It's worth repeating that this has to be the most detail per square inch I've ever seen in a marketed kit and of course,it doesn't hurt that one of the best modelers I've ever known is building it as well. The fidelity in scale is amazing.
J
Hosted by Darren Baker
Riich Models RV35011

jrutman

Joined: April 10, 2011
KitMaker: 7,941 posts
Armorama: 7,934 posts

Posted: Friday, October 04, 2013 - 01:55 AM UTC
Posted: Friday, October 04, 2013 - 02:19 AM UTC
Hi Mike,
Excellent progress, looking terrific. The level of detail is wonderful.
Class work.
Cheers
Al
Excellent progress, looking terrific. The level of detail is wonderful.
Class work.
Cheers
Al




SdAufKla

Joined: May 07, 2010
KitMaker: 2,238 posts
Armorama: 2,158 posts

Posted: Friday, October 04, 2013 - 03:21 AM UTC
@ Jerry and Alan:
Thank you both for your kind comments about my build, but Riich Models really deserves a ton of credit for bringing this kit out with the level and fidelity of detail that's included. A 5 or 600 part kit of a subject that's only 4 inches long and 2-1/4 inches wide must represent a huge investment in money and time as well as a great marketing risk for any company.
Riich deserves full credit for listening to and giving their customers what they asked for.
In particular, two individuals were instrumental in getting the kit and its details correct and accurate:
At Riich Models, Mr. Kurtis Tsang ensured that the kit was designed correctly from the start and was willing to put the time, effort and money into making that so.
However, another individual, Mr. George Moore was the guy who did significant "heavy lifting" with providing much of the research and other technical information that Riich needed in order to produce this little jewel.
Mr. Moore is also the individual who mastered the Resicast carrier kits and conversions, and you can find his personal website here:
Moore's Military Models
I just thought that these guys' names deserve to be mentioned here. While I was researching my carrier build, I learned that Mr. Tsang and Mr. Moore were the two guys who had such personal involvement in bringing the Riich Models Universal Carrier to light. I don't have any connection with either of these folks, but I am one singularly impressed model builder and feel that credit should be given where its due.
It's not often that we know who's responsible for the many of the kits that we enjoy building, so for anyone looking at the Riich Universal Carrier kit, now you know who deserves much of the credit for it.
Happy modeling!
Thank you both for your kind comments about my build, but Riich Models really deserves a ton of credit for bringing this kit out with the level and fidelity of detail that's included. A 5 or 600 part kit of a subject that's only 4 inches long and 2-1/4 inches wide must represent a huge investment in money and time as well as a great marketing risk for any company.
Riich deserves full credit for listening to and giving their customers what they asked for.
In particular, two individuals were instrumental in getting the kit and its details correct and accurate:
At Riich Models, Mr. Kurtis Tsang ensured that the kit was designed correctly from the start and was willing to put the time, effort and money into making that so.
However, another individual, Mr. George Moore was the guy who did significant "heavy lifting" with providing much of the research and other technical information that Riich needed in order to produce this little jewel.
Mr. Moore is also the individual who mastered the Resicast carrier kits and conversions, and you can find his personal website here:
Moore's Military Models
I just thought that these guys' names deserve to be mentioned here. While I was researching my carrier build, I learned that Mr. Tsang and Mr. Moore were the two guys who had such personal involvement in bringing the Riich Models Universal Carrier to light. I don't have any connection with either of these folks, but I am one singularly impressed model builder and feel that credit should be given where its due.
It's not often that we know who's responsible for the many of the kits that we enjoy building, so for anyone looking at the Riich Universal Carrier kit, now you know who deserves much of the credit for it.
Happy modeling!

dvarettoni

Joined: September 28, 2005
KitMaker: 778 posts
Armorama: 763 posts

Posted: Friday, October 04, 2013 - 03:36 AM UTC
mike out standing you allways make it look so simple can't wait to see this next week!!! hay just started my next build i started MENG's T90a you should check it out
dave
dave



SdAufKla

Joined: May 07, 2010
KitMaker: 2,238 posts
Armorama: 2,158 posts

Posted: Friday, October 04, 2013 - 11:59 AM UTC
@ Dave: Thanks, Dave! I did check out your T-90 and am blown-away by how much progress you've made on it already.
I'm also following it now, so hopefully I won't miss any of your up-dates. I'll be looking forward to seeing it and your BRDM-2 next week!
So, on to a little up-date for today...
Progressing through the unfinished kit steps, I tackled step 42 today. This is where the radio battery box, the POL cans and stowage rack and the (elliptical spring sprung!) rear number plate are constructed.
Doesn't sound like much of a day's work, but this little sub-assembly has 21 parts, four of which are PE. It all goes together par for the course - that is, very nicely.
The only significant challenge is forming the two PE elliptical springs that the rear number plate is mounted to. These certainly give this area of the model that "classic" Universal Carrier look. The number plate appearing to hang suspended in the air is very characteristic, and FWIW, I think Riich has done the subject justice.
I used a .030 dia drill bit to form the two semi-circular bends on the PE spring parts, Pa6 x 2. Keeping these bends equal and the springs the same length is important to getting a good fit on the number plate. I would suggest slightly reaming out the three holes on each PE part that accept the bolts molded on the reverse of the number plate to give you a little "wiggle room" for adjustment. If you need more adjustment, then the molded on bolts can be trimmed around to make them a little smaller in diameter.
I soldered the joins on these parts, too, for added strength, but if they're formed well, they will almost stay closed on their own. CA should work with some care.
I did scratch build the short section of pipe conduit that the electrical wires for the tail light on the number plate. I basically made this the same way as the conduit for the radio power lead.
If I ever build another one of these Riich carriers, I will scavenge the injection molded headlight wiring conduit, part A37, step 30, to make the radio power and tail light conduits. Part A37 is not visible under the upper front hull / glacis, and the parts that are visible, A30 and A56, are all that's really needed there. This would leave A37 available to make visible missing conduits.
Anyways, here are a couple of pictures of the battery box assembly from step 42.




