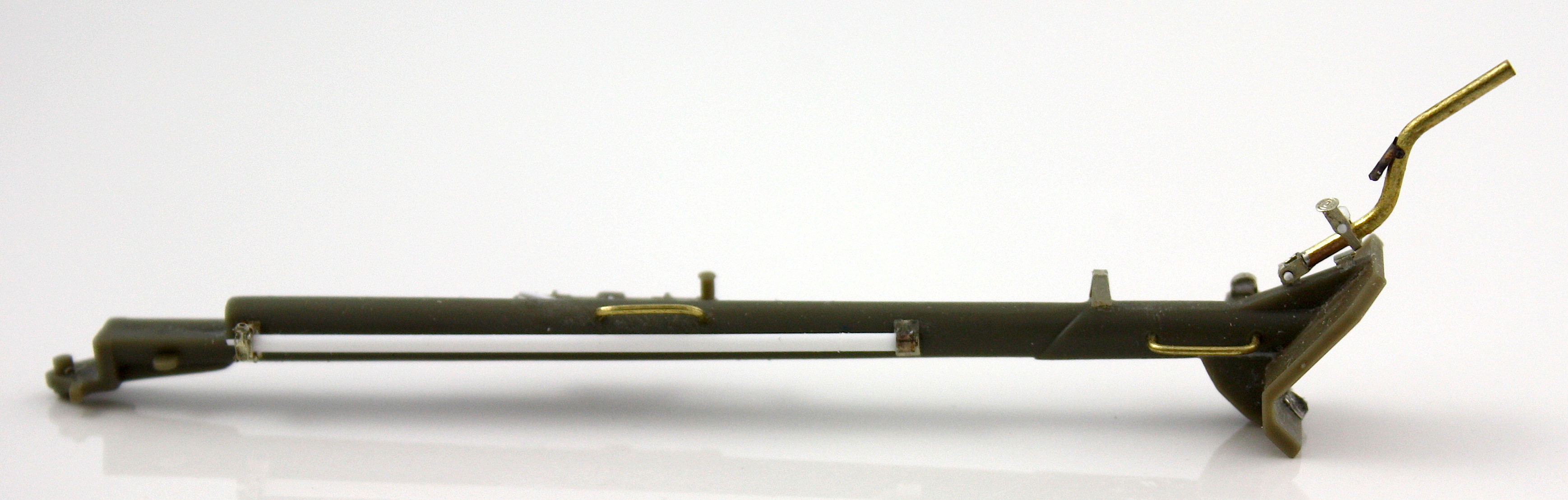
The biggest job here was to replace the folding rear trailing arm maneuvering handles with brass rod and photoetch from the aber set. It all goes together really well, but I HIGHLY recommend soldering these. They are delicate and you’ll probably knock them off a dozen times during construction and finishing if you superglue them instead.
In fact, as a note, this build relies a LOT on soldering. If you want to practice your soldering skills, the Aber pak 40 sets, especially the gun shield is a great place to do so. I actually wound up buying a butane soldering torch to supplement my soldering iron in order to get everything together.
The trailing arm locking brace that connects the two arms together in the center when in travel mode was also detailed as per various walk arounds and book photos. I’ve seen two different styles of handles on this, a straight bar and an angled one. I went with the straight one as it’s more common in historical photos.
