This guy is gonna be a real problem child!
The first thing necessary was to make the duck boards that sit on the floor of the carrier. The radio operator SHOULD (!) have his feet resting on the duck board on his side of the fighting compartment.
The kit parts, F36 and F37, were fairly uninspiring, so I made replacements by laminating thin wood (used to wrap cigars) on to some .010 styrene. After painting these the base dark green color, I used some fine steel wool to rub some of the paint off and expose the wood grain.
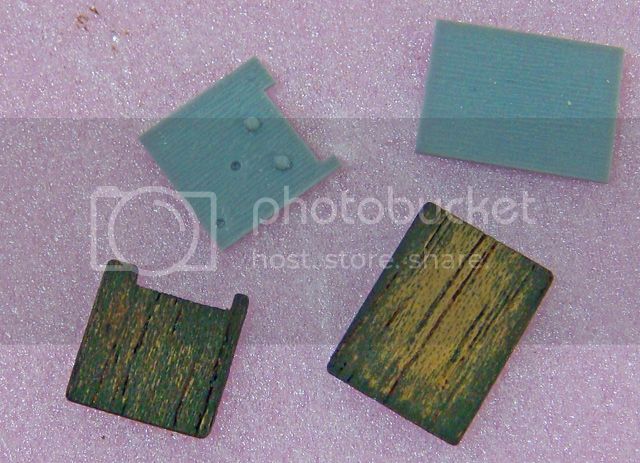
I already had the radio operator's seat cushion, kit part B6, in initial paint, but it was so bulky that I also painted up a spare cushion B7 (intended for the radio operator's back).
(The kit has 2 B sprues, so there are doubles of both of these parts.)
A quick test fit of the radio operator's legs showed that not only are they spread too wide to fit into the compartment, but if the B6 cushion is used, his feet cannot touch the duck board floor.
My first change was to move his knees closer together by trimming the two halves at a slight angle. This got his legs into the compartment, but the kit sculpted pose has him sitting at "attention" - very unnatural looking.
So, I pried his legs apart, move his right leg and hip down so that this knee was pointing more forward. I then cut his right knee apart and moved his lower leg to point forward. Both of his feet were cut off and the toes pointed down in a more natural position.
In order to get him to sit flat on the seat cushion, B7, I had to trim the back of his right thigh and buttock (after back filling the hollow kit parts with styrene). This looks odd in the photos below, but keep in mind that some of this in real life would be the back of his thigh "squishing" as the leg muscle relaxed. Also, the real seat cushion would "crush" under his weight. So the material I removed, in real life, would be accounted for by these two action.
Once positioned in the model, this area of his leg will be invisible to the viewer.
In this photo, you can see the reposed legs and the two seat cushions (B6 and B7) for comparison.
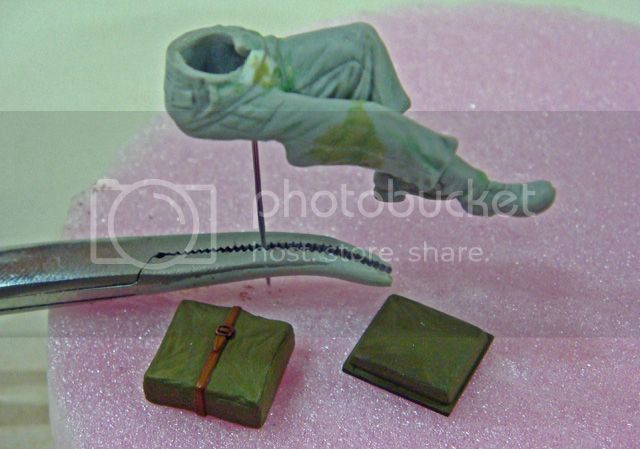
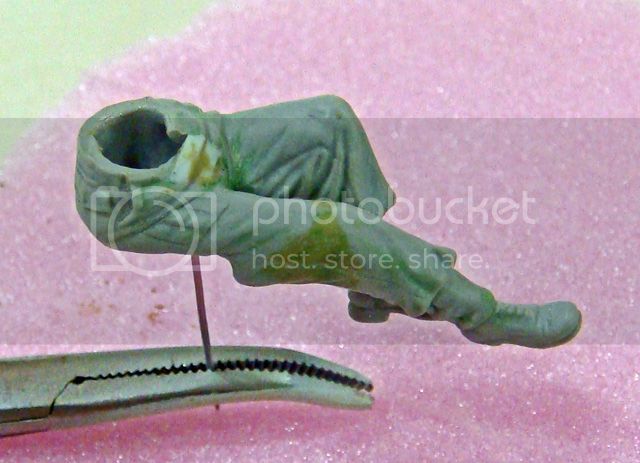
Now that I have the radio operator's legs posed, I now have to fit him and the radio together.
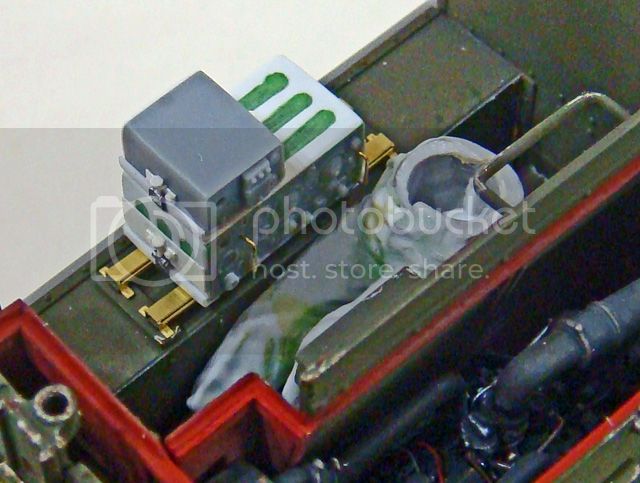
Here you can see just how little room there is for the operator and his equipment. Also, I want to use the guard on the radio, so I know now that I'll have to grind away a bit of the right hip, add the material back with two-part epoxy putty, and then re-sculpt the area to account for the bars on the guard.
I'll cover the radio stuff in the next post...