Like I said, IMO, Riich has done this quite well, and the details match available references closely.
Today, I also spent a little time cleaning up the parts (yes, parts -plural!) for step 43. This is where the tow rope is constructed... from 15 parts. That's not a typo: 15 parts.
More on this later, but I have to say that I've never built a kit that had a 15-part tow cable. As you might expect, the Riich kit has very faithfully captured the iconic look and details of this Universal Carrier feature, too.
Happy modeling!
I'm also following it now, so hopefully I won't miss any of your up-dates. I'll be looking forward to seeing it and your BRDM-2 next week!
So, on to a little up-date for today...
Progressing through the unfinished kit steps, I tackled step 42 today. This is where the radio battery box, the POL cans and stowage rack and the (elliptical spring sprung!) rear number plate are constructed.
Doesn't sound like much of a day's work, but this little sub-assembly has 21 parts, four of which are PE. It all goes together par for the course - that is, very nicely.
The only significant challenge is forming the two PE elliptical springs that the rear number plate is mounted to. These certainly give this area of the model that "classic" Universal Carrier look. The number plate appearing to hang suspended in the air is very characteristic, and FWIW, I think Riich has done the subject justice.
I used a .030 dia drill bit to form the two semi-circular bends on the PE spring parts, Pa6 x 2. Keeping these bends equal and the springs the same length is important to getting a good fit on the number plate. I would suggest slightly reaming out the three holes on each PE part that accept the bolts molded on the reverse of the number plate to give you a little "wiggle room" for adjustment. If you need more adjustment, then the molded on bolts can be trimmed around to make them a little smaller in diameter.
I soldered the joins on these parts, too, for added strength, but if they're formed well, they will almost stay closed on their own. CA should work with some care.
I did scratch build the short section of pipe conduit that the electrical wires for the tail light on the number plate. I basically made this the same way as the conduit for the radio power lead.
If I ever build another one of these Riich carriers, I will scavenge the injection molded headlight wiring conduit, part A37, step 30, to make the radio power and tail light conduits. Part A37 is not visible under the upper front hull / glacis, and the parts that are visible, A30 and A56, are all that's really needed there. This would leave A37 available to make visible missing conduits.
Anyways, here are a couple of pictures of the battery box assembly from step 42.




Like I said, IMO, Riich has done this quite well, and the details match available references closely.
Today, I also spent a little time cleaning up the parts (yes, parts -plural!) for step 43. This is where the tow rope is constructed... from 15 parts. That's not a typo: 15 parts.
More on this later, but I have to say that I've never built a kit that had a 15-part tow cable. As you might expect, the Riich kit has very faithfully captured the iconic look and details of this Universal Carrier feature, too.
Happy modeling!

jrutman

Joined: April 10, 2011
KitMaker: 7,941 posts
Armorama: 7,934 posts

Posted: Saturday, October 05, 2013 - 01:30 AM UTC
Man o man. It never ends bubba. How many parts can be left in the box? The tail end stuff looks very tidy and I love the spring mounts under the rear plate and they even provide the handles for the oil cans?
What manner of divination is this? What sorcerer has leant his foul hand to this abomination? Where is the Inquisition when you need them??
Seriously,nice clean job man.
J
What manner of divination is this? What sorcerer has leant his foul hand to this abomination? Where is the Inquisition when you need them??
Seriously,nice clean job man.
J
Posted: Saturday, October 05, 2013 - 01:49 AM UTC
Top of the line modelling Mike. This is the level where I would lay out cash and buy the book for. I really admire your attention to detail, but even more than that, adpating figures to be placed on top of this detail, is magic!! Keep it going mate ... this is a model that will be remembered for some time.