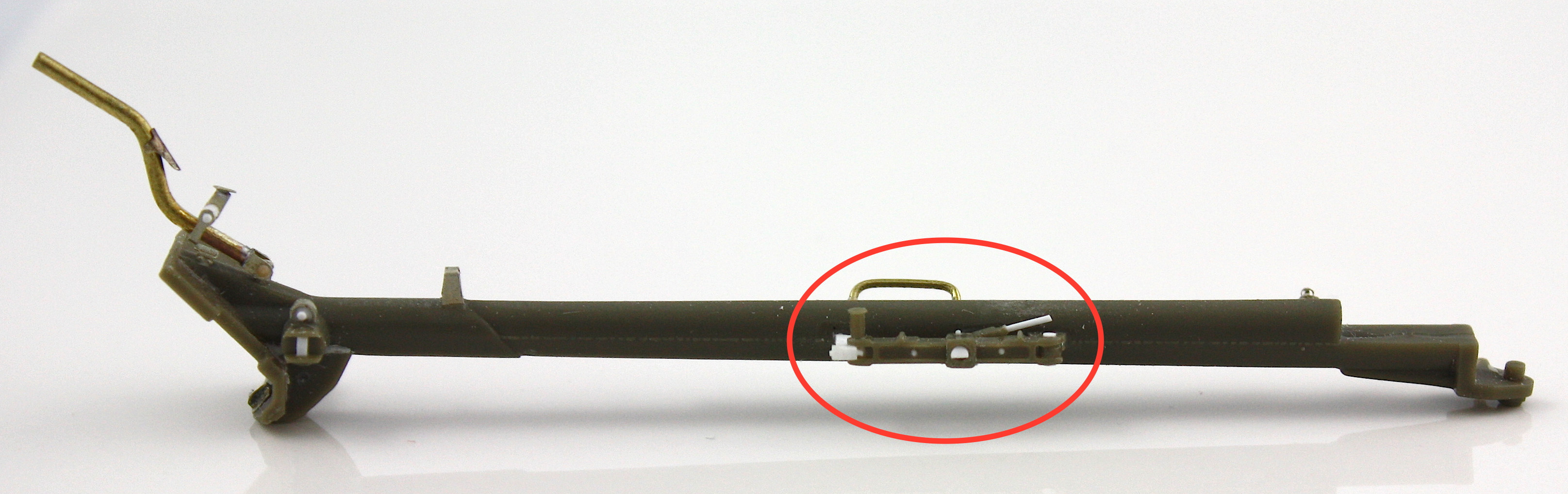
Next it was on to the gun mount base. Here I had some issues with the AFVclub kit. I’m pretty sure I followed the directions correctly, but I got to a point where attaching one of the wheel mount arms in the correct orientation was impossible because the mount points are keyed (a half-circle shaped pin goes into a half-circle shaped hole) but if I put together like that one of the wheel mounts was always upside down. I checked all of the part and part numbers, and every time I assembled it the kit wound up like that. In the end I just opened up the half-circular hole and flipped the part over, and everything matched up with references and such, but it was still surprising.
Small bits of photoetch and wire were added here for the gun mount stops and oiling points.
I’m going to be honest here, the AFVclub pak40 base has several unusual accuracy and molding issues related to the two ‘handles’ and rods which lock the axles in place for firing. First off, the kit includes two versions of these handles, one for use when the gun is traveling, and one for firing. The firing handles are angled outwards and their ends lock into mounts on the axle bump stops, while the travel ones are straight and don’t lock into these, enabling the axle suspension to travel.
Here’s a list of the issues in the AFVclub kit related to that:
1) The firing handles, because they’re angled, can’t be molded correctly on a two part mold. AFVclub has thus compromised and molded the handle slanted like a parallelogram. But in reality a rectangular handle doesn’t suddenly become a parallelogram when its hinge moves. This means it’s easier to cut off the properly formed handles on the straight part and angle them than trying to fix the angled ones.
