Anyone who has seen some of my previous work (Russian MAZ 8x8's) knows that I am a stickler for having fairly correct and complete underbody and driveline detail.
After seeing the job the Italeri designers did on the HEMTT driveline it leaves me wondering if any of the design engineers ever actually laid eyes on a HEMTT driveline?
At least in the case of the Italeri M1120 model the driveline would functionally work (unlike some other kits I have dealt with!) It just would not work for very long and the Italeri kit clearly fails to match the reality of the vehicle in a number of major ways.
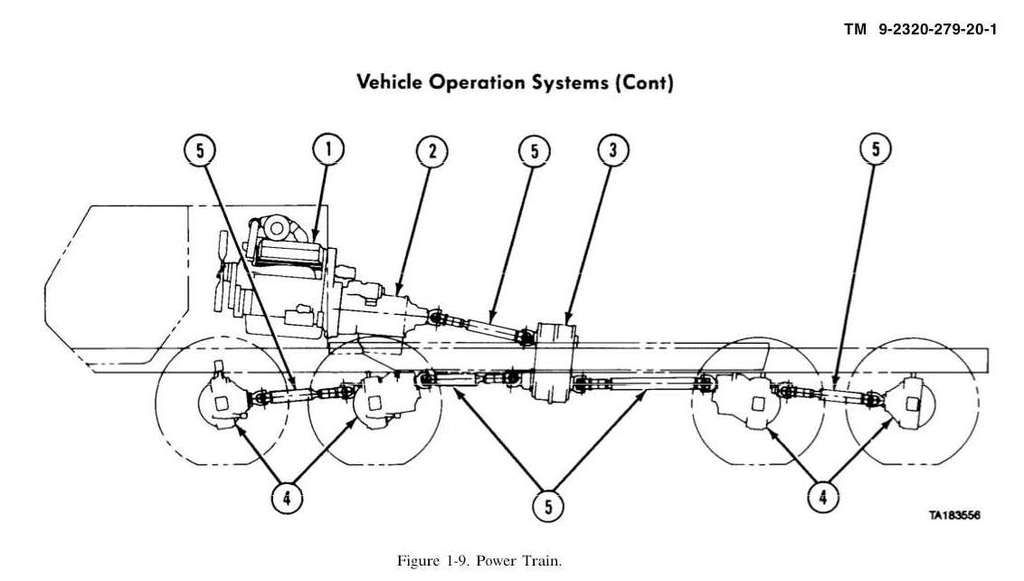
Please note in the TM drawing above; the engine and transmission are inclined and not sitting flat square as Italeri's undetailed, ugly block of cheese engine would have the model builder think. Additionally the transfer case and all four differentials are also slightly inclined.
What's this all about?Universal joints work best, last longer and can carry more stress when the angle of axis bend
(don't know what else to call it) is kept as small as possible. Clearly Oshkosh has tried to minimize the angle of bend on all the driveline universals to maximize the vehicle strength, endurance and dependability. To my mind this is a fact that the Italeri design engineers decided to intentionally overlook, I guess because zero degree and 90 degree angles are just that much easier to lay out on their CAD design drawings.
This is simply laziness on the part of the model manufacturer at the expense of greater accuracy in the model. It would not have cost the company that much more in initial design hours to do it correctly in the first place and would have cost literally nothing in additional manufacturing expense!
I'm sorry but if I owned the company there would be a design manager somewhere that would be out of his fancy office and back out on the floor doing basic CAD scut work tomorrow!