SdAufKla

Joined: May 07, 2010
KitMaker: 2,238 posts
Armorama: 2,158 posts

Posted: Saturday, October 05, 2013 - 09:37 AM UTC
@ Jerry: How many more parts...?!
I don't even know. It must be some special kind of plastic that Riich uses. When you leave the box open overnight, the next day, the parts all seemed to have multiplied!
I just wish the model fairies would pay me a visit. No matter how many cookie crumbs I leave 'em, they never seem to get any work done overnight. Between my lazy model fairies and the self-replicating Riich plastic, I may never finish this build!
@ Frank: I don't know, Frank... I don't think there're any publishers or editors willing to put up with me, so I guess I'll just keep posting away here.
On the bright side, no one can say they're not getting their money's worth!
Well, it's a college football day here, so between battening down the hatches for tropical storm Karen and getting ready for the "BIG GAME" (which I couldn't care less about, but I enjoy the company), not much to show.
Just how much can you say about a 1/35th scale tow rope, anyways?
Surprisingly, more than I thought...
First, Riich gives us 15 parts to assemble the Universal Carrier tow rope - one piece of nylon string, 4 PE split rings, 2 pieces of chain, and 8 injection-molded parts.
After cleaning up the plastic parts, I checked the nylon string against the eyelets only to find that the string is much too large to fit into the slide molded holes. In fact, the string is larger in diameter than the tow-eye ferrules, so even drilling them out is not an option.
This was too bad, as I had planned on the color variation of actual hemp rope vice the typical wire rope. The prototype photo in Riich's instructions shows an original tow rope made of large diameter hemp, and that would have been an nice "vintage" touch to my carrier.
Oh well... Plan B. Checking out all of the tow ropes that I could see clearly in period photos showed that most were made of a thin wire rope anyways, so falling back on my usual techniques, I twisted a new rope from .010 dia lead wire.
These photos also showed that most (if not all) of the small wire ropes had their ferrules (the portion between the rope and eyelet) wrapped in some sort of fabric or paper. So, after cutting my rope to length (57 mm), I added thin copper wire wraps and glued the rope to the kit eyelets. Next I added this wrapped material from thin tissue paper strips.
Since I was going through all that effort, I decided to replace the kit's PE split rings (which lack an appropriate thickness) with rings made from 28 gauge brass wire. I formed this by wrapping the wire around a 1 mm dia drill bit, and then cutting the rings from the resulting coil.
Riich does not specify the length of the rope or chain pieces. I estimated the length for my rope from photos. Studying the instructions, Riich depicts the two chain pieces in two different lengths - one 12 links long and one 15 links. I chose to go with 15 - just because...
All of the shackles and hooks are just press-fit to assemble. The split rings are simply spread apart, the chain and one shackle are threaded on, and split is closed.
Here's the result.



In these pics, I've pre-painted the material wrapped around the ferrules to protect the paper and white glue.
Now, if all of this seems excessive... well, fret not. It seems that carrier crews mixed and matched the tow rope parts according to their own needs and ideas.
Here are three variations in how the rope is configured and carried. Some one could easily simplify Riich's (and the prototype's) "full-Monty" approach and go with several interesting depictions.



Who knew there was so much to something so simple?
Again, to Riich's credit, they did not cut any corners with even the most mundane features of their Universal Carrier.
Now, if I can just get those damn model-fairies to do some work...
I don't even know. It must be some special kind of plastic that Riich uses. When you leave the box open overnight, the next day, the parts all seemed to have multiplied!
I just wish the model fairies would pay me a visit. No matter how many cookie crumbs I leave 'em, they never seem to get any work done overnight. Between my lazy model fairies and the self-replicating Riich plastic, I may never finish this build!
@ Frank: I don't know, Frank... I don't think there're any publishers or editors willing to put up with me, so I guess I'll just keep posting away here.
On the bright side, no one can say they're not getting their money's worth!

Well, it's a college football day here, so between battening down the hatches for tropical storm Karen and getting ready for the "BIG GAME" (which I couldn't care less about, but I enjoy the company), not much to show.
Just how much can you say about a 1/35th scale tow rope, anyways?
Surprisingly, more than I thought...
First, Riich gives us 15 parts to assemble the Universal Carrier tow rope - one piece of nylon string, 4 PE split rings, 2 pieces of chain, and 8 injection-molded parts.
After cleaning up the plastic parts, I checked the nylon string against the eyelets only to find that the string is much too large to fit into the slide molded holes. In fact, the string is larger in diameter than the tow-eye ferrules, so even drilling them out is not an option.
This was too bad, as I had planned on the color variation of actual hemp rope vice the typical wire rope. The prototype photo in Riich's instructions shows an original tow rope made of large diameter hemp, and that would have been an nice "vintage" touch to my carrier.
Oh well... Plan B. Checking out all of the tow ropes that I could see clearly in period photos showed that most were made of a thin wire rope anyways, so falling back on my usual techniques, I twisted a new rope from .010 dia lead wire.
These photos also showed that most (if not all) of the small wire ropes had their ferrules (the portion between the rope and eyelet) wrapped in some sort of fabric or paper. So, after cutting my rope to length (57 mm), I added thin copper wire wraps and glued the rope to the kit eyelets. Next I added this wrapped material from thin tissue paper strips.
Since I was going through all that effort, I decided to replace the kit's PE split rings (which lack an appropriate thickness) with rings made from 28 gauge brass wire. I formed this by wrapping the wire around a 1 mm dia drill bit, and then cutting the rings from the resulting coil.
Riich does not specify the length of the rope or chain pieces. I estimated the length for my rope from photos. Studying the instructions, Riich depicts the two chain pieces in two different lengths - one 12 links long and one 15 links. I chose to go with 15 - just because...
All of the shackles and hooks are just press-fit to assemble. The split rings are simply spread apart, the chain and one shackle are threaded on, and split is closed.
Here's the result.



In these pics, I've pre-painted the material wrapped around the ferrules to protect the paper and white glue.
Now, if all of this seems excessive... well, fret not. It seems that carrier crews mixed and matched the tow rope parts according to their own needs and ideas.
Here are three variations in how the rope is configured and carried. Some one could easily simplify Riich's (and the prototype's) "full-Monty" approach and go with several interesting depictions.