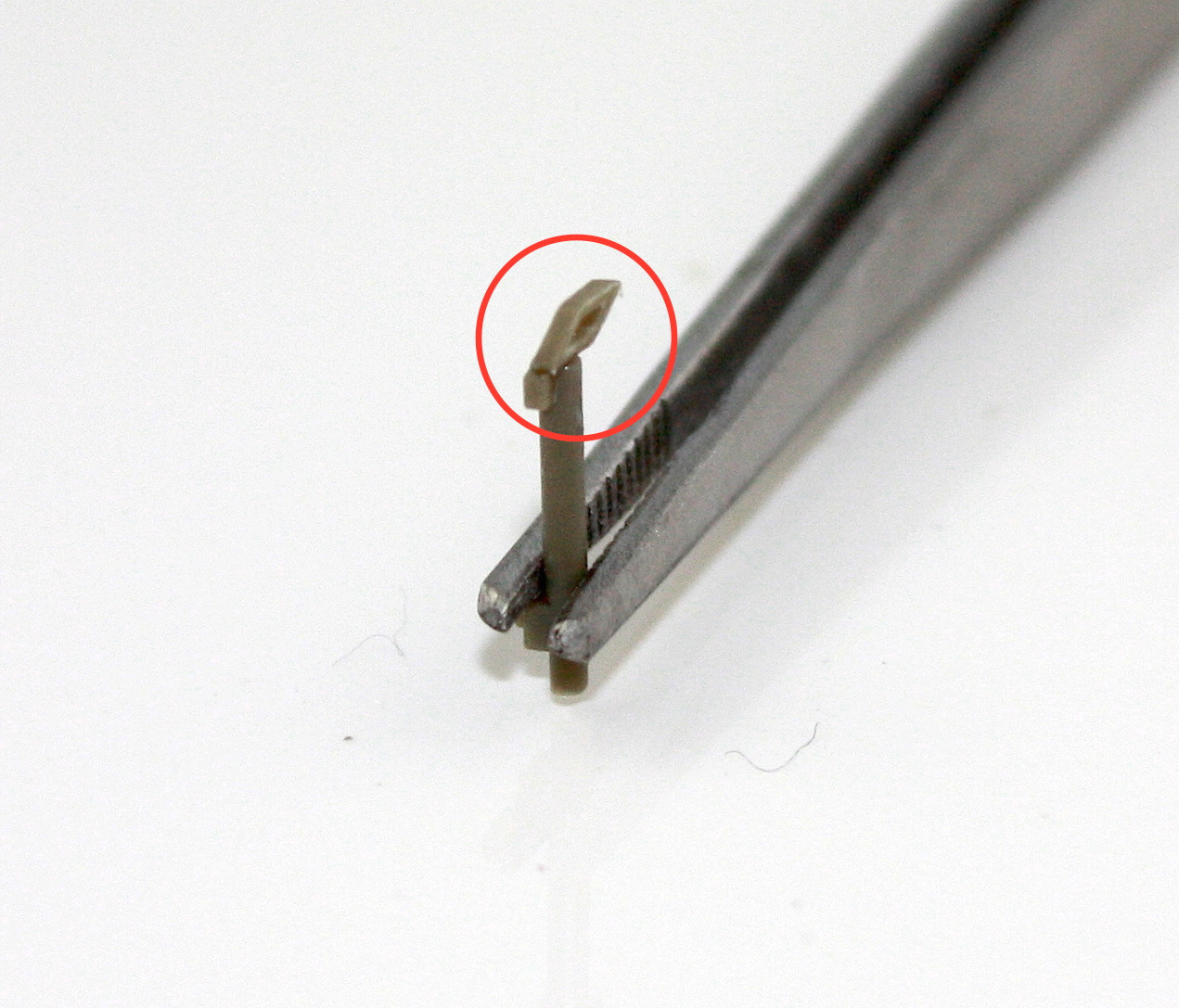
2) The top of the axle bump stop is reinforced by two triangular reinforcing plates, which are molded solid in the kit and not replaced in the aber etch set. These need to be hollowed out.