Who knew there was so much to something so simple?
Again, to Riich's credit, they did not cut any corners with even the most mundane features of their Universal Carrier.
Now, if I can just get those damn model-fairies to do some work...
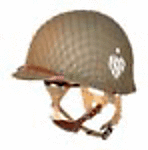
Big-John

Joined: August 12, 2010
KitMaker: 731 posts
Armorama: 711 posts

Posted: Saturday, October 05, 2013 - 09:52 AM UTC
I still get “blown away” every time I read one of your updates Mike. I’m amazed at the level of detail in the kit, and your ability to take it a few steps further.
One highly detailed kit + one master modeler = AWESOME!
One highly detailed kit + one master modeler = AWESOME!
Posted: Saturday, October 05, 2013 - 10:28 PM UTC
Hi Mike,
Excellent progress. Glad to see George getting the credit he deserves for his input to the kit. Riich have certainly rowed the boat out on this kit and your blog will be a great help to anyone undertaking the build.
Frank,
I highly recommend Nigel Watson's Volumnes 1, 2 and 3 on the Universal Carrier, simply a master piece of information. I just got volume 3 and it's another data filled gem.
Cheers
Al
Excellent progress. Glad to see George getting the credit he deserves for his input to the kit. Riich have certainly rowed the boat out on this kit and your blog will be a great help to anyone undertaking the build.
Frank,
I highly recommend Nigel Watson's Volumnes 1, 2 and 3 on the Universal Carrier, simply a master piece of information. I just got volume 3 and it's another data filled gem.
Cheers
Al




Keef1648

Joined: January 23, 2008
KitMaker: 1,240 posts
Armorama: 1,192 posts

Posted: Sunday, October 06, 2013 - 01:00 AM UTC

Mike, as usual, outstanding work and update.
I noticed the conduit and wiring for the number plate light, I hope your going to cut it underneath and insert a/the bulb or is that not included in the kit?
Batteries plus Bulbs on Two Notch Rd may help or even Advance Autos if it isn't included (everything else seems to be).

I am really enjoying this build and anyone who has this as a 'to do' project will have a great reference here.
Keith.


SdAufKla

Joined: May 07, 2010
KitMaker: 2,238 posts
Armorama: 2,158 posts

Posted: Wednesday, October 09, 2013 - 03:42 AM UTC
@ John: Thank you, mi amigo!
@ Alan: George definitely deserves to see his name in public in connection with this kit. The Riich kit certainly falls into the "craftsman" area - definitely not a "shake and bake" or weekend project. But if someone wants an accurate rendition of the Universal Carrier, this is the kit he should tackle. George Moore played a large part in making this true.
@ Keith: I donno, Keith. I'm at the limits of my meager talents as it is. I'm lucky to keep from making gluey finger prints all over. I think installing a light bulb in the number plate is beyond me...
So, only a quick up-date right now. Hopefully some more photos later, but at the moment, here's where the carrier project stands.

This is an initial composition test to check on the relative sizes of the main components of the planned display. The hull front is still just dry-fit pending installation of the driver. The model is really starting to look like a Universal Carrier now, though...
The paper tag with the engine data is a mock up to get a better idea of how large or small that should be. I plan to display the carrier with the engine compartment top off to the side so that the engine details can be seen.
I have some fairly firm ideas for the terrain and other display elements and will show those as I mock them up, too. Right now, I'm just testing various arrangements to get a better idea of how the overall space will work. Smaller is better, but there needs to be space for a couple of other elements needed for visual balance.
In regards to the rest of the build - I've completed all of the construction. There are still a bunch of sub-assemblies and parts that will be finished and installed as the carrier moves towards total completion. I'll post up a few pictures of these parts when I get a chance.
So, next is to move everything over to the painting bench.
I'll finish the inside of the front hull and then start painting the figures. Once the figures are done, I'll be able to install the driver and close-up the hull. I'll also add the radio operator and radio. This sequence will hopefully mitigate the effects of handling the carrier as I move on to finishing the exterior later.
(I anticipate a lot of handling as I install the radio operator and radio. This could be rough on the exterior finish, so do the figure installation first followed by the exterior finish.)
Happy modeling!
@ Alan: George definitely deserves to see his name in public in connection with this kit. The Riich kit certainly falls into the "craftsman" area - definitely not a "shake and bake" or weekend project. But if someone wants an accurate rendition of the Universal Carrier, this is the kit he should tackle. George Moore played a large part in making this true.
@ Keith: I donno, Keith. I'm at the limits of my meager talents as it is. I'm lucky to keep from making gluey finger prints all over. I think installing a light bulb in the number plate is beyond me...

So, only a quick up-date right now. Hopefully some more photos later, but at the moment, here's where the carrier project stands.

This is an initial composition test to check on the relative sizes of the main components of the planned display. The hull front is still just dry-fit pending installation of the driver. The model is really starting to look like a Universal Carrier now, though...
The paper tag with the engine data is a mock up to get a better idea of how large or small that should be. I plan to display the carrier with the engine compartment top off to the side so that the engine details can be seen.
I have some fairly firm ideas for the terrain and other display elements and will show those as I mock them up, too. Right now, I'm just testing various arrangements to get a better idea of how the overall space will work. Smaller is better, but there needs to be space for a couple of other elements needed for visual balance.
In regards to the rest of the build - I've completed all of the construction. There are still a bunch of sub-assemblies and parts that will be finished and installed as the carrier moves towards total completion. I'll post up a few pictures of these parts when I get a chance.
So, next is to move everything over to the painting bench.
I'll finish the inside of the front hull and then start painting the figures. Once the figures are done, I'll be able to install the driver and close-up the hull. I'll also add the radio operator and radio. This sequence will hopefully mitigate the effects of handling the carrier as I move on to finishing the exterior later.
(I anticipate a lot of handling as I install the radio operator and radio. This could be rough on the exterior finish, so do the figure installation first followed by the exterior finish.)
Happy modeling!