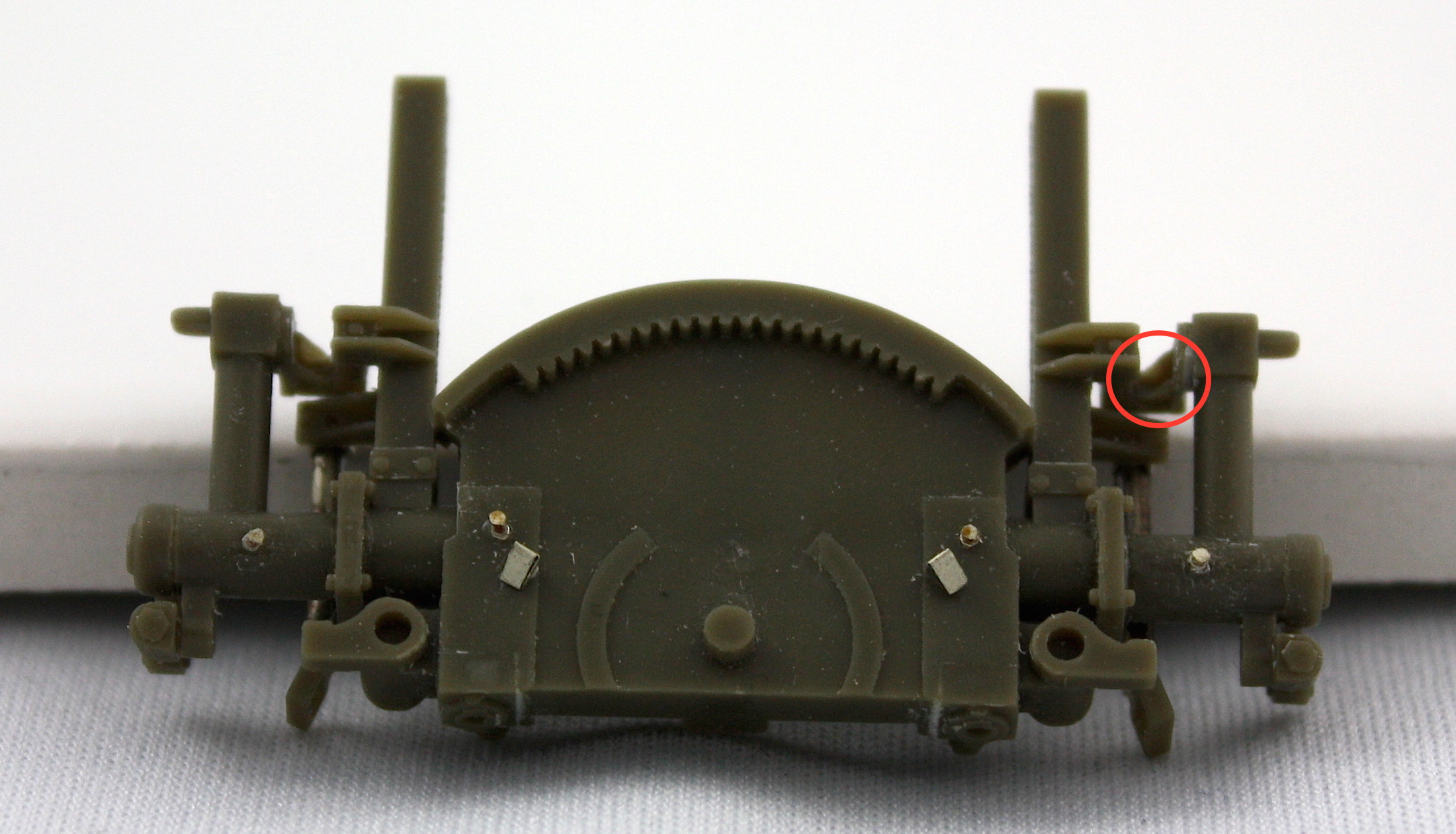
3) The bump stops don’t actually line up with each other. The ones on the gun platform are fine, but the one on each axle are supposed to be at an angle. AFVclub has molded these as pointing straight down, which means that if the suspension were compressed then only 1/3rd of the bump stop on the axle would contact the upper bump stop on the carriage.