Keef1648

Joined: January 23, 2008
KitMaker: 1,240 posts
Armorama: 1,192 posts

Posted: Wednesday, October 09, 2013 - 11:19 PM UTC
Great to see your Carrier up close last night Mike.
A really first class piece of work and well worth the effort you are putting into this kit.....
As always you inspire us all to do better and above all 'enjoy' our hobby....
Looking forward to seeing what you do with the odball paint colors you picked up during the meeting.
Keith.
A really first class piece of work and well worth the effort you are putting into this kit.....
As always you inspire us all to do better and above all 'enjoy' our hobby....
Looking forward to seeing what you do with the odball paint colors you picked up during the meeting.
Keith.


jrutman

Joined: April 10, 2011
KitMaker: 7,941 posts
Armorama: 7,934 posts

Posted: Thursday, October 10, 2013 - 01:35 AM UTC
Can't wait to see what kind of display you will be cooking up for this little jewel.
J
J

jrutman

Joined: April 10, 2011
KitMaker: 7,941 posts
Armorama: 7,934 posts

Posted: Sunday, October 13, 2013 - 01:21 AM UTC
C'mon man,how long ya gonna make me wait for a bren fix??
J
J

SdAufKla

Joined: May 07, 2010
KitMaker: 2,238 posts
Armorama: 2,158 posts

Posted: Sunday, October 13, 2013 - 11:59 AM UTC
@ Keith: Oddball colors is right! The one bottle I special ordered was based on what I'm pretty sure was a typo in the paint mix discussion I was referencing.
At any rate, I think I have the "light mud" color mix sorted out. More on that when I get to the actual camouflage painting.
Still, that light sky blue gray threw me for a loop!
@ Jerry: Sorry I left you "Jonesin'" bro! Slow progress coupled with a lot of business to take care of for our local AMPS chapter (newsletter, meeting agenda, launching our new forum, etc) meant that I didn't think I had much to show that was "/news worthy."
However, since you've asked, here's a little up-date. Sorry there's not too much to show, but hopefully it'll keep ya going... I hope to have some of the goooood stuff soon!
So, after I finished cleaning up all of the parts and readying everything left on the carrier for finishing, I did some preliminary painting on the rear hull sub-assemblies.




I wanted to get the "factory" colors on these sub-assemblies before I assembled them and moved to the weathering and field-applied camouflage. The way these parts overhang each other means that there are a lot of areas that would be hard to reach even with an airbrush. I'll also do some preliminary weathering up under the "luggage shelf" and in the final drive area before I permanently glue all this up.
Since I had the dark green mixed up, I went ahead and used it all up on a couple of other sub-assemblies, like the sand shields and the engine compartment top.


The sand shields have been thinned by sanding on their reverse sides. It doesn't show up in these photos, but they're almost paper thin now. This was pretty easy to do just using a small sanding block and patience.
The engine compartment top still has its Pyrene fire extinguisher to add. The Riich PE fire extinguisher mount is very nice, but it's also a fairly complicated folding job. I also found that I had to move my mount slightly to the right (about the width of the molded on mounting bolts) to avoid the long stowage box. It's entirely possible that this requirement was my own doing given the difficulty I had folding the mount. But, hey, what's a 1/3 of mm between friends?
There's quite a bit more painting and weathering left to do in the engine compartment top, but you can see all the parts on it now.
My main effort over the last few building session has been to finish the upper front hull so that it's ready to close up once the driver is painted.

I did a little extra work on the instrument cluster since it has such a prominent place. I replaced the molded on toggle switches with bits of brass wire and added a half-wing-nut switch from left over DML Pz IV parts. This required shaving off the molded on wing-nut switch. I also added a large button to the center of the starter switch.
The gauges are done with the kit decals. It did take several applications of decal setting solution to get these to settle into the molded on instrument faces. I finally resorted to Testor's Decal Solvent - Mocro Sol just wasn't getting it done.

The upper front hull is close to being done. Obviously, I still have to add the instrument cluster (when it's finished), and the entire sub-assembly will get a "dust" glaze followed by Testor's Dull Coat.
Once this is done, I'll get serious with painting the figures.
The Devil is in the details... Slow going for the time being.
Happy modeling!
At any rate, I think I have the "light mud" color mix sorted out. More on that when I get to the actual camouflage painting.
Still, that light sky blue gray threw me for a loop!

@ Jerry: Sorry I left you "Jonesin'" bro! Slow progress coupled with a lot of business to take care of for our local AMPS chapter (newsletter, meeting agenda, launching our new forum, etc) meant that I didn't think I had much to show that was "/news worthy."
However, since you've asked, here's a little up-date. Sorry there's not too much to show, but hopefully it'll keep ya going... I hope to have some of the goooood stuff soon!
So, after I finished cleaning up all of the parts and readying everything left on the carrier for finishing, I did some preliminary painting on the rear hull sub-assemblies.




I wanted to get the "factory" colors on these sub-assemblies before I assembled them and moved to the weathering and field-applied camouflage. The way these parts overhang each other means that there are a lot of areas that would be hard to reach even with an airbrush. I'll also do some preliminary weathering up under the "luggage shelf" and in the final drive area before I permanently glue all this up.
Since I had the dark green mixed up, I went ahead and used it all up on a couple of other sub-assemblies, like the sand shields and the engine compartment top.


The sand shields have been thinned by sanding on their reverse sides. It doesn't show up in these photos, but they're almost paper thin now. This was pretty easy to do just using a small sanding block and patience.
The engine compartment top still has its Pyrene fire extinguisher to add. The Riich PE fire extinguisher mount is very nice, but it's also a fairly complicated folding job. I also found that I had to move my mount slightly to the right (about the width of the molded on mounting bolts) to avoid the long stowage box. It's entirely possible that this requirement was my own doing given the difficulty I had folding the mount. But, hey, what's a 1/3 of mm between friends?
There's quite a bit more painting and weathering left to do in the engine compartment top, but you can see all the parts on it now.
My main effort over the last few building session has been to finish the upper front hull so that it's ready to close up once the driver is painted.

I did a little extra work on the instrument cluster since it has such a prominent place. I replaced the molded on toggle switches with bits of brass wire and added a half-wing-nut switch from left over DML Pz IV parts. This required shaving off the molded on wing-nut switch. I also added a large button to the center of the starter switch.
The gauges are done with the kit decals. It did take several applications of decal setting solution to get these to settle into the molded on instrument faces. I finally resorted to Testor's Decal Solvent - Mocro Sol just wasn't getting it done.

The upper front hull is close to being done. Obviously, I still have to add the instrument cluster (when it's finished), and the entire sub-assembly will get a "dust" glaze followed by Testor's Dull Coat.
Once this is done, I'll get serious with painting the figures.
The Devil is in the details... Slow going for the time being.
Happy modeling!
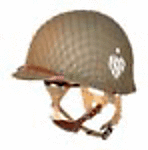
Big-John

Joined: August 12, 2010
KitMaker: 731 posts
Armorama: 711 posts

Posted: Sunday, October 13, 2013 - 02:27 PM UTC
Once again, another outstanding update.
I went to a local model show yesterday and had one of these kits in my hands. I ended up putting it back down on the table.
I just love the idea of the engine data plate. I’m a Ford man and have about 7 or so real Flathead V8 engines stuffed in my garage ranging from 1935 to 1949.
Flatheads Forever!!!
I went to a local model show yesterday and had one of these kits in my hands. I ended up putting it back down on the table.
I just love the idea of the engine data plate. I’m a Ford man and have about 7 or so real Flathead V8 engines stuffed in my garage ranging from 1935 to 1949.
Flatheads Forever!!!
Posted: Sunday, October 13, 2013 - 09:08 PM UTC
Hi Mike,
Excellent work, this is looking very sharp. Terrific stuff.
Cheers
Al
Excellent work, this is looking very sharp. Terrific stuff.
Cheers
Al




Keef1648

Joined: January 23, 2008
KitMaker: 1,240 posts
Armorama: 1,192 posts

Posted: Sunday, October 13, 2013 - 11:25 PM UTC
Quoted Text
@ Keith: Oddball colors is right! The one bottle I special ordered was based on what I'm pretty sure was a typo in the paint mix discussion I was referencing.
At any rate, I think I have the "light mud" color mix sorted out. More on that when I get to the actual camouflage painting.
Still, that light sky blue gray threw me for a loop!![]()
Happy modeling!
Odball color, yer durn tootin? Had me 'puggled'from the moment you asked for it but I have learned not to question your reasons as you seem to pull reference material out of thin air.

But then again, I am certain I shared some references to WW2 paint colors and the dates and timings orders for them, with you some time ago... May not cover Canuck items but still they may be helpful to you.
looking really good, now I will have to step up my efforts (bummer).
Keith.


jrutman

Joined: April 10, 2011
KitMaker: 7,941 posts
Armorama: 7,934 posts

Posted: Monday, October 14, 2013 - 01:53 AM UTC
Ah yes,read through the update and now my shakes have dissapaited.
This blog had me seriously thinking about getting one of Riiches Harley kits. I didn't want to bust my budget at Avenel Hobbies so I deffered the buy until next month. With my luck though,there won't be any left next month.
Thanks for posting buddy!
J
This blog had me seriously thinking about getting one of Riiches Harley kits. I didn't want to bust my budget at Avenel Hobbies so I deffered the buy until next month. With my luck though,there won't be any left next month.
Thanks for posting buddy!
J

SdAufKla

Joined: May 07, 2010
KitMaker: 2,238 posts
Armorama: 2,158 posts

Posted: Tuesday, October 15, 2013 - 11:47 AM UTC
@ John: The Ford engine really caught my imagination with this build.
The brand recognition, at least here in the US, is so strong that I think everyone can identify with it. That's one reason why I wanted to show the engine off, and I hope the "data plate" will help the viewer to intuitively understand the display.
We'll see...
@ Alan: Thank you, sir!
@ Keith: I've gone through my workshop with a fine tooth comb and simply cannot find that info sheet you gave me. Like you said, though, as soon as I finish, it'll be the first thing I pull off the bookshelf.
The issue has been with the "Light Mud" color. However, I think I now have a good Vallejo match for Starmer's Tamiya mix.
@ Jerry: Not too much with this next little up-date, but hopefully it'll tide you over a bit...
So, I've finished the upper front hull. It's now ready to glue on as soon as I have the driver painted.
I had intended to add the kit-supplied armored glass vision blocks, but they're slightly too large to fit. This fit problem is probably a factor of the paint inside the frame / openings. However, raw plastic is not an option. I also think that trying to trim them down and then polish out any resulting blemishes will be more work than making new parts.
I'm still thinking about what I'm going to do to replace them - either Micro Crystal Clear or .010 clear styrene sheet. More to follow...