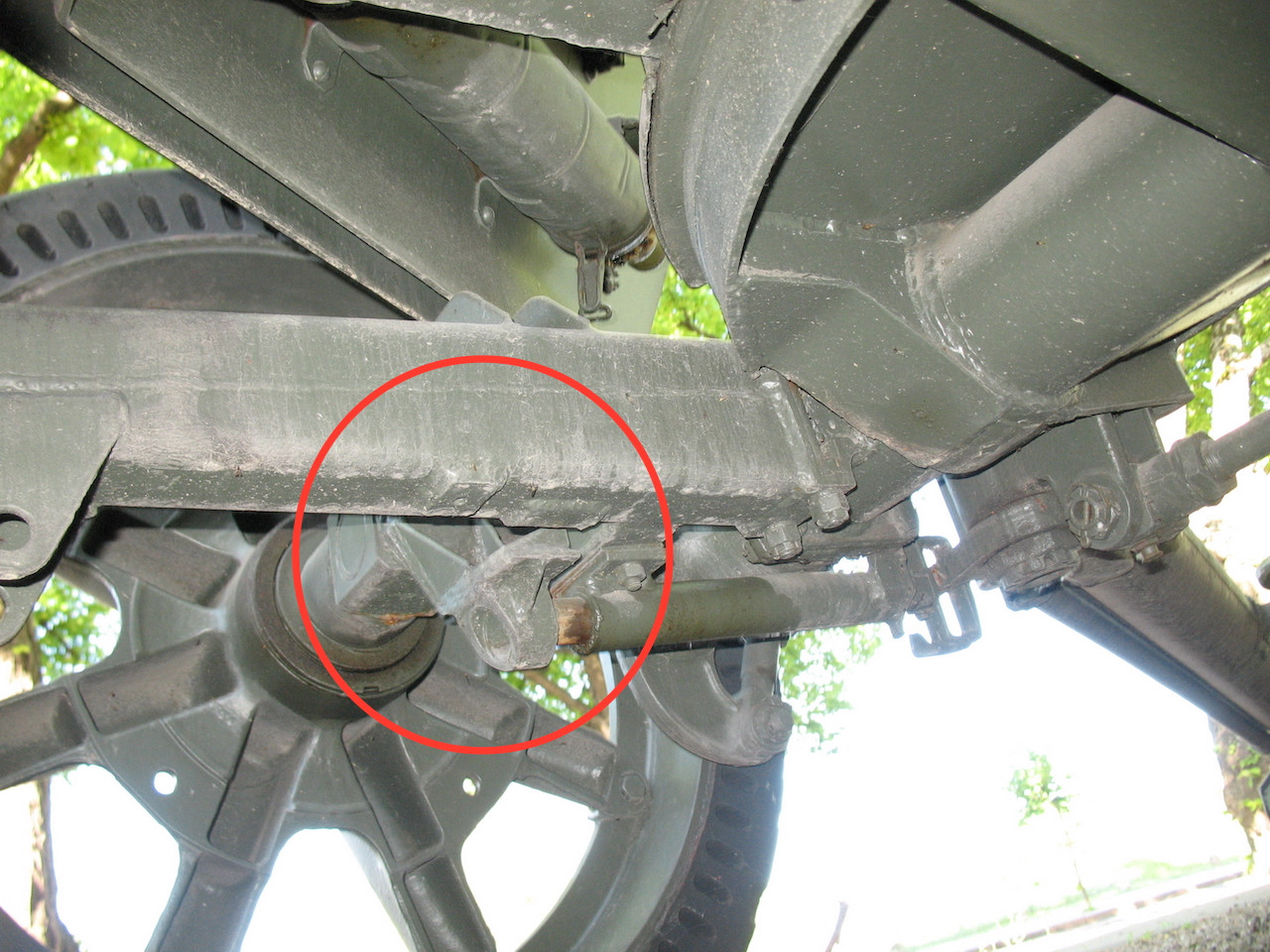
4) When you correct that by cutting off the axle bump stop and repositioning it, you move the locking area that the end of the rod meets up with, meaning that needs to be cut off and glued back on.