I also added the Pyrene fire extinguisher behind the driver and added the wiring bundle that exits the chase next to the driver and curves up and into the space behind the instrument cluster.

I've also completed the engine compartment top. My plan is to display this off of the carrier, something like the initial mock-up posted earlier.

I've started under-coating the figures with acrylics, but there's not too much to show on that front yet. Hopefully I'll be able to post up some happy snaps of the crew in a few days.
'Til then, Happy modeling!
The brand recognition, at least here in the US, is so strong that I think everyone can identify with it. That's one reason why I wanted to show the engine off, and I hope the "data plate" will help the viewer to intuitively understand the display.
We'll see...
@ Alan: Thank you, sir!
@ Keith: I've gone through my workshop with a fine tooth comb and simply cannot find that info sheet you gave me. Like you said, though, as soon as I finish, it'll be the first thing I pull off the bookshelf.
The issue has been with the "Light Mud" color. However, I think I now have a good Vallejo match for Starmer's Tamiya mix.
@ Jerry: Not too much with this next little up-date, but hopefully it'll tide you over a bit...
So, I've finished the upper front hull. It's now ready to glue on as soon as I have the driver painted.
I had intended to add the kit-supplied armored glass vision blocks, but they're slightly too large to fit. This fit problem is probably a factor of the paint inside the frame / openings. However, raw plastic is not an option. I also think that trying to trim them down and then polish out any resulting blemishes will be more work than making new parts.
I'm still thinking about what I'm going to do to replace them - either Micro Crystal Clear or .010 clear styrene sheet. More to follow...

I also added the Pyrene fire extinguisher behind the driver and added the wiring bundle that exits the chase next to the driver and curves up and into the space behind the instrument cluster.

I've also completed the engine compartment top. My plan is to display this off of the carrier, something like the initial mock-up posted earlier.

I've started under-coating the figures with acrylics, but there's not too much to show on that front yet. Hopefully I'll be able to post up some happy snaps of the crew in a few days.
'Til then, Happy modeling!
Posted: Tuesday, October 15, 2013 - 12:22 PM UTC
Hi Mike,
A real pleasure watching this develop.
Al
A real pleasure watching this develop.
Al



SdAufKla

Joined: May 07, 2010
KitMaker: 2,238 posts
Armorama: 2,158 posts

Posted: Wednesday, October 16, 2013 - 02:17 PM UTC
@ Al: Thanks, as always. I appreciate the kind words.
I've moved on to painting the figures.
As some of you may know, I'm something of a traditionalist when it comes to figure painting. I work in artist oils over acrylic undercoats. Artist oils are one of the three main mediums used for figures - hobby enamels, acrylics and oils - and oils are the traditional medium used by most figure modelers until the advent of modern acrylics like Andrea or Vallejo.
Some of the earlier posts have shown the figure conversion work with the priming done with Tamiya XF-2 Flat White. I like starting with the uniform white since it shows clearly where any additional work is needed and any colors applied over it will show "true." Also, the white needs very little in the way of acrylic paint for the undercoating.
The acrylic undercoating helps with the oil paints in a couple of important ways. First, having a color close to the desired final color means that less oil paint is required to get good coverage and also that the primer color won't show through if the oil paint is brushed out too thin. Oil paints need to be brushed out just about as thin as possible or else it's very easy to get too much paint on the figure.
Sometimes the undercoat color can be used as part of the actual final shading and highlights. For instance, on these figures, their boots will be black, but I've undercoated them with a burnt sienna color. When I put the black oil paint on them, I can deliberately brush it out to a semi-transparent layer on the high points in order to get the underlying brown to show as if the leather is worn.
Also, because the acrylics are not affected by the oils or the mineral spirits used to thin them, any details first painted with acrylics can be incorporated into the final look. The acrylic details can also work as "place holders" for later details painted on with oils. Again, on these figures, I have blocked in the regimental shoulder flashes and division insignia with acrylics. I will paint over these with oils, but the acrylics will hold those shapes for me. If I screw up the oils over them, a moist brush will clean the oils off leaving the basic acrylic shapes intact.
Finally, undercoating with acrylics can help in establishing the color pallet to be used. The acrylic colors don't have to be exact matches, but they can be used to get ideas about how to vary colors and tones from item to item and figure to figure. Using thin acrylic coats can also help show where the clothing folds and shapes are as well as help the details to stand out.
Anyways, enough about the theory. If anyone has any questions, please don't hesitate to ask, but since most guys now use acrylics and a glazing technique, I won't spend much more time explaining my oil painting technique. There's not a lot of cross-over between the basics of the two.
Here are my carrier figures. The undercoating is pretty much done. I do still have a few small details that I'll pick out with acrylics, like the belt buckle on the officer / gunner figure. But essentially, they're ready for the oils now.