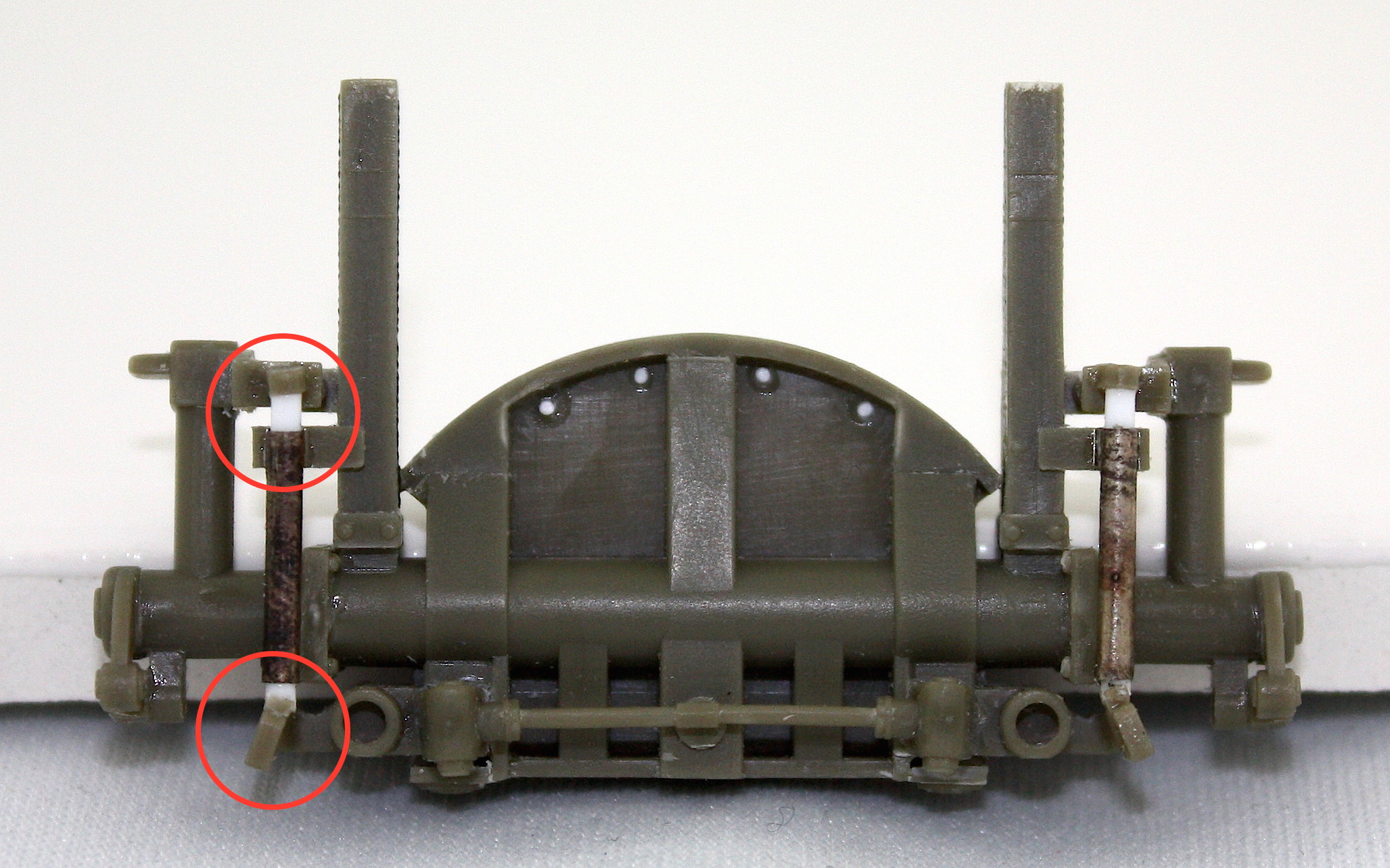
I chose to do all of this for accuracy’s sake, but will admit that when finished, unless you know what you’re looking for, most people won’t notice this, not the four missing bolts on the underside of the gun carriage.
Next up, we get crazy with the lower gun shields. Watch as 5 kit parts become 113 photoetched ones!