The figures are all wearing various khaki drill items with the driver and radio operator wearing the Airtex shirts.
They will be badged out as members of "Princess Louise's IV Dragoon Guards," the recce regiment of the Canadian 1st Infantry Division. The 4PLDG shoulder flash was one of those that incorporated the Dominion name into the flash - no separate "Canada" shoulder flashes.
The division insignia is in a very dark red right now, but it will be highlighted in lighter and brighter reds later.
I decided to make the "gunner" an officer just for variety. Also, I intend to mark the carrier as a HQ vehicle for B Squadron, which was heavily employed in southern Italy starting in September, 1943. At any rate, an officer makes sense in one of the squadron carriers equipped with a radio.
Happy modeling!
I've moved on to painting the figures.
As some of you may know, I'm something of a traditionalist when it comes to figure painting. I work in artist oils over acrylic undercoats. Artist oils are one of the three main mediums used for figures - hobby enamels, acrylics and oils - and oils are the traditional medium used by most figure modelers until the advent of modern acrylics like Andrea or Vallejo.
Some of the earlier posts have shown the figure conversion work with the priming done with Tamiya XF-2 Flat White. I like starting with the uniform white since it shows clearly where any additional work is needed and any colors applied over it will show "true." Also, the white needs very little in the way of acrylic paint for the undercoating.
The acrylic undercoating helps with the oil paints in a couple of important ways. First, having a color close to the desired final color means that less oil paint is required to get good coverage and also that the primer color won't show through if the oil paint is brushed out too thin. Oil paints need to be brushed out just about as thin as possible or else it's very easy to get too much paint on the figure.
Sometimes the undercoat color can be used as part of the actual final shading and highlights. For instance, on these figures, their boots will be black, but I've undercoated them with a burnt sienna color. When I put the black oil paint on them, I can deliberately brush it out to a semi-transparent layer on the high points in order to get the underlying brown to show as if the leather is worn.
Also, because the acrylics are not affected by the oils or the mineral spirits used to thin them, any details first painted with acrylics can be incorporated into the final look. The acrylic details can also work as "place holders" for later details painted on with oils. Again, on these figures, I have blocked in the regimental shoulder flashes and division insignia with acrylics. I will paint over these with oils, but the acrylics will hold those shapes for me. If I screw up the oils over them, a moist brush will clean the oils off leaving the basic acrylic shapes intact.
Finally, undercoating with acrylics can help in establishing the color pallet to be used. The acrylic colors don't have to be exact matches, but they can be used to get ideas about how to vary colors and tones from item to item and figure to figure. Using thin acrylic coats can also help show where the clothing folds and shapes are as well as help the details to stand out.
Anyways, enough about the theory. If anyone has any questions, please don't hesitate to ask, but since most guys now use acrylics and a glazing technique, I won't spend much more time explaining my oil painting technique. There's not a lot of cross-over between the basics of the two.
Here are my carrier figures. The undercoating is pretty much done. I do still have a few small details that I'll pick out with acrylics, like the belt buckle on the officer / gunner figure. But essentially, they're ready for the oils now.



The figures are all wearing various khaki drill items with the driver and radio operator wearing the Airtex shirts.
They will be badged out as members of "Princess Louise's IV Dragoon Guards," the recce regiment of the Canadian 1st Infantry Division. The 4PLDG shoulder flash was one of those that incorporated the Dominion name into the flash - no separate "Canada" shoulder flashes.
The division insignia is in a very dark red right now, but it will be highlighted in lighter and brighter reds later.
I decided to make the "gunner" an officer just for variety. Also, I intend to mark the carrier as a HQ vehicle for B Squadron, which was heavily employed in southern Italy starting in September, 1943. At any rate, an officer makes sense in one of the squadron carriers equipped with a radio.
Happy modeling!
Posted: Wednesday, October 16, 2013 - 10:53 PM UTC
A link for anyone interested.
http://www.canadiansoldiers.com/organization/fieldforces/casf/1stdivision.htm
Hi Mike, figures are looking excellent. I may be wrong but I would have thought the Soldiers boots should have been black? Officers boots were brown but as far as I know the Canadians used the same ammo boots as the British.
Either way lovely work on both the vehicle and the figures. Terrific amount of detail and a nice alternative setting the scene in the Med.
Highly informative and interesting blog and excellent workmanship on the kit and figures. A real gem of a build.
Al
http://www.canadiansoldiers.com/organization/fieldforces/casf/1stdivision.htm
Hi Mike, figures are looking excellent. I may be wrong but I would have thought the Soldiers boots should have been black? Officers boots were brown but as far as I know the Canadians used the same ammo boots as the British.
Either way lovely work on both the vehicle and the figures. Terrific amount of detail and a nice alternative setting the scene in the Med.
Highly informative and interesting blog and excellent workmanship on the kit and figures. A real gem of a build.
Al


Keef1648

Joined: January 23, 2008
KitMaker: 1,240 posts
Armorama: 1,192 posts

Posted: Wednesday, October 16, 2013 - 11:19 PM UTC
Great stuff Mike and I look forward to seeing all of this on Saturday.
@ Alan, I don't think Mike has finished the Boots and based on his enormous and personal amount of knowledge of Canadians in WW2 he will end up with the correct, issued color..
He has a a complete uniform set in his miniature museum for a starter
Keith.
@ Alan, I don't think Mike has finished the Boots and based on his enormous and personal amount of knowledge of Canadians in WW2 he will end up with the correct, issued color..
He has a a complete uniform set in his miniature museum for a starter

Keith.

![